E.cut yes, other not !!
WHY MORE THAN 200 CUSTOMERS IN EUROPE KEEP BUYING ECUT ?
“E.cut™ yes, others not !!!”
E.cut™, unlike others who appear, disappear and reappear with other names, has been present for almost 20 years in the European market with these wonderful machines.
The manufacturer is one of the largest and appears “in the clear.” , without changing its name every few years.
Baoma’s website reads : “… the company has obtained two certifications : ISO9001:2000 Quality System Certification and ISO14001:1996 Environmental System Certification, rarely acquired by other companies in the same industry, and export quality authentication. Baoma is professionally engaged in the development, production and sales of CNC&EDM machines under the slogan of “let’s start now to create the future,” focusing on organizing and promoting a highly efficient team that holds independent development capacity. It has obtained five national patents and two gold awards, and has been honored by the central authority as a “national consumer’s reliable product” and a “satisfied enterprise of product quality after-sales service” for several years.”
See : Baoma, and Suzhou-Baoma
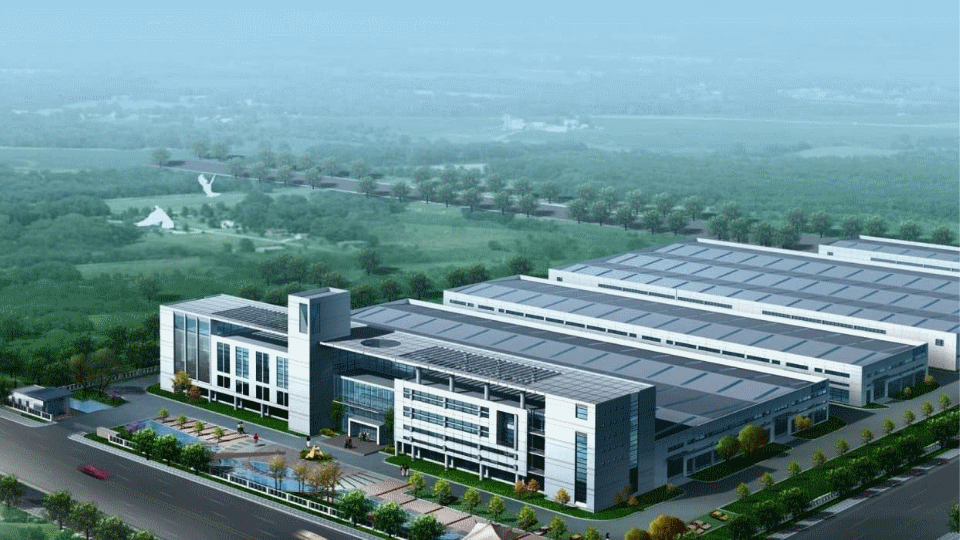
“E.cut yes, others no !!!”
Genesi has obtained 3 European patents , and makes many additions and modifications to the original machines.
Because as they are born, the machines are suitable for markets and environments where technology, safety and abmbient standards are not the same as in Europe.
It is the use of the machines that suggests adaptations to the way we operate in Europe !
We use them to make our customers’ parts.
We use them to examine with his parts what is the model, ( among more than 80 ) most suitable for his needs.
We use them to test special machining, and to provide the best working parameters.
And there’s nothing better than using the machines to learn what modes and working parameters are optimal for different customers’ needs.
It’s not the removal speed, often used as a lure mirror, to evaluate a machine !
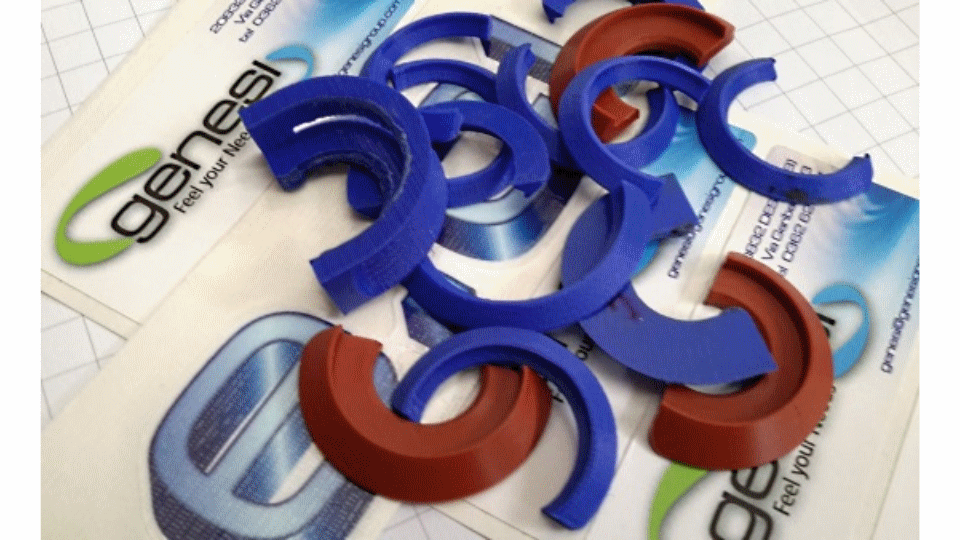
“E.cut yes, others no !!!”
Manuals are one of the most “E.cut yes, others no !” topics.
The E.cut manuals, (over 400 pages), are in CHM format, i.e., the original Windows format, and can also be had as PDFs. They are loaded and viewable directly on the machine even while it is working.
Copied to a flash drive, they can be viewed on any PC, even in the office or at home. Transferred to a cell phone, they can be viewed there as well.
Both the graphics program, (Autocad 2005 ) and the CNC can be uploaded to other PCs, and the paths developed even in the office. The industrial PC that serves as the CNC is networked, so program transmission is immediate.
Detailed explanations, many, many pictures, even in 3D, videos, and image sequences of malfunctions and how to intervene, have been developed and updated for 15 years with the goal of making the operator “autonomous.”
The adoption of Window 10 Pro with regular licensing,allows for secure remote assistance. In addition, remotely, from the office, or from home, can be controlled the working phases, the progress, and it is possible to intervene to change the cutting parameters.
Operator support, especially in the initial phase, is immediate and in real time.

“E.cut yes, others no !!!”
We perform tests and trials on customers’ and potential customers’ parts and materials, because Ecut is an investment asset, and it has to return to the customer for his parts, for his machining.
We always invite people to see the machines at our workshop or at customers who already own a model similar to the one we will propose. We have more than 80 models, ( no one has such an extensive range ), so we are able to provide the most suitable machine.
We try to figure out together with him what are the most convenient modes and working parameters for the work that HE has to follow, we do not just show the maximum speed of removal .
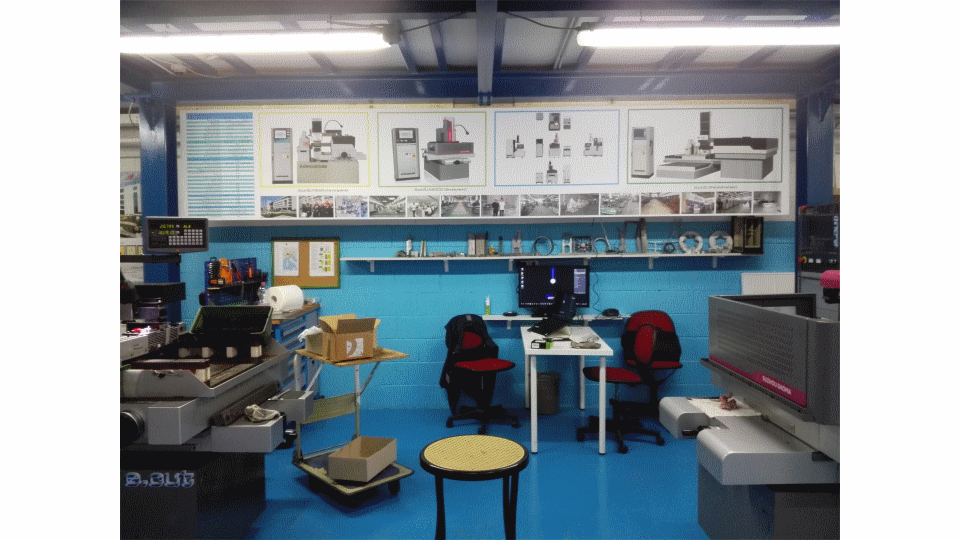
E.cut yes, others no !!!”
Only E.cut is always present at the world’s most important machine tool fair, EMO in Hannover.
Others attend only once. Often because after a few years … they no longer exist !!!
Since 2017, punctually, Baoma and Genesis have been showing what’s new, and illustrating the features of wire erosion cutting technology.
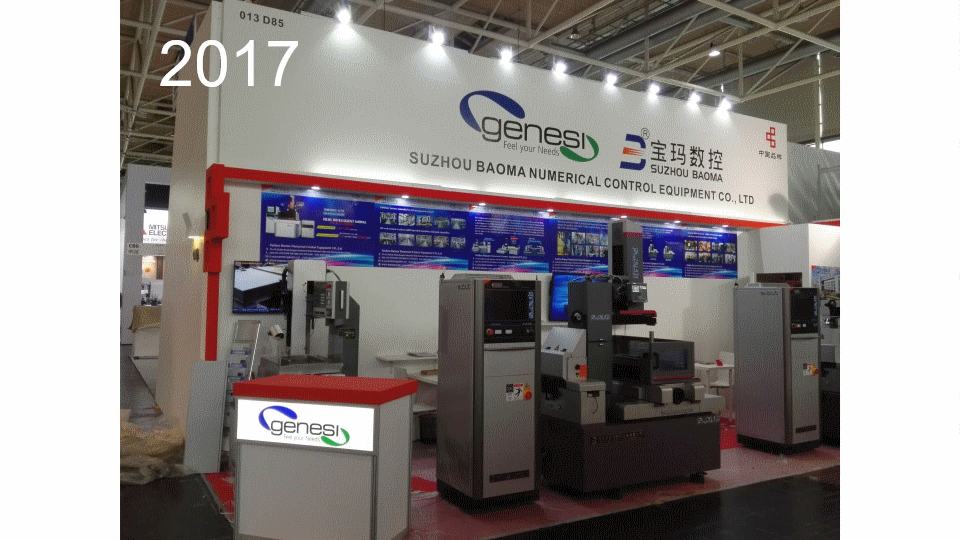
E.cut ™ is just Genesi, if it’s not E.cut ™ it’s not the same !
E.cut™ at Kilometer Zero – From fairs, exhibition, end of rental –
Ask if your E.cut™ is there.