
Ecutting, a new way of metalworking–simple, cheap, precise !
LARGE WORKPIECES AND HIGH THICKNESSES
The processing of large workpieces is facilitated by the high wire flow speed, (more than 100 times compared to conventional wire erosion), drop washing, without any immersion tank.
Whether with small machines with cutting heights of 500mm and capacities of 300 kg, up to machines with strokes of 2000 x 1200 x H 800mm and capacities of up to 5000 kg, the low operating cost makes Ecut technology advantageous.
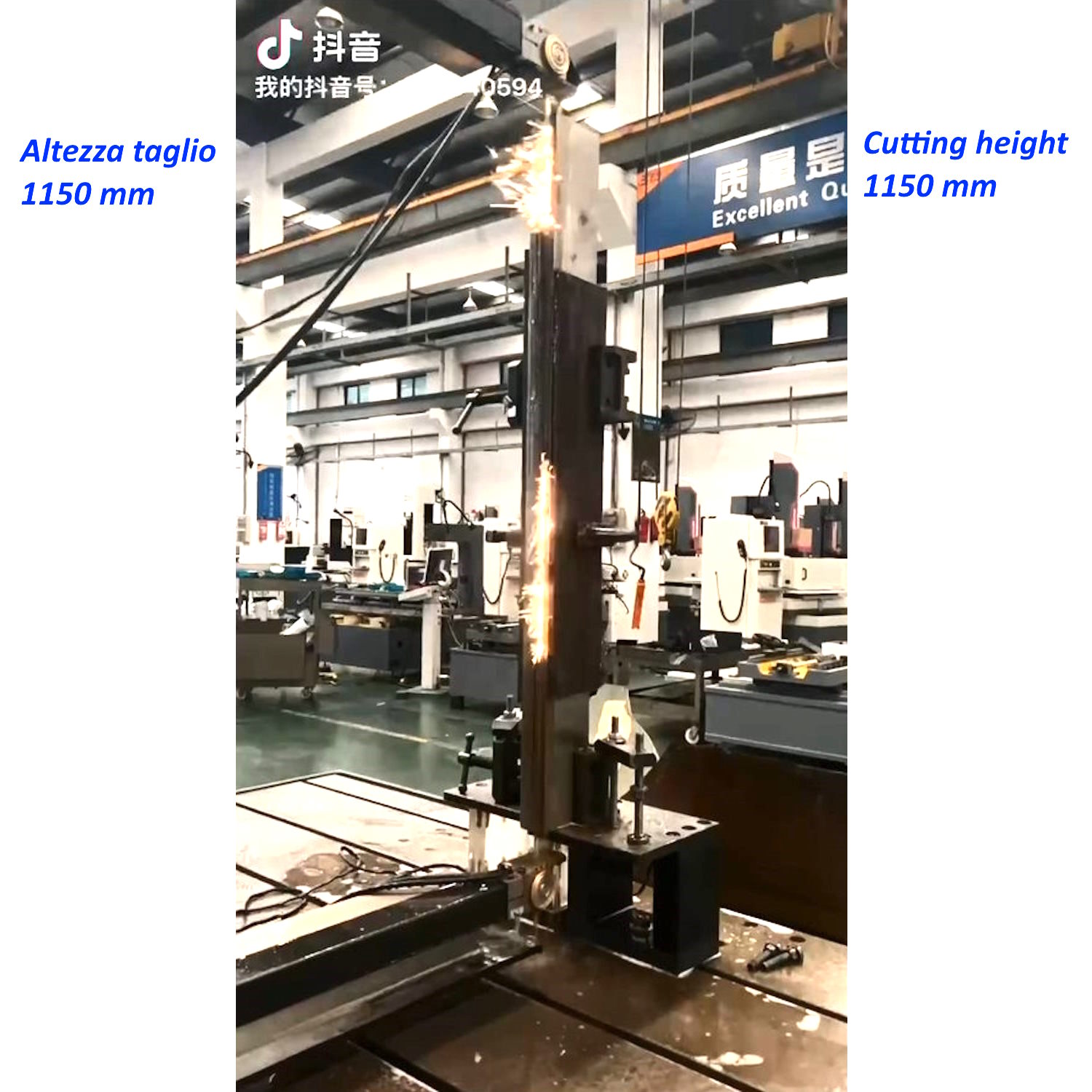
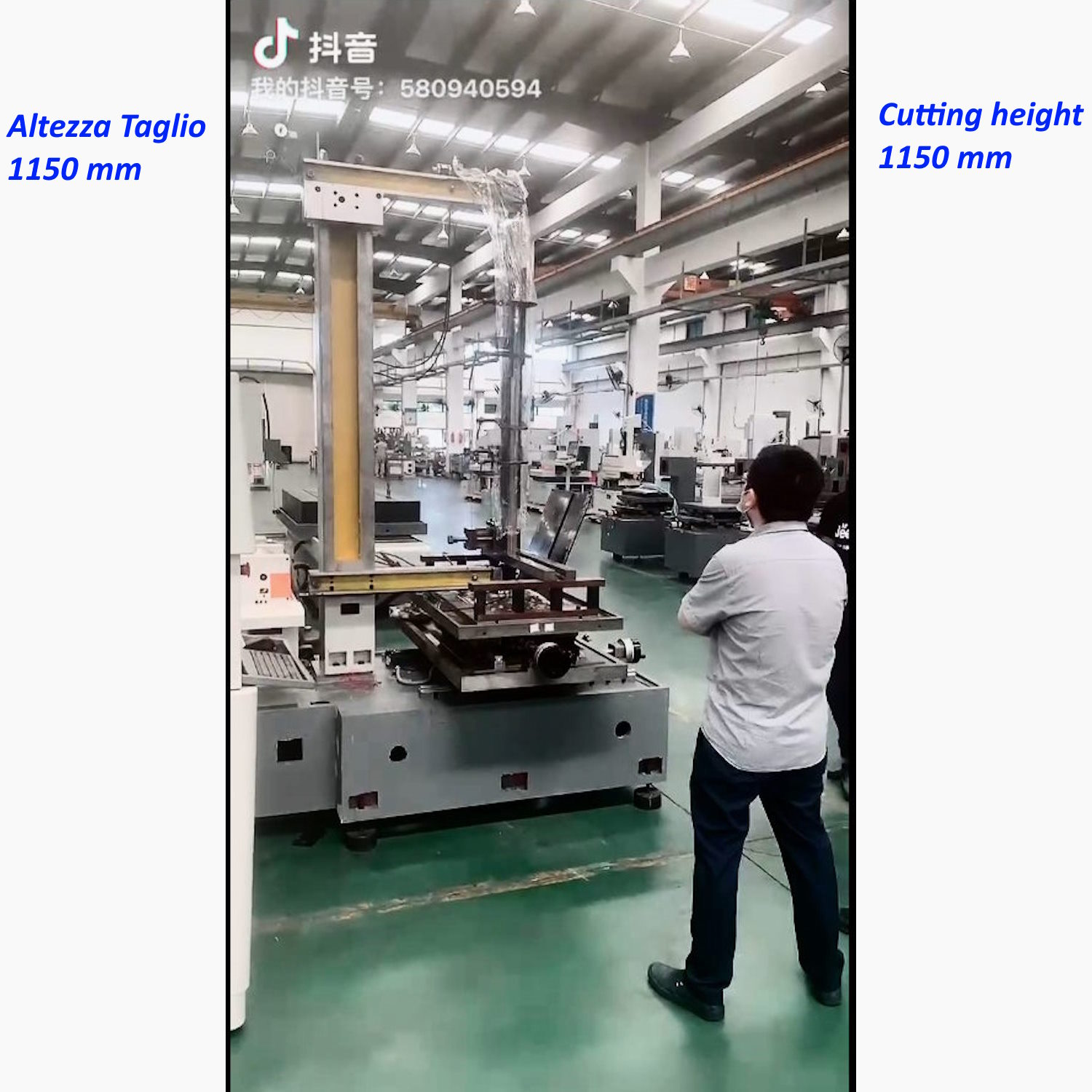
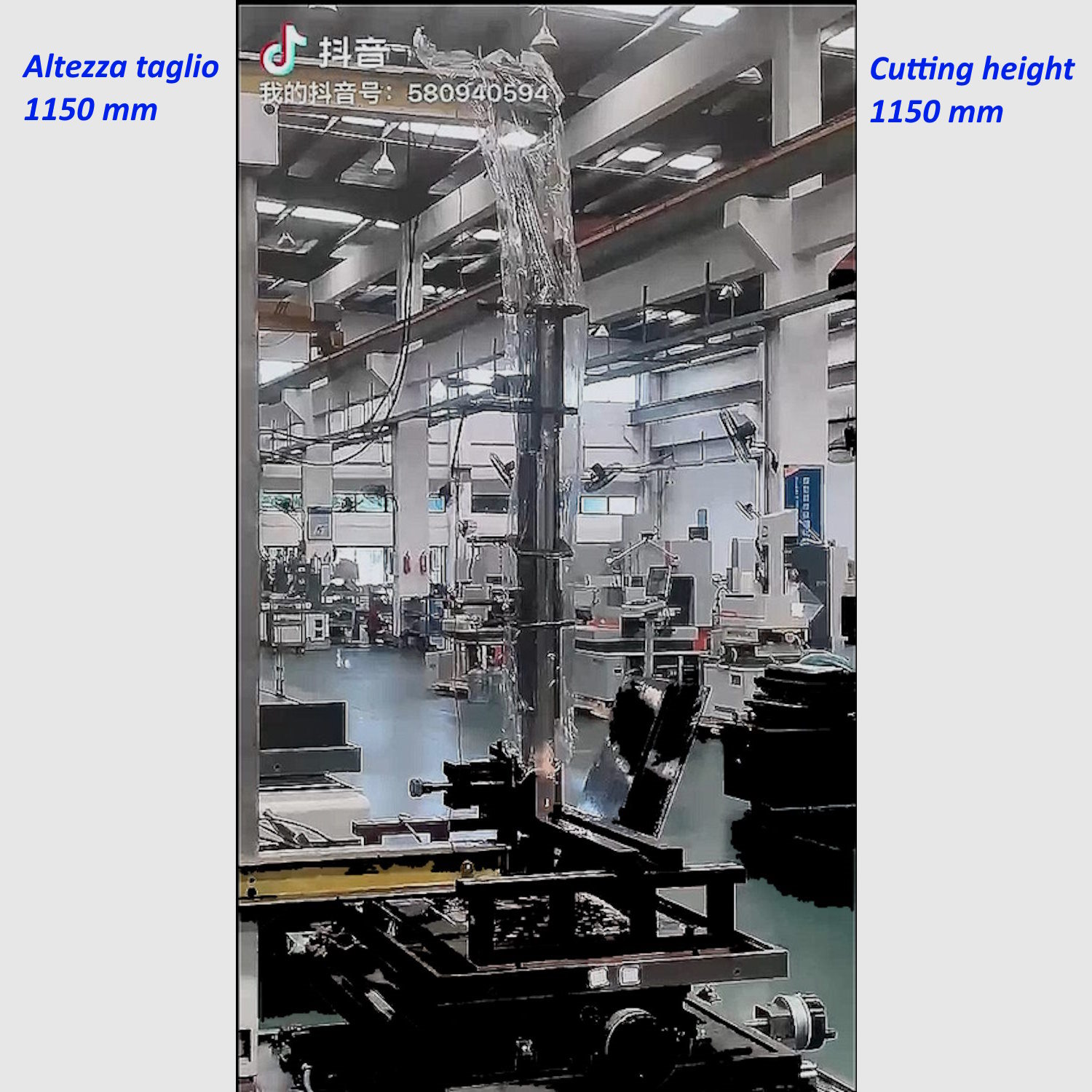
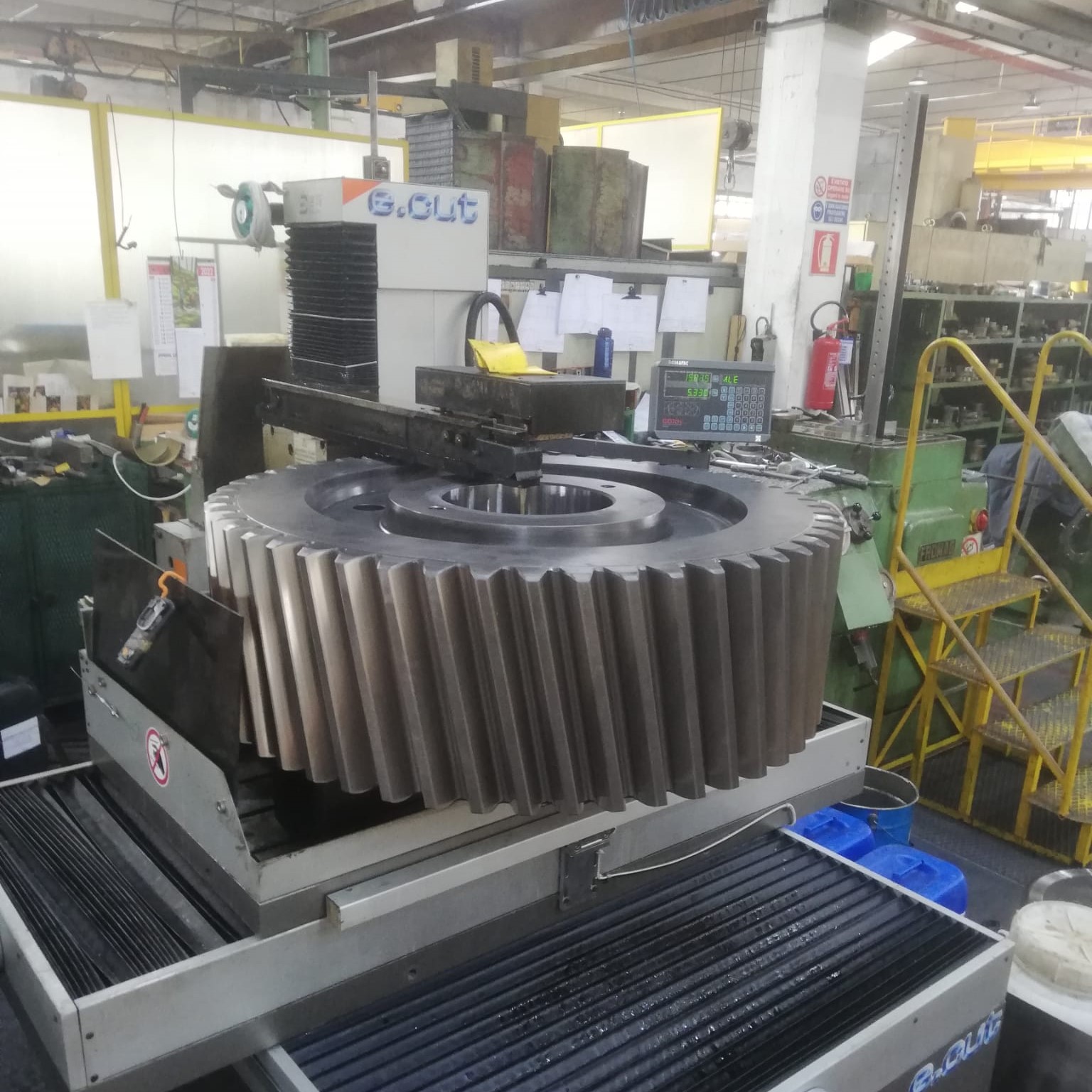
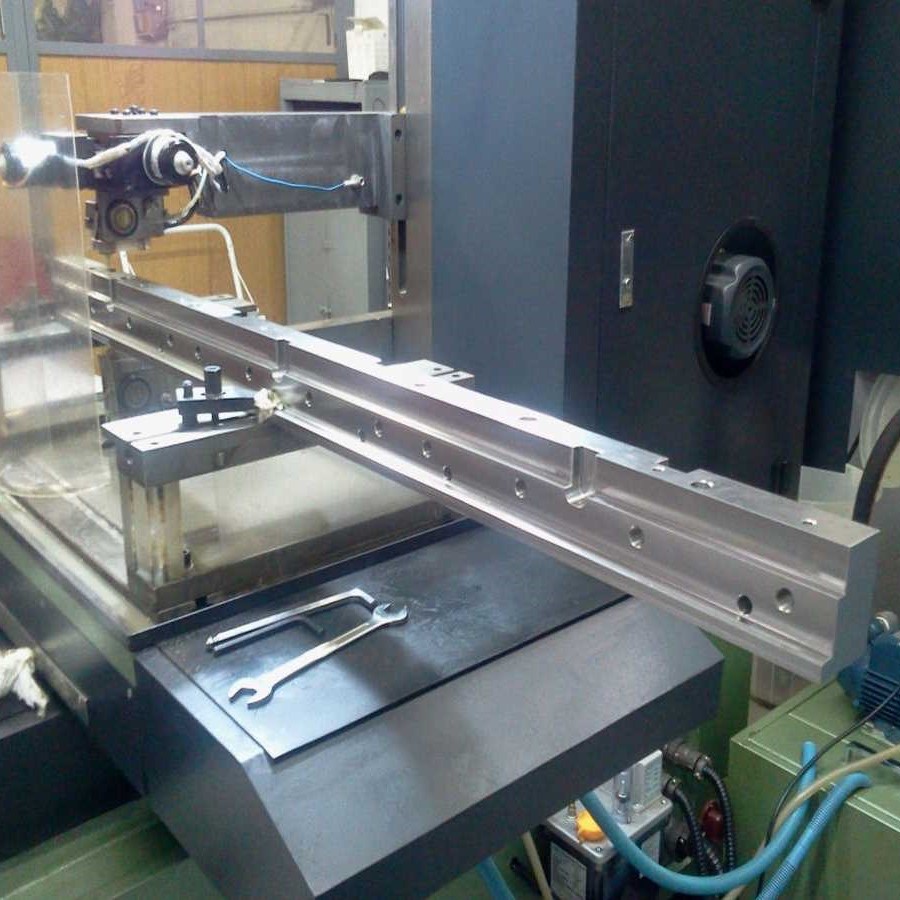
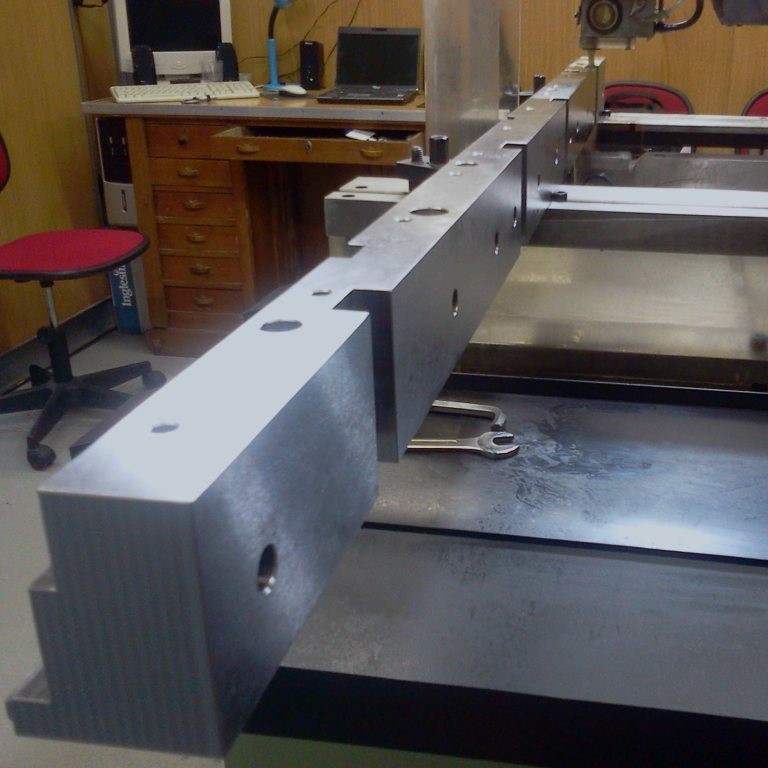
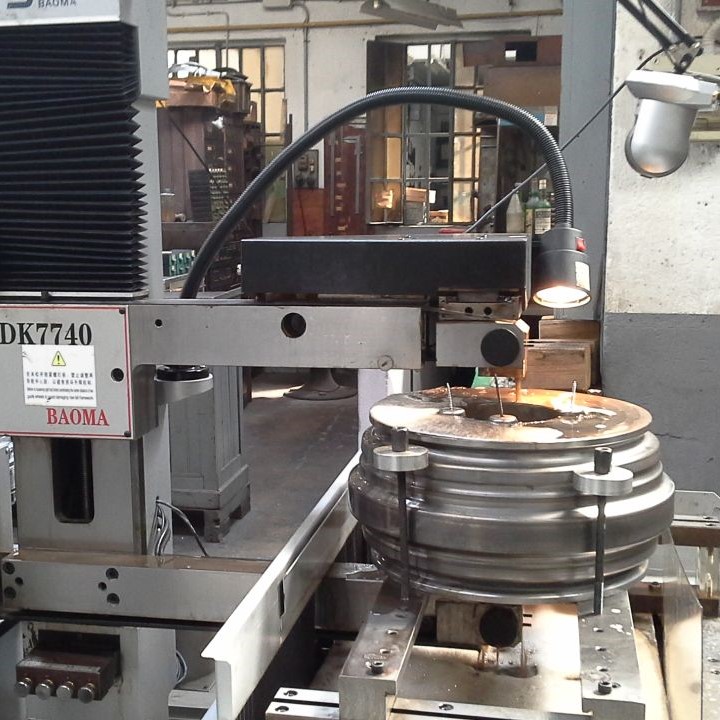
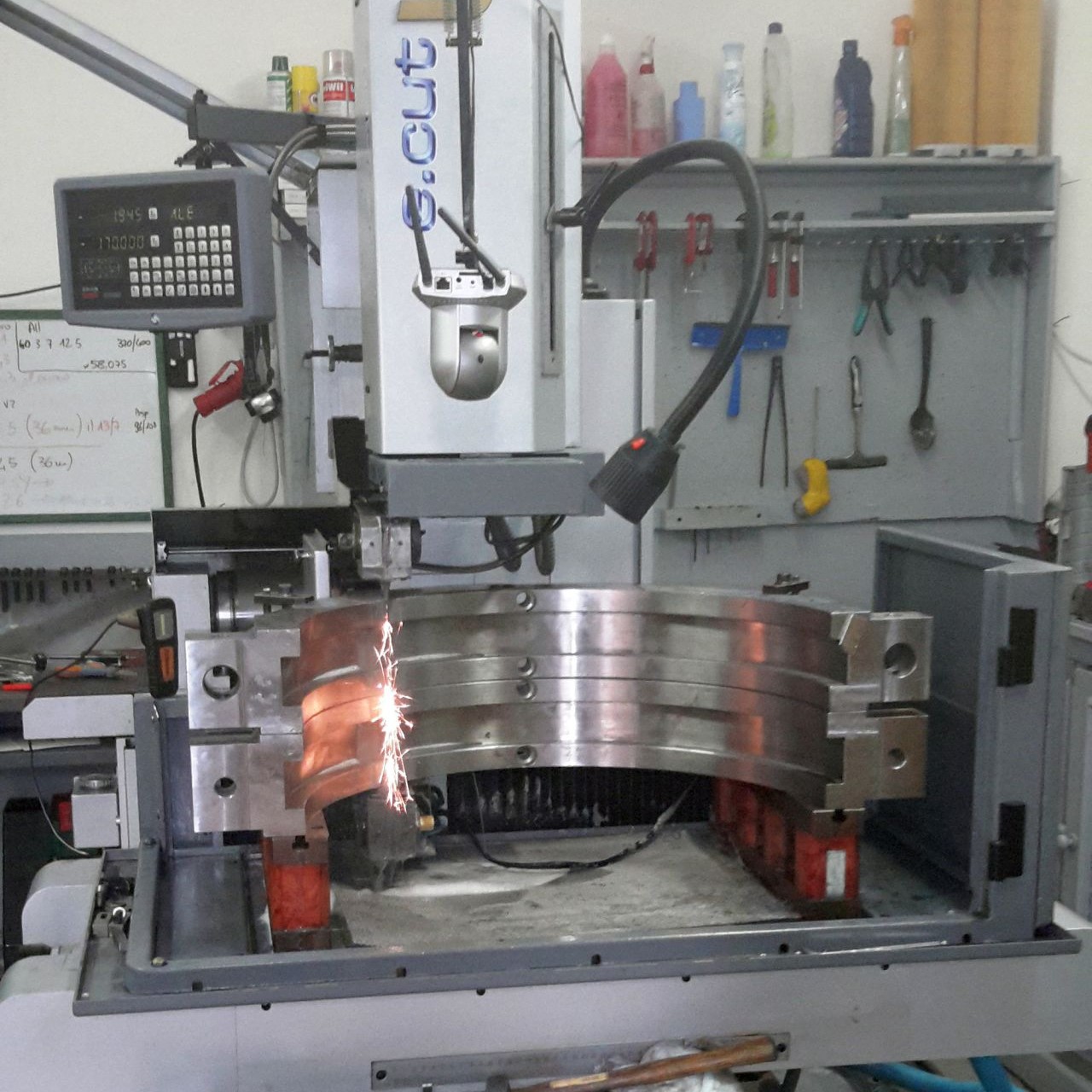
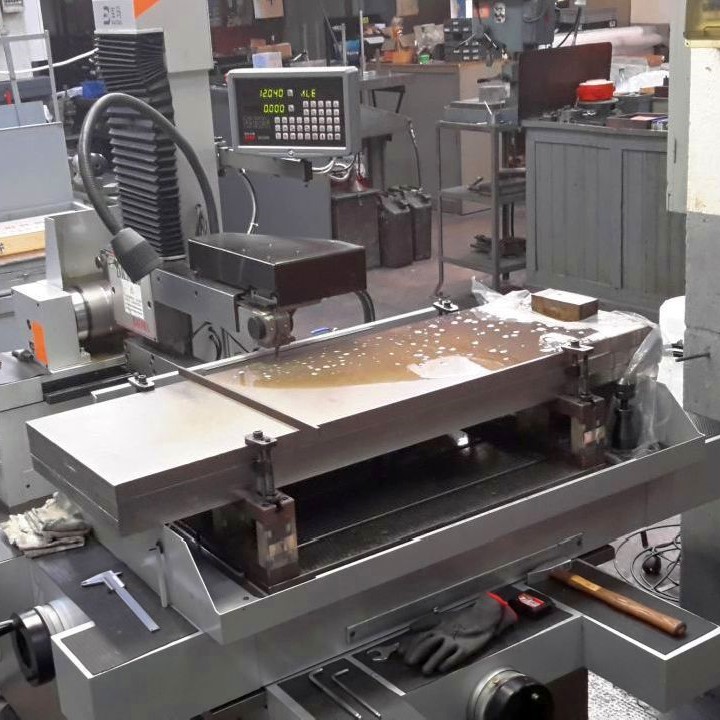
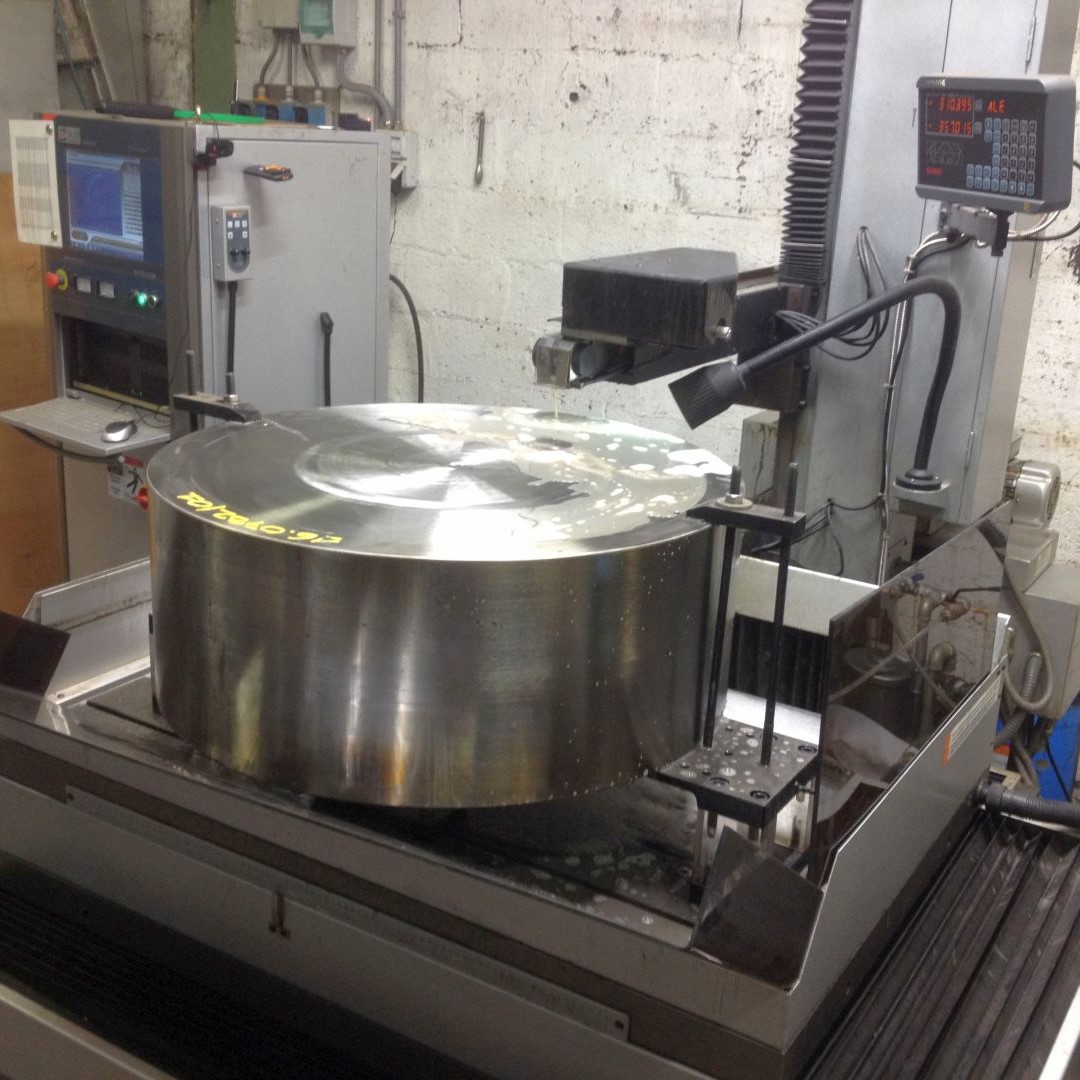
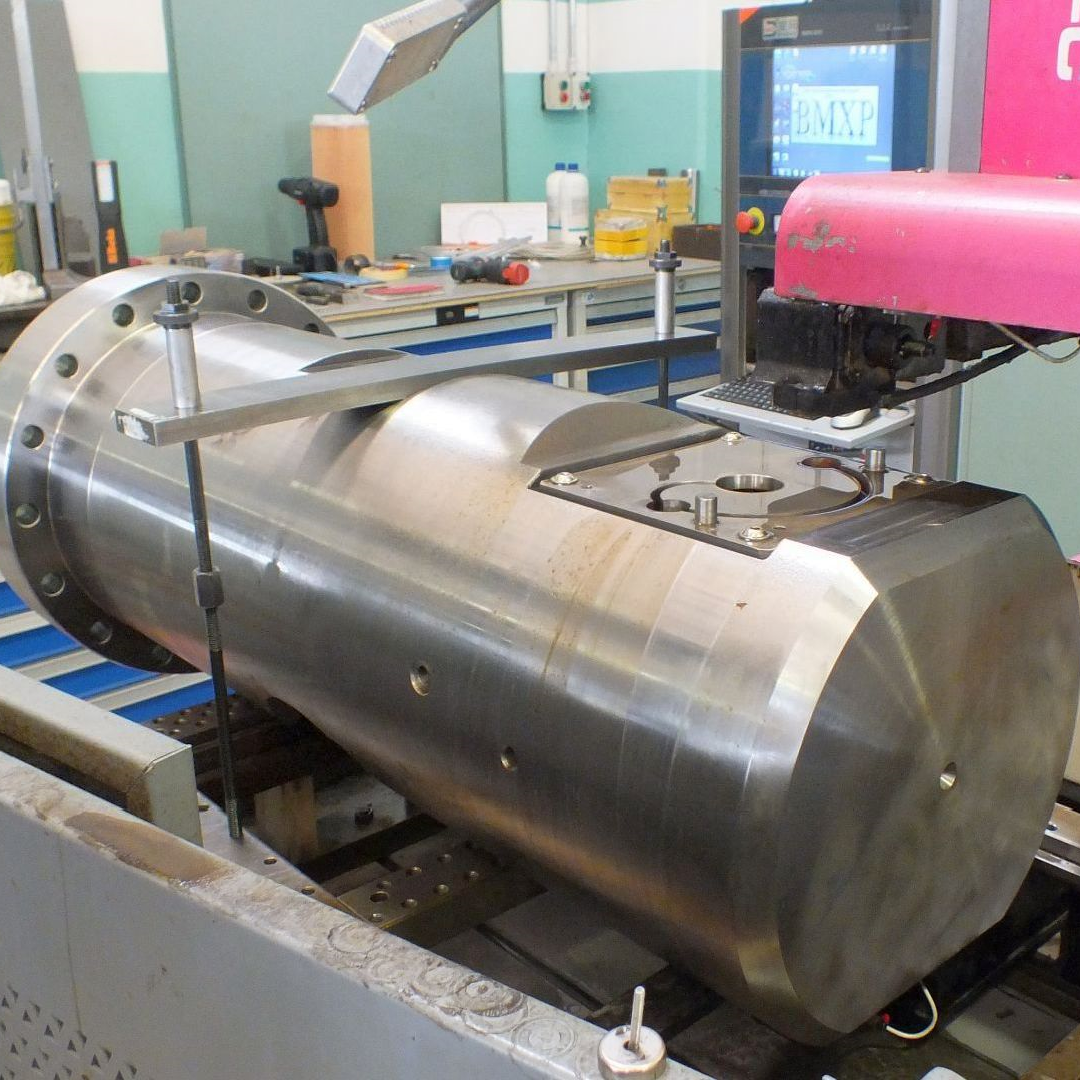
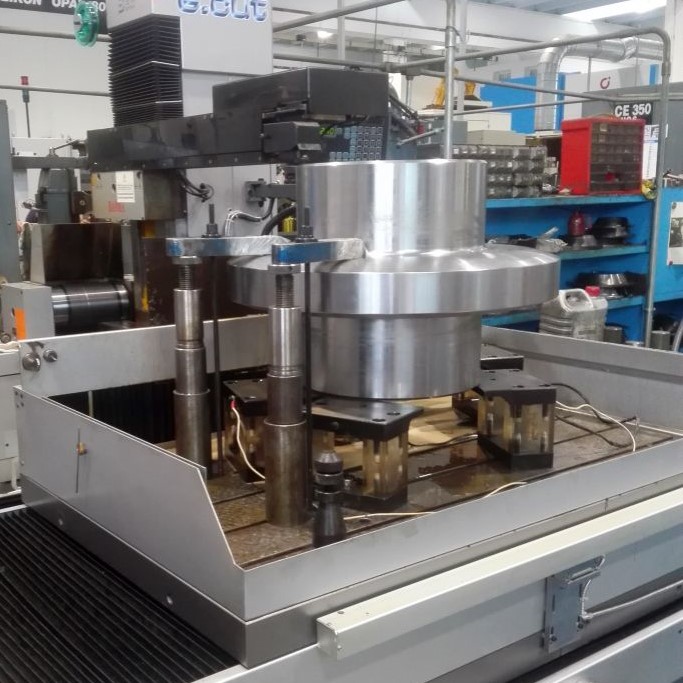
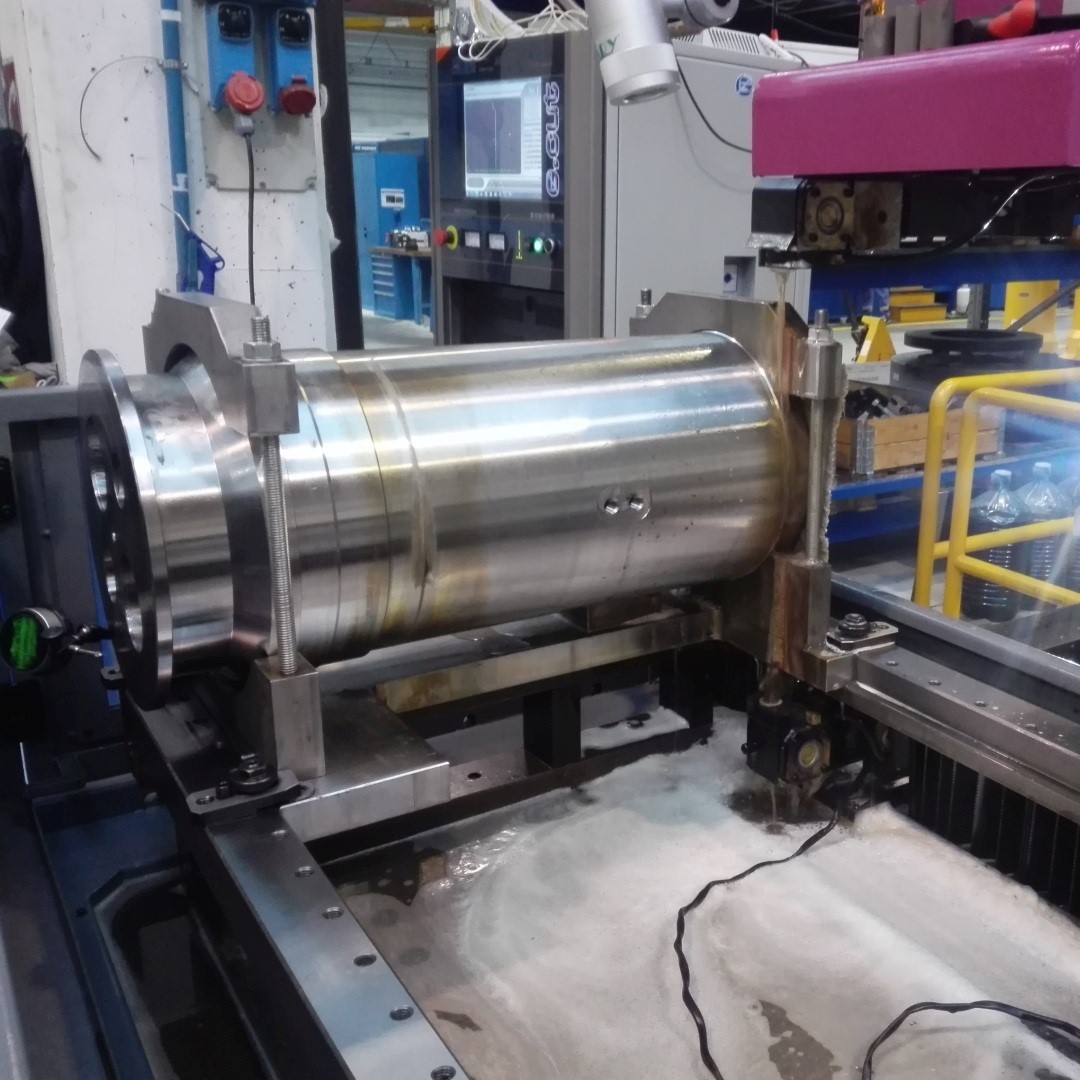
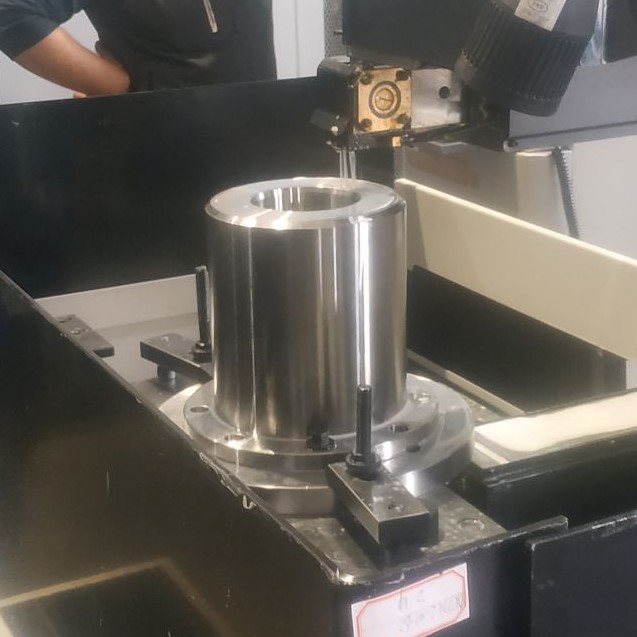

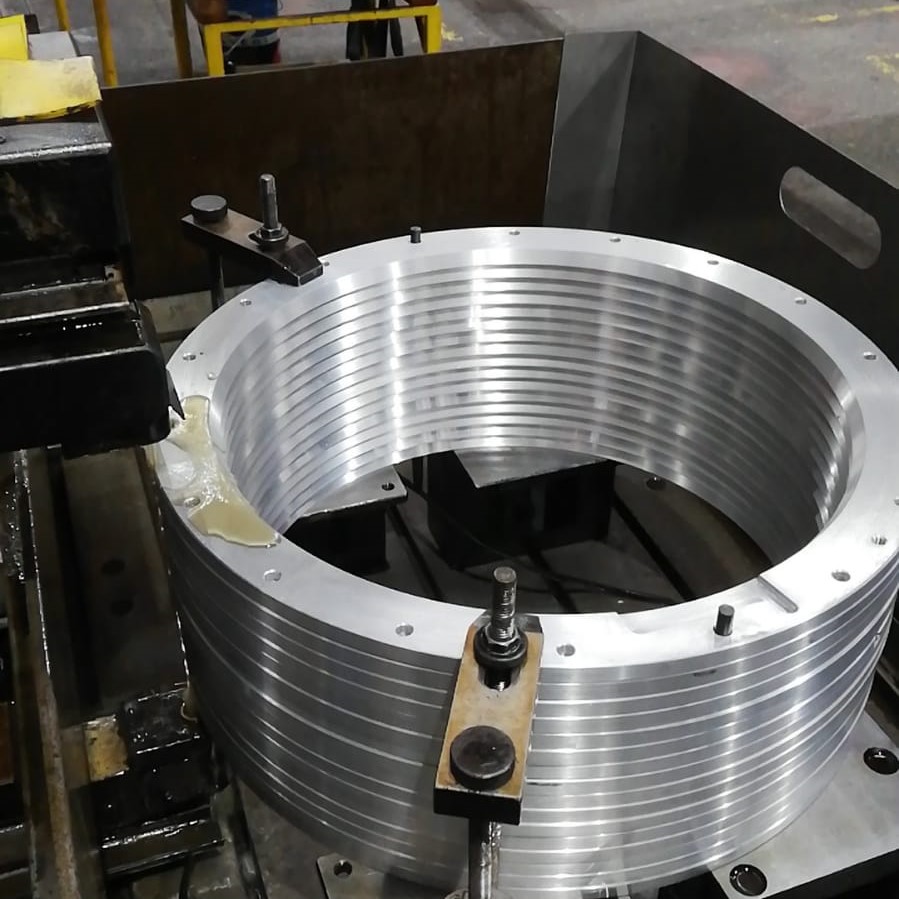
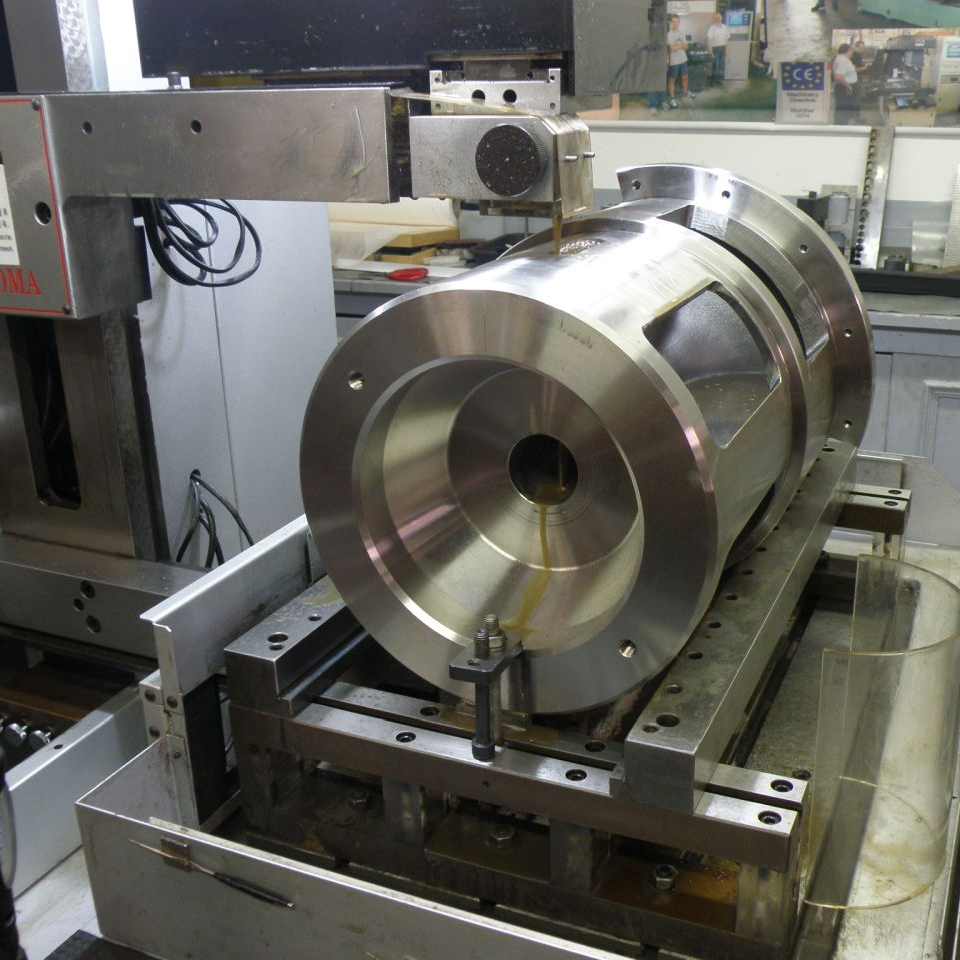
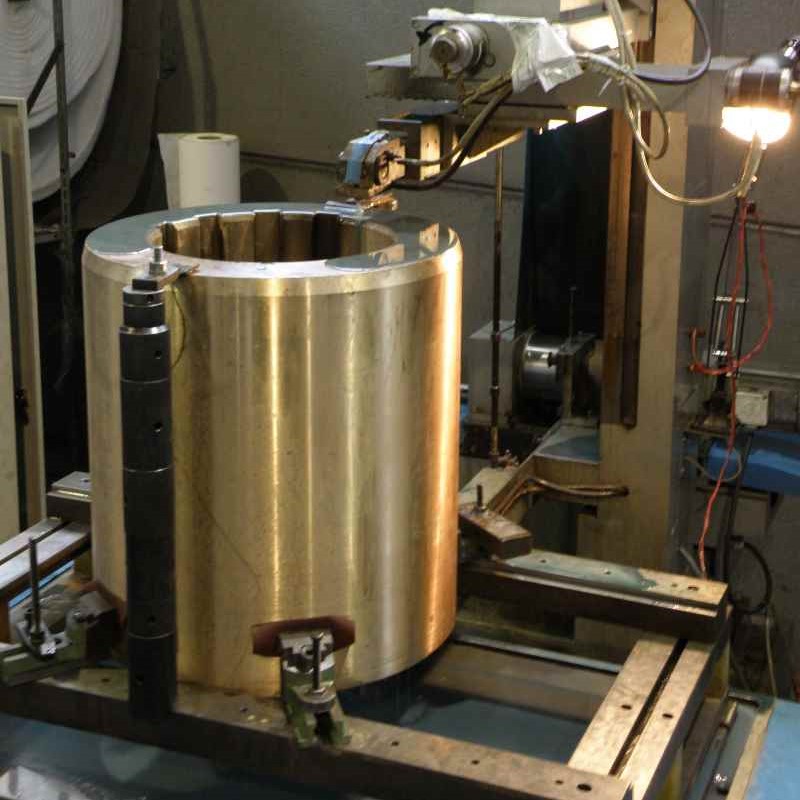
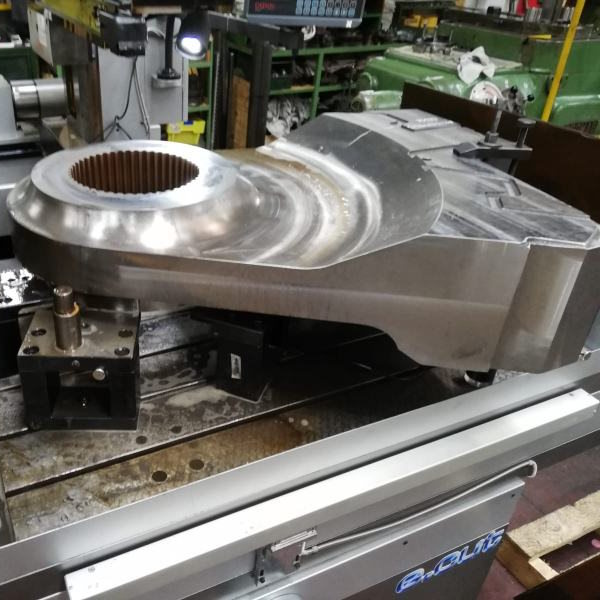

SMALL PIECES.
Ecut ‘ cutting takes place without any thrust. The machining of small parts, even with very complex profiles, is very simple, very advantageous, and often not achievable by other methods. The lack of barrel effect allows ribbing of a few tenths even on high thicknesses.
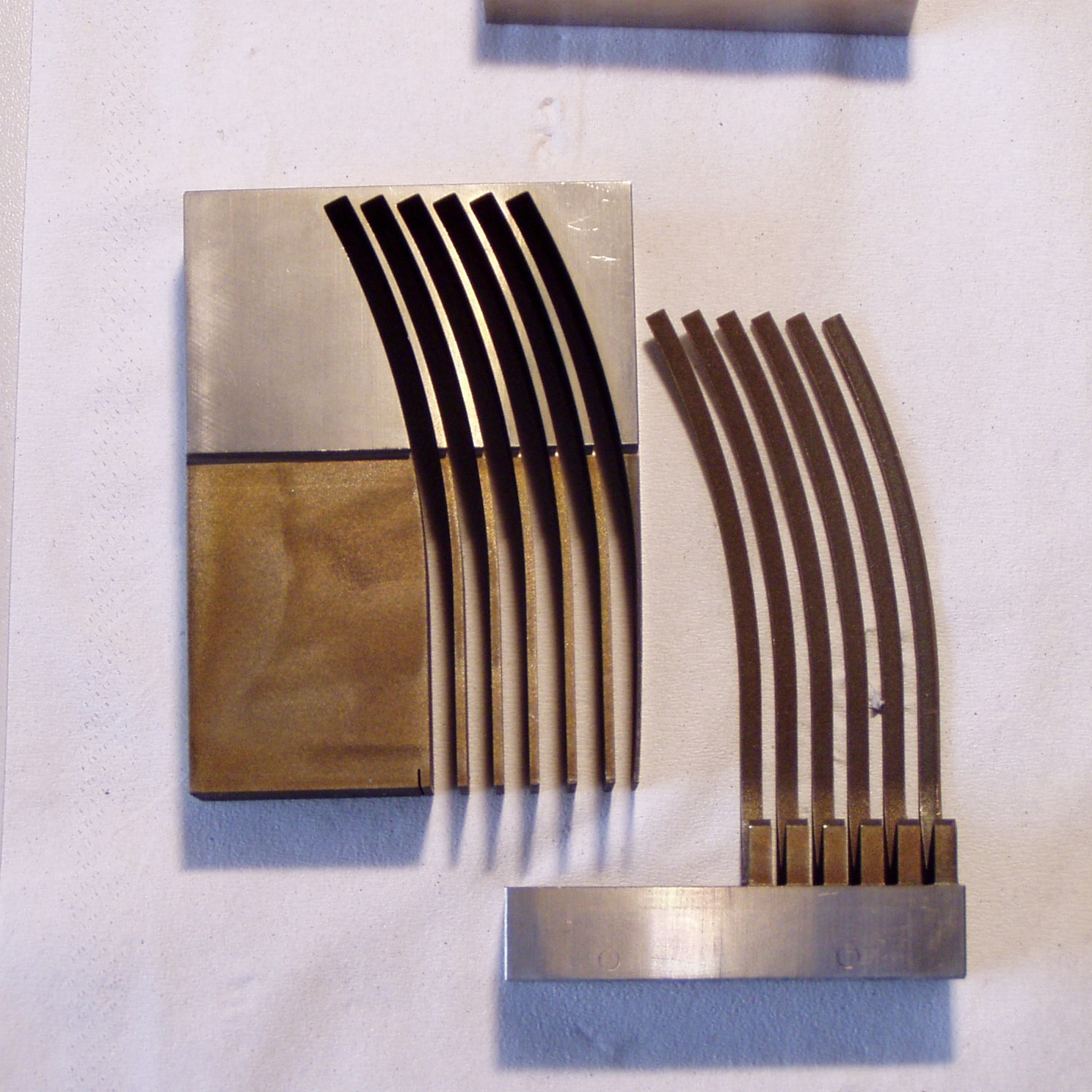
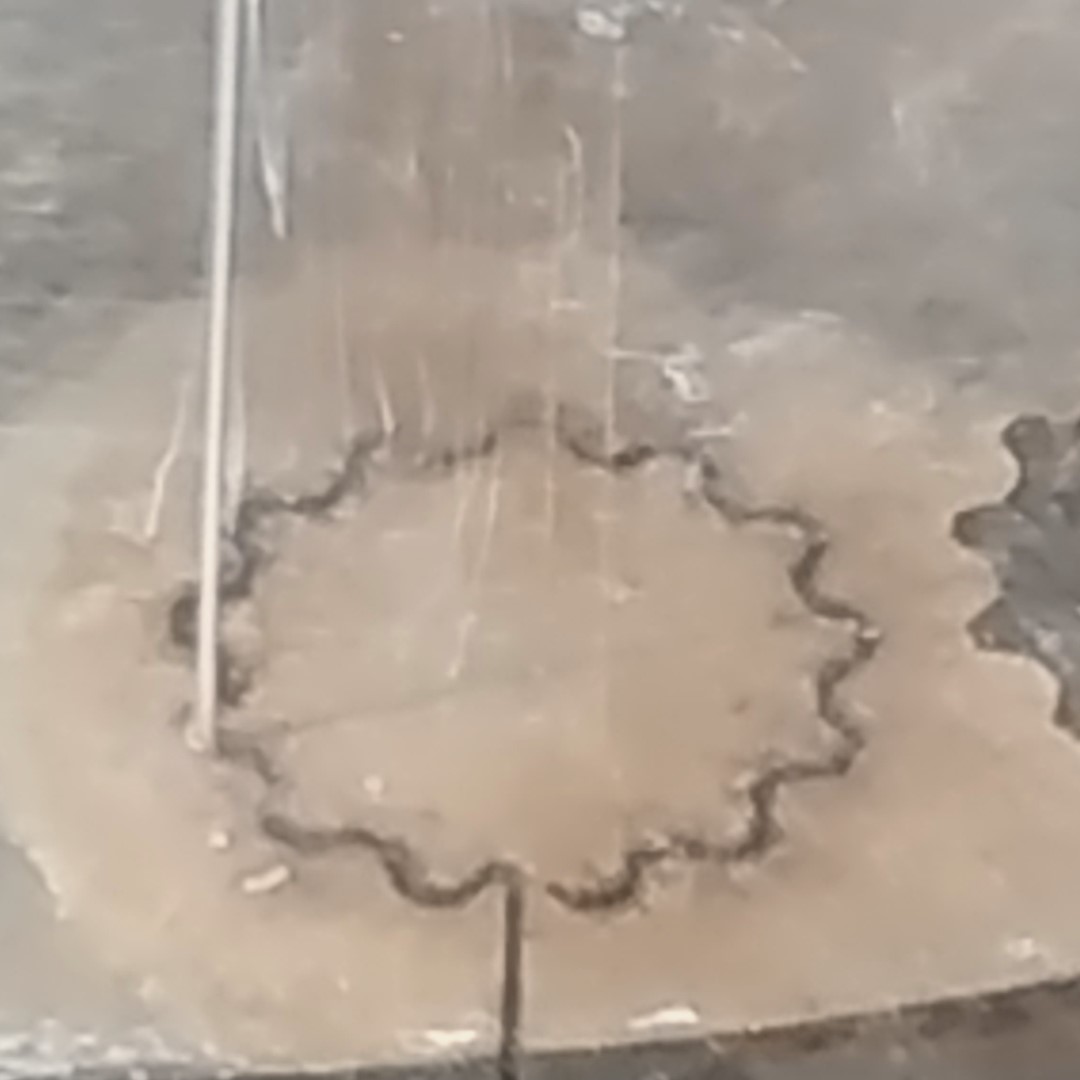

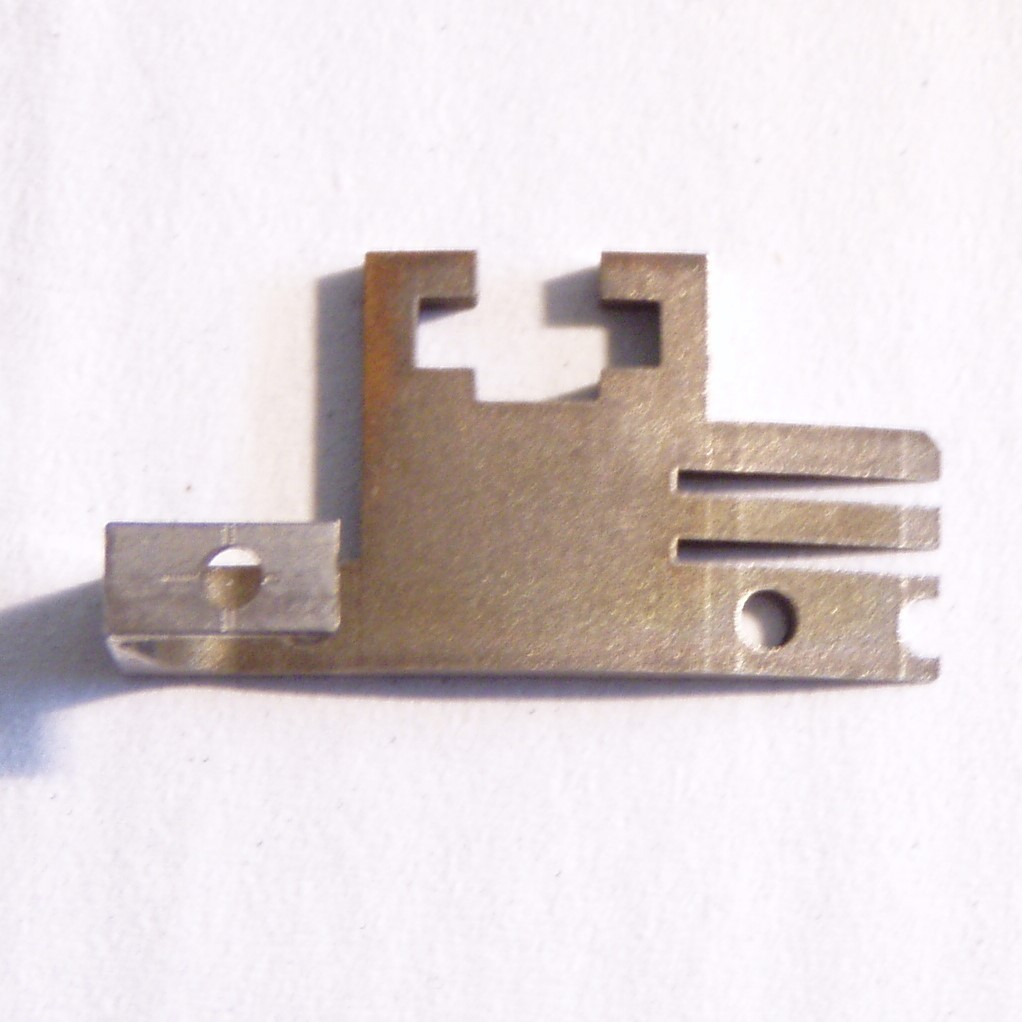
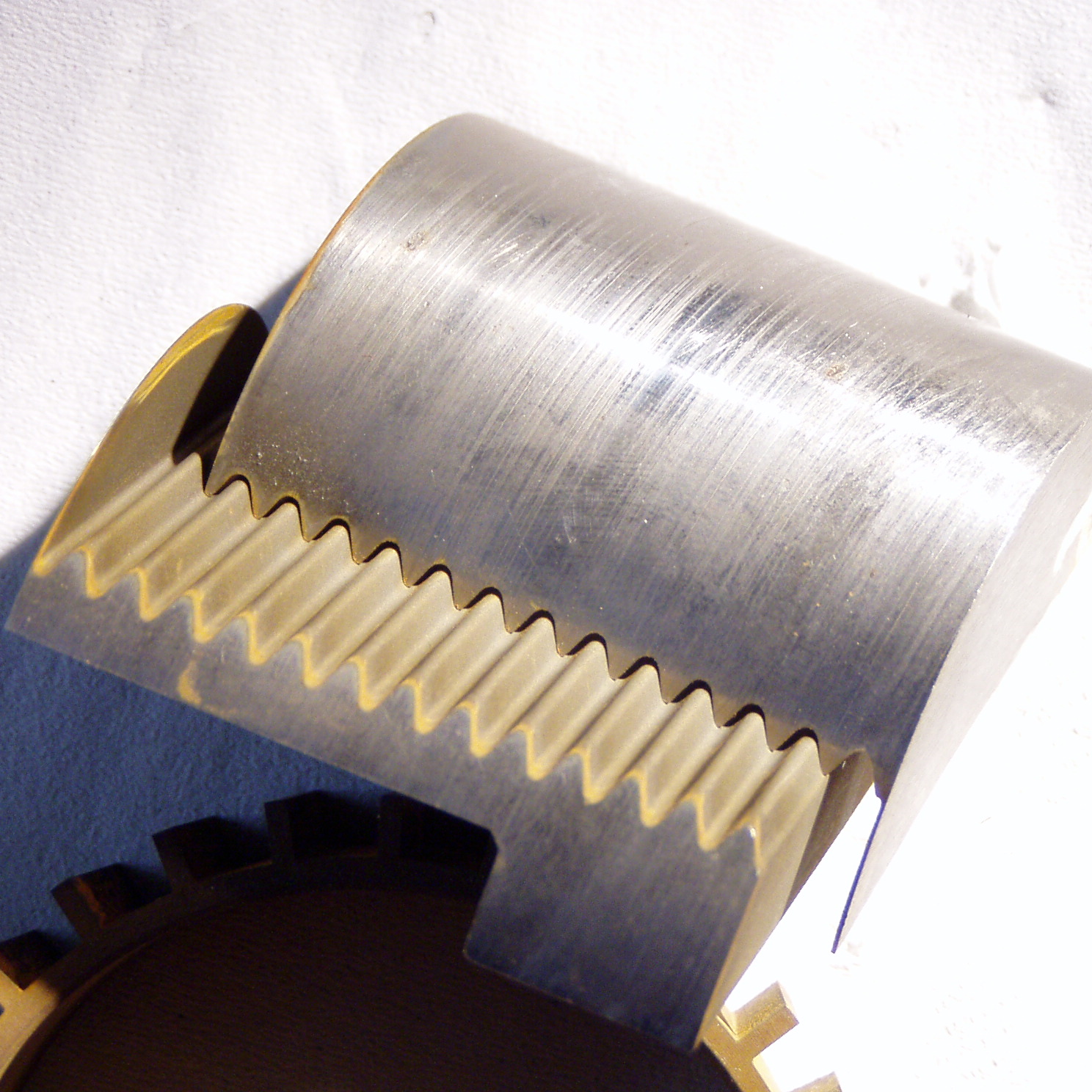
COMPLEX PROFILES
Ecut technology is condensed into one tool, the wire, which produces a 0.2 mm cut. The achievable internal edges are therefore 0.1 mm. The cutting path is obtained from DXF or DWG.
The hourly operating cost is about 0.5 euro/hour in normal machines, and 2 euro/hour in production machines. These are hourly costs that are 25 to 100 times less than machining with chip removal, and 10 to 20 times less than with conventional wire erosion
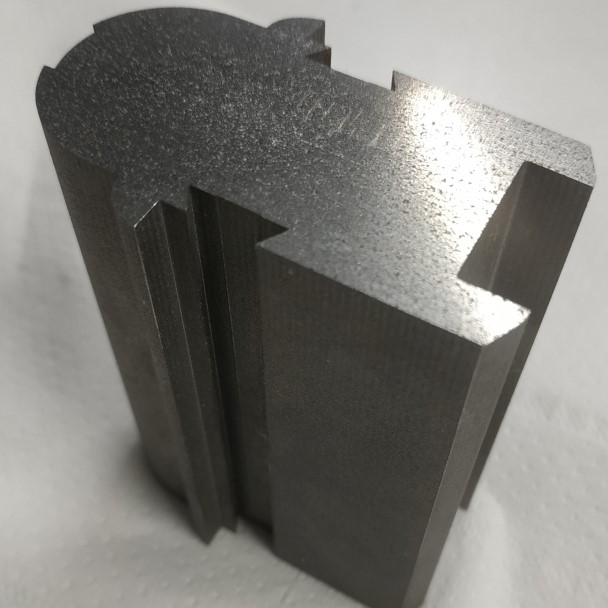
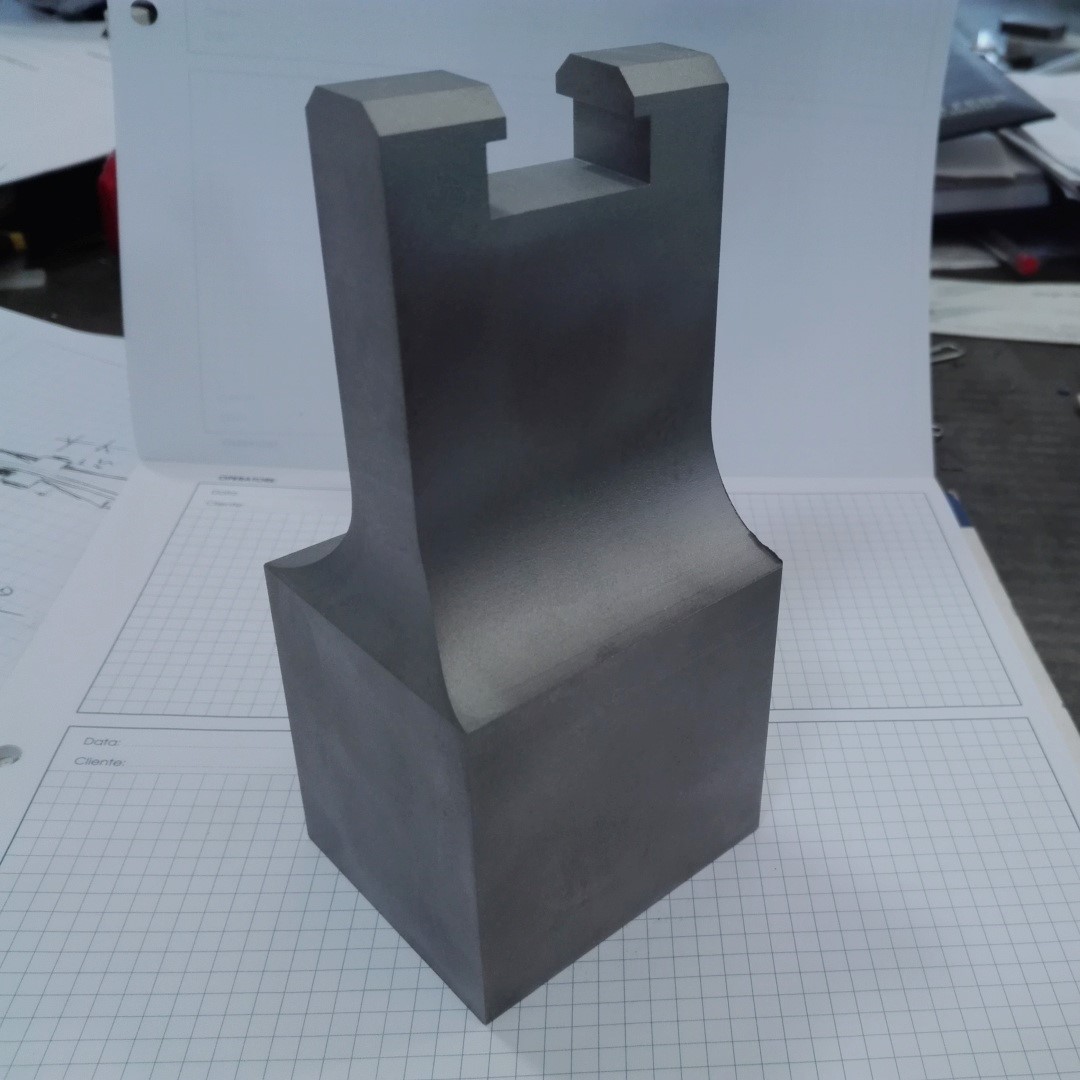
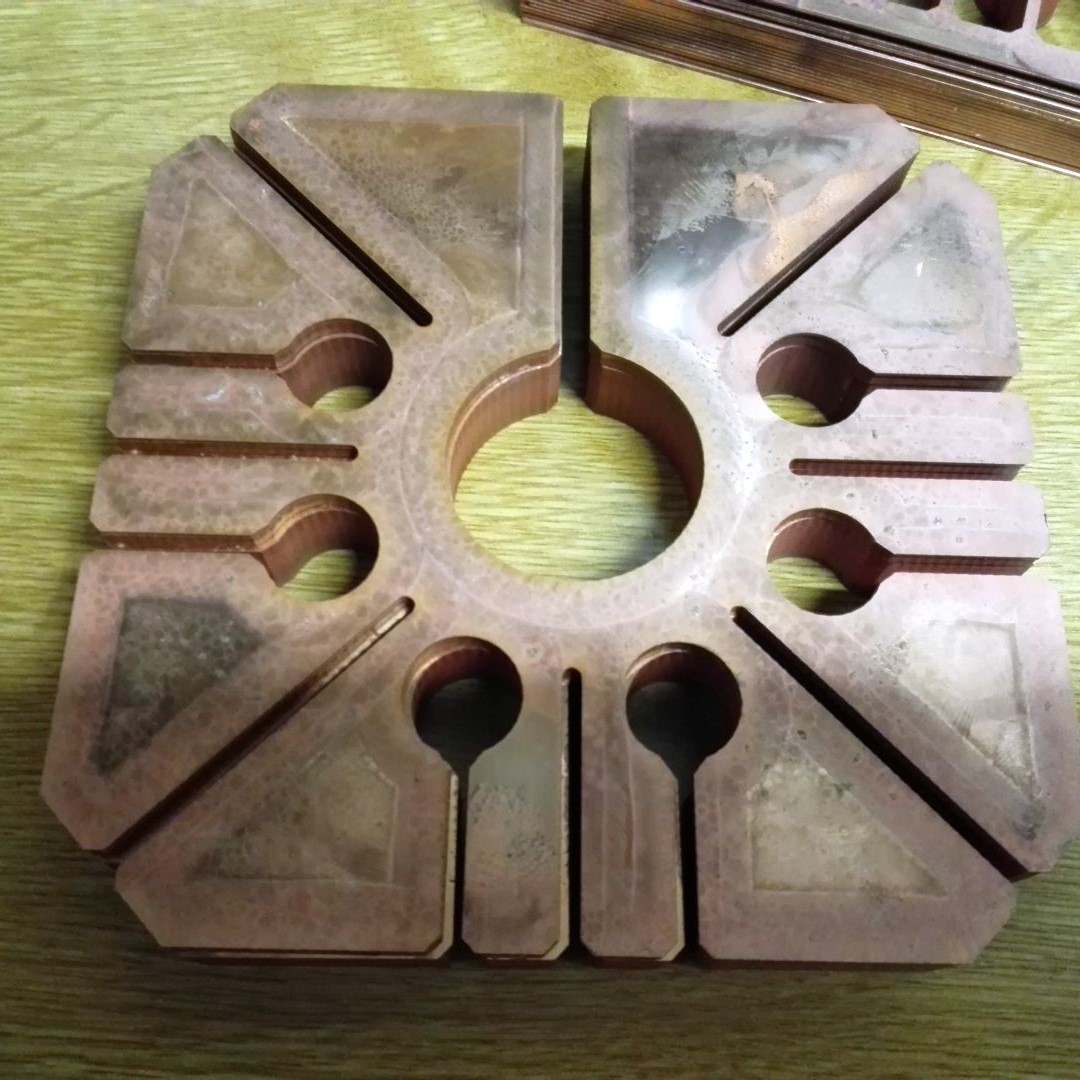
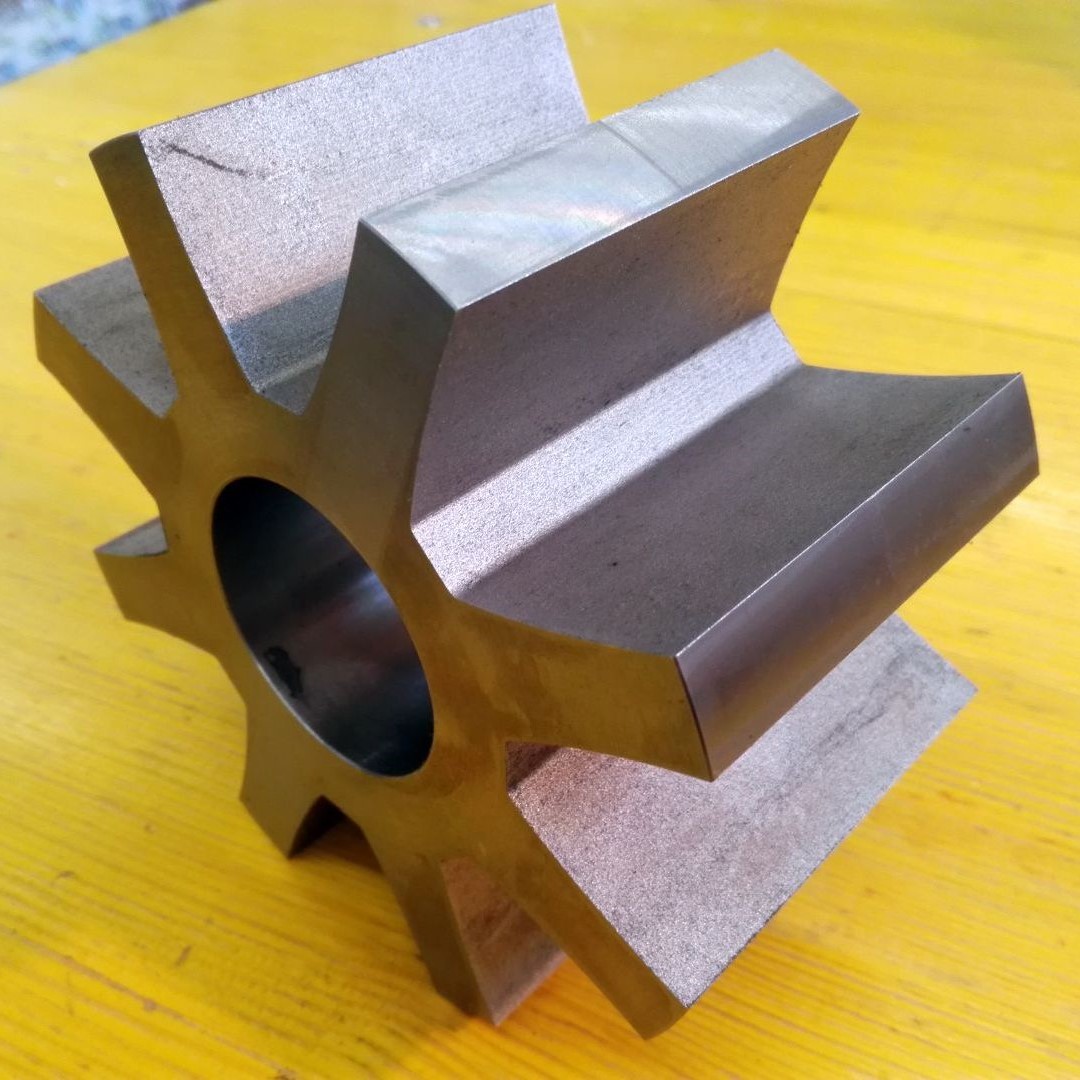
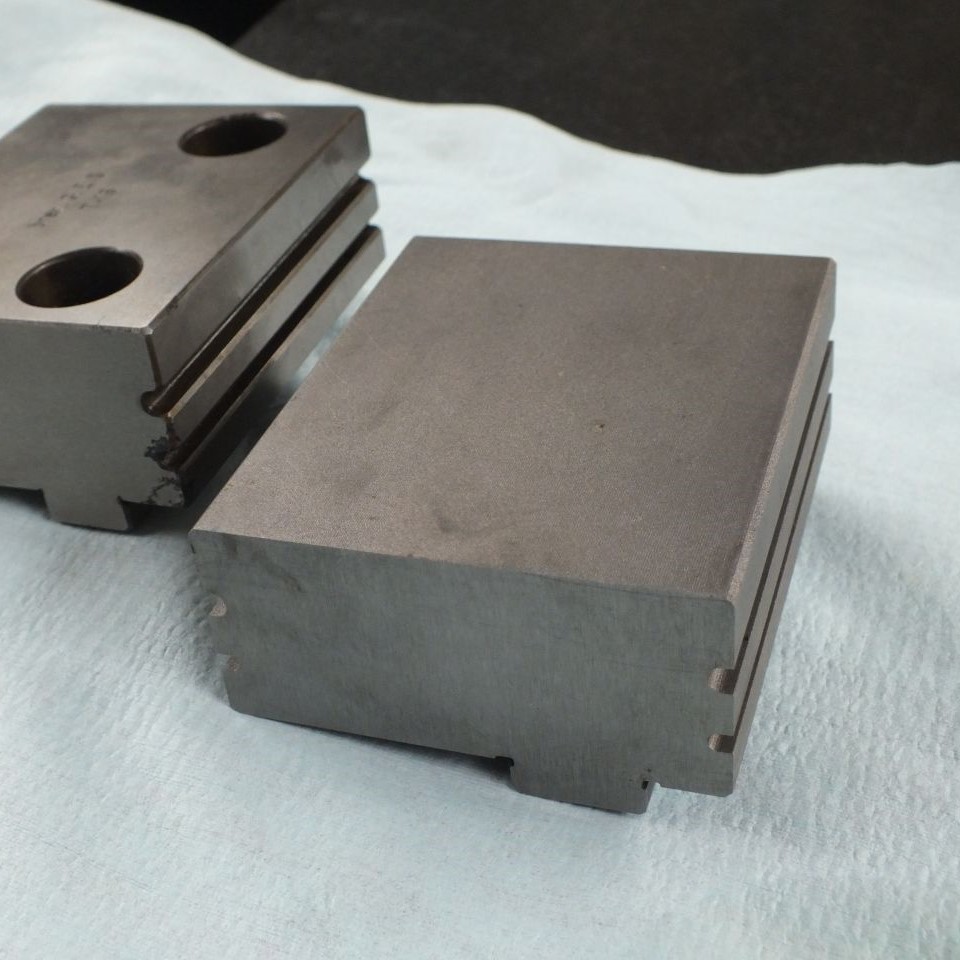
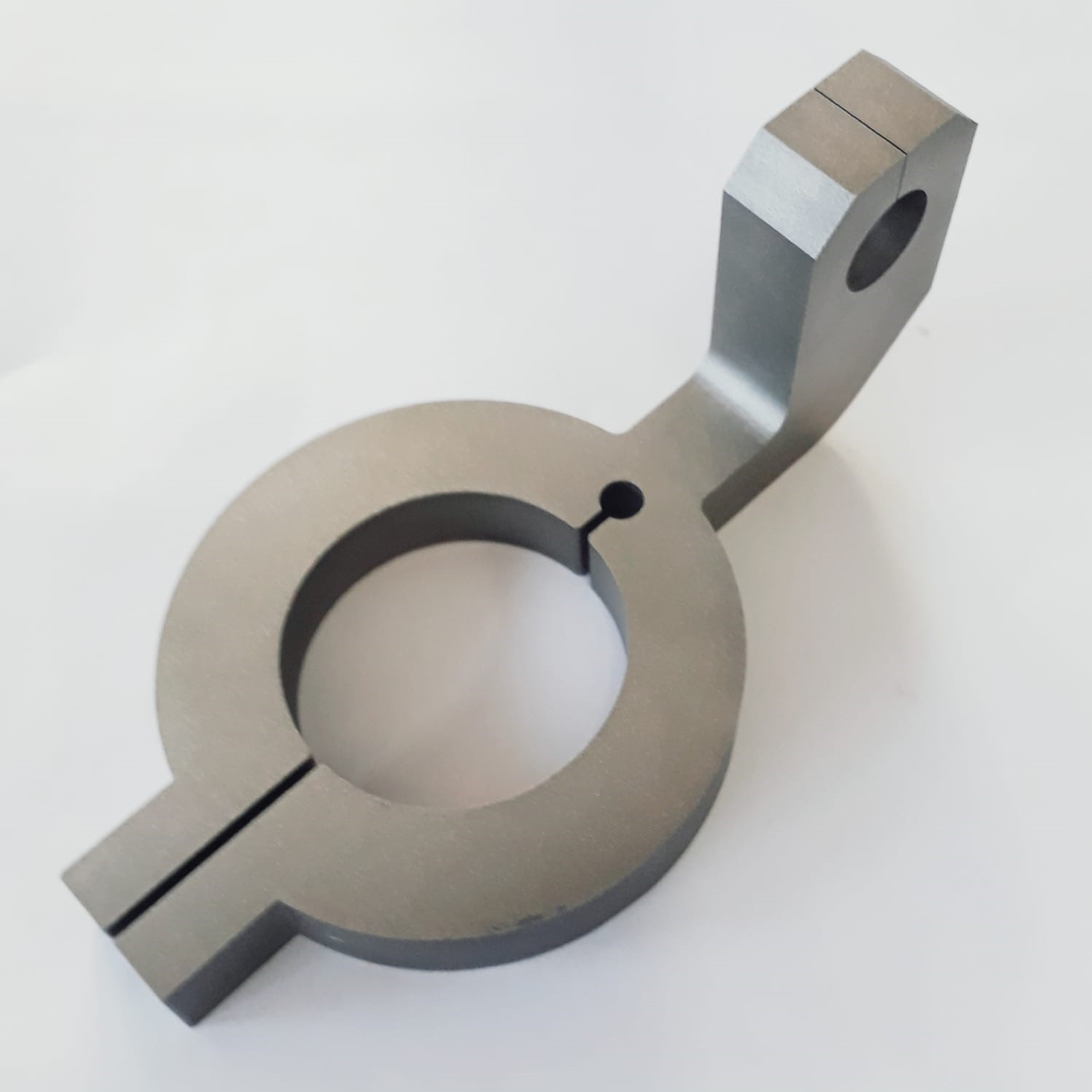
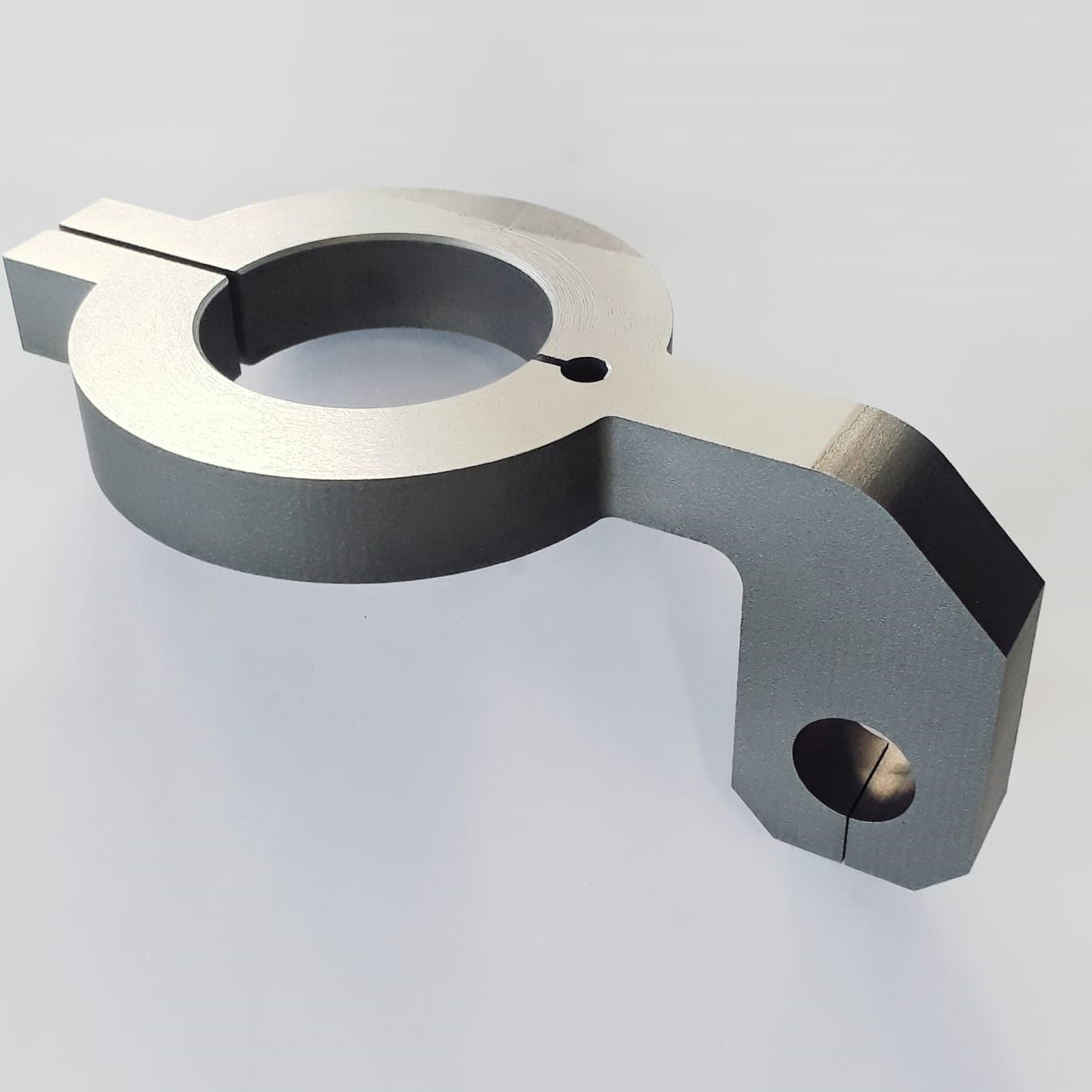
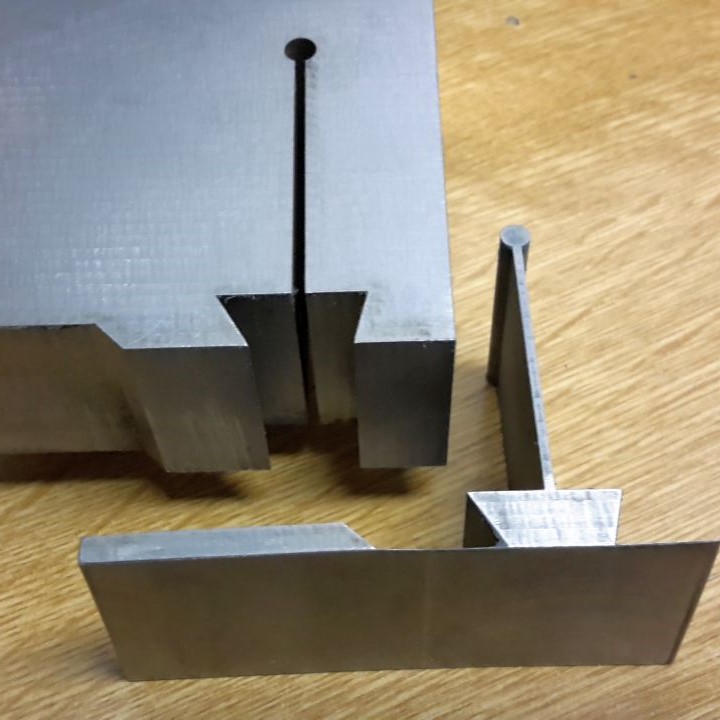
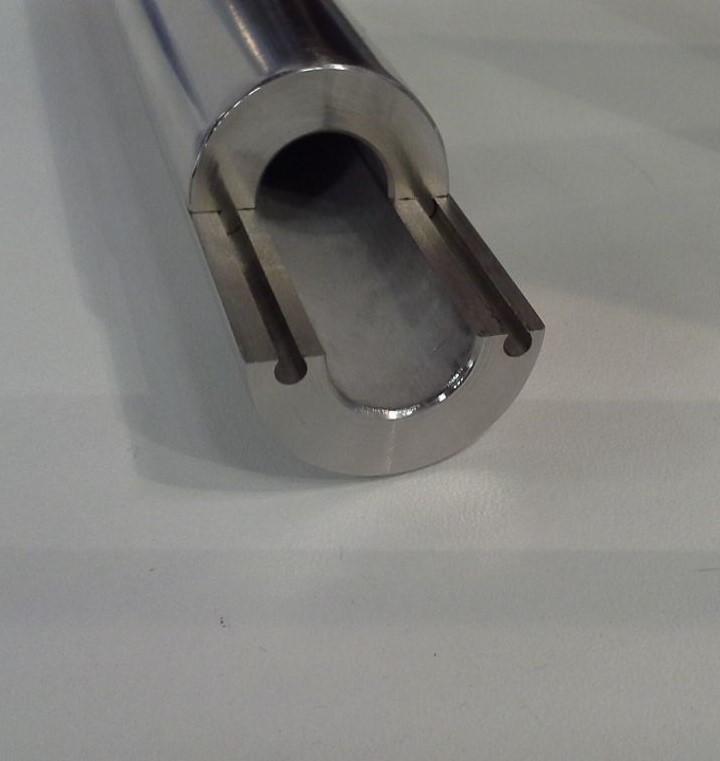
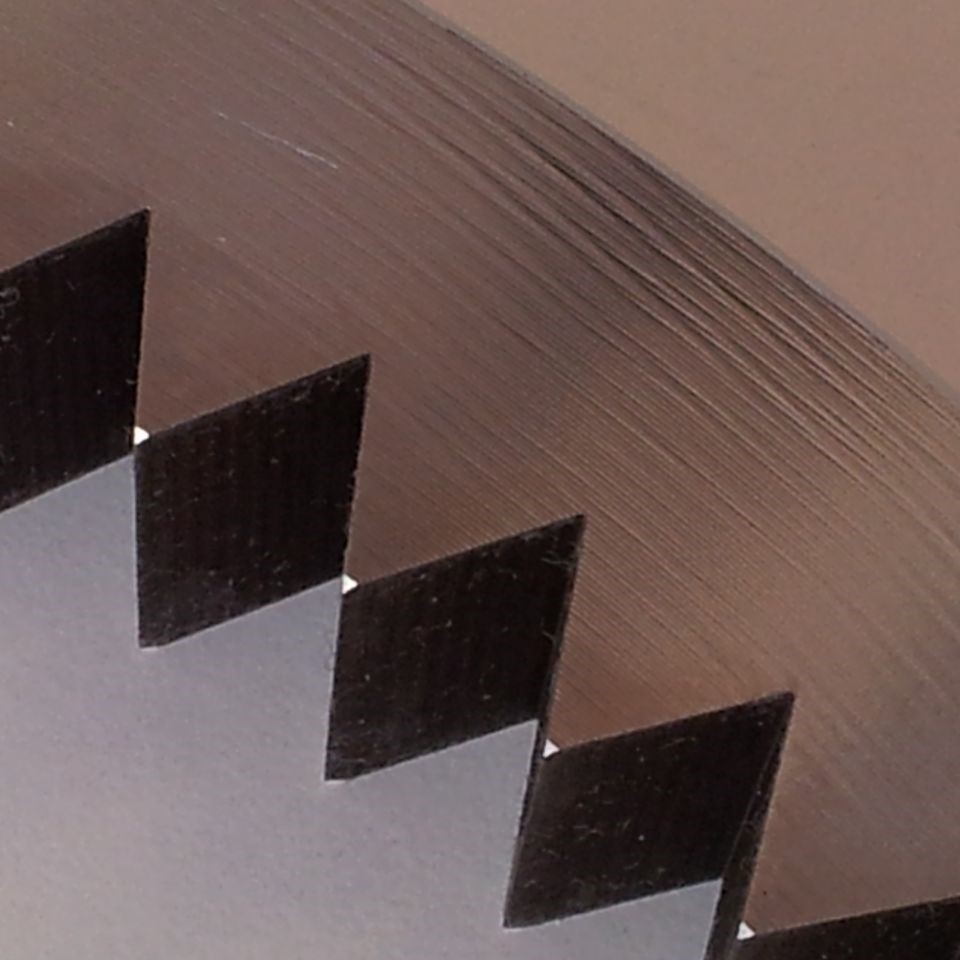
ALUMINUM MACHINING
Machining aluminum with wire erosion machines is virtually impossible. Only Ecut’s patented solution allows its use, doubling the speed of removal.
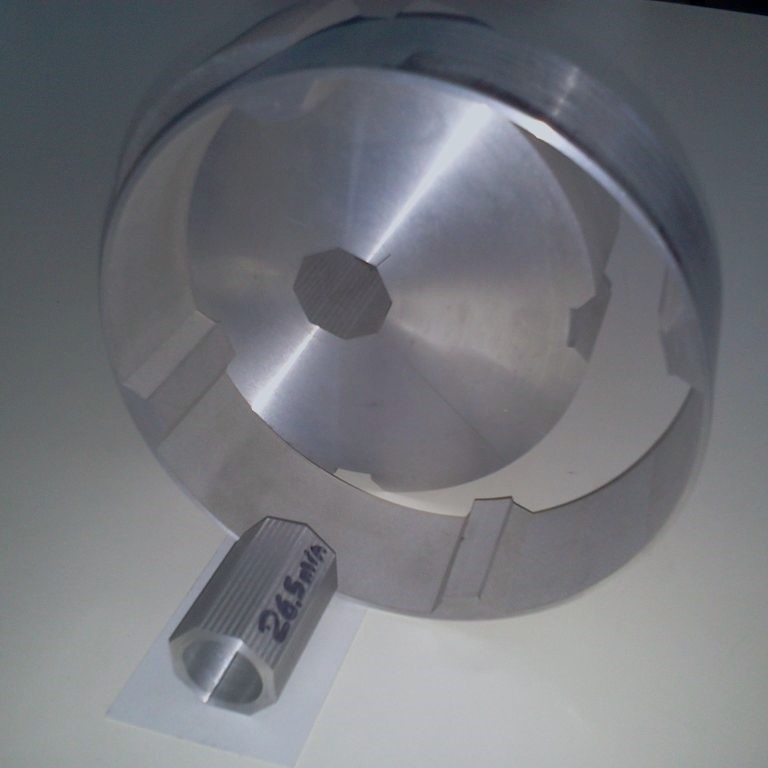
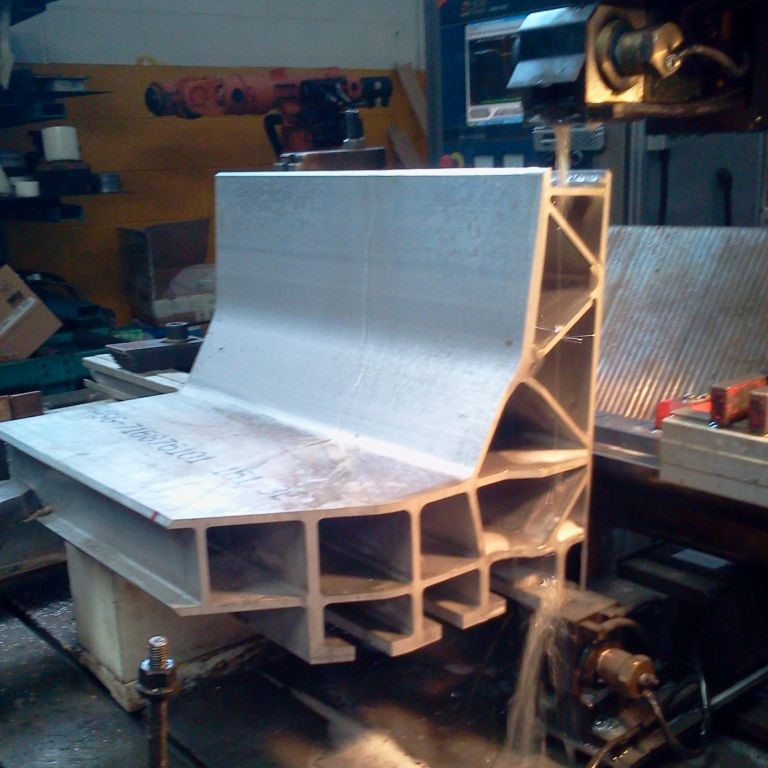
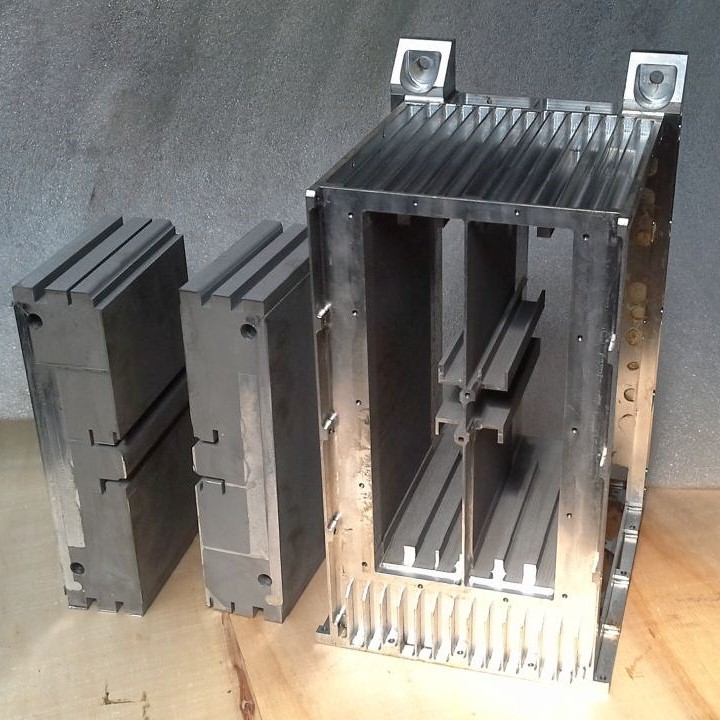
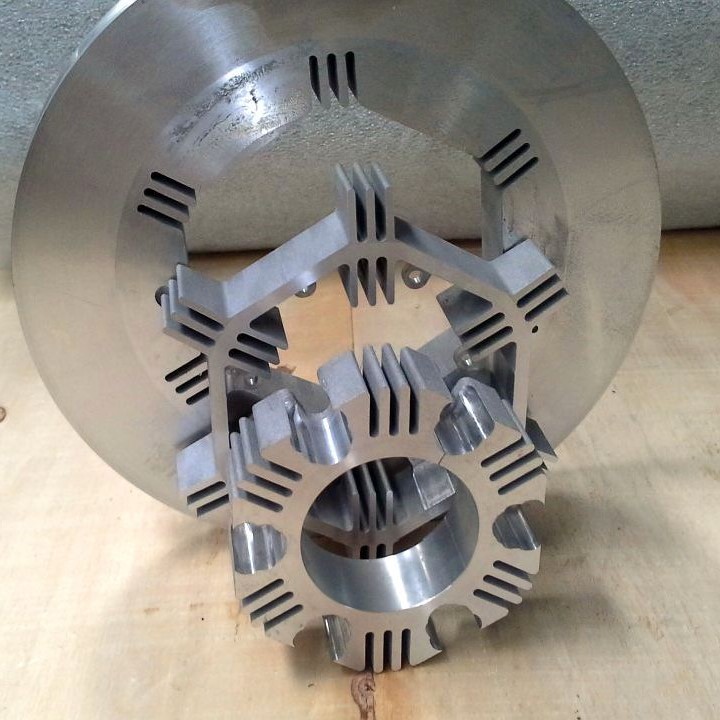
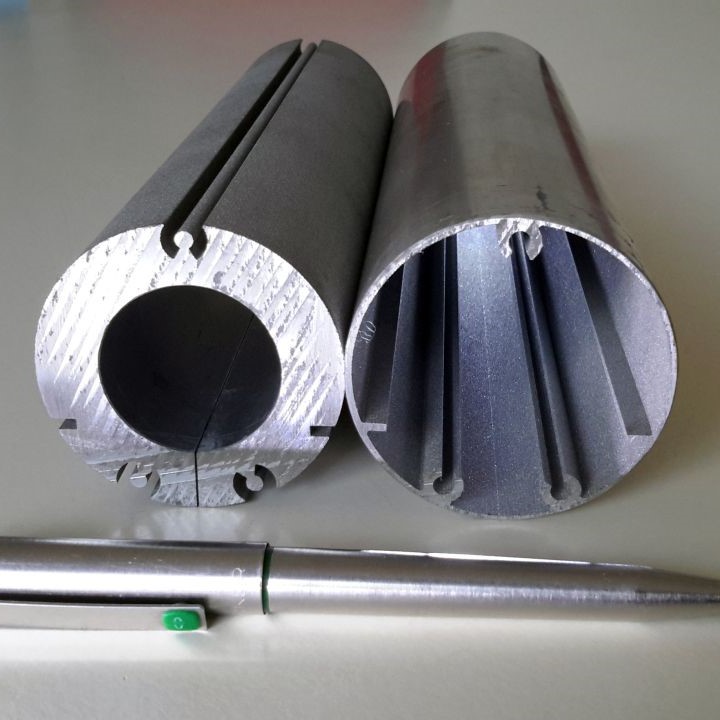
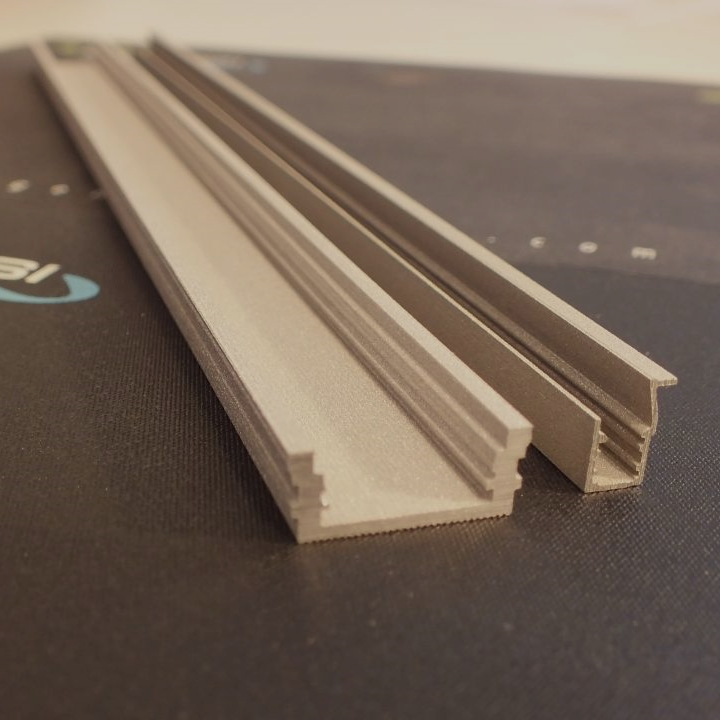
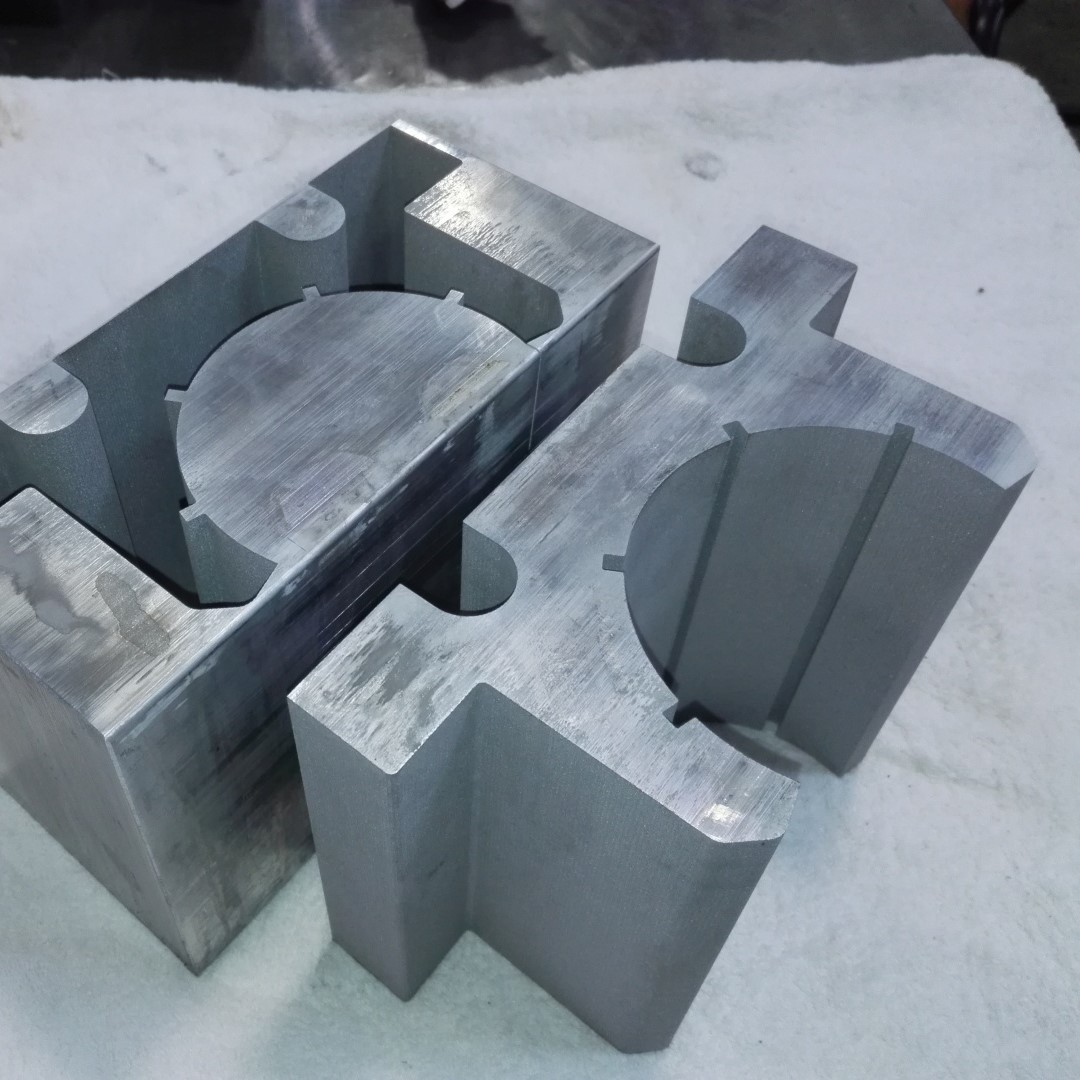
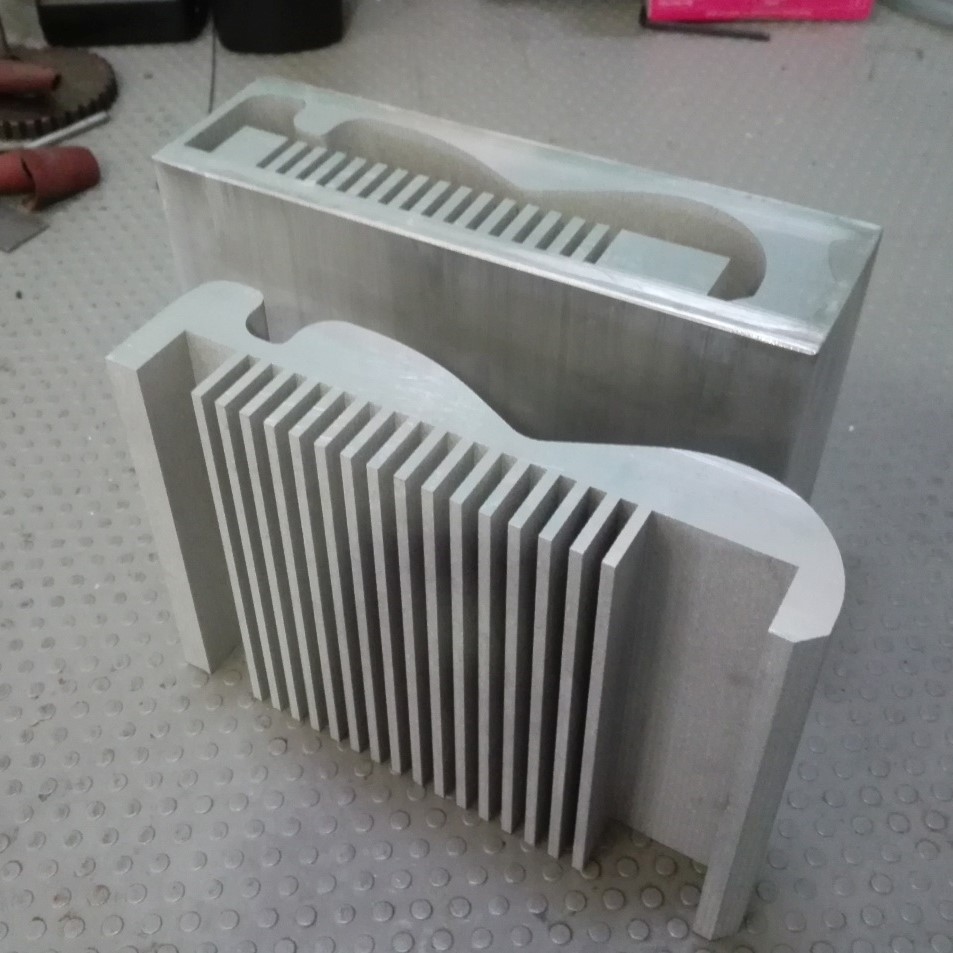
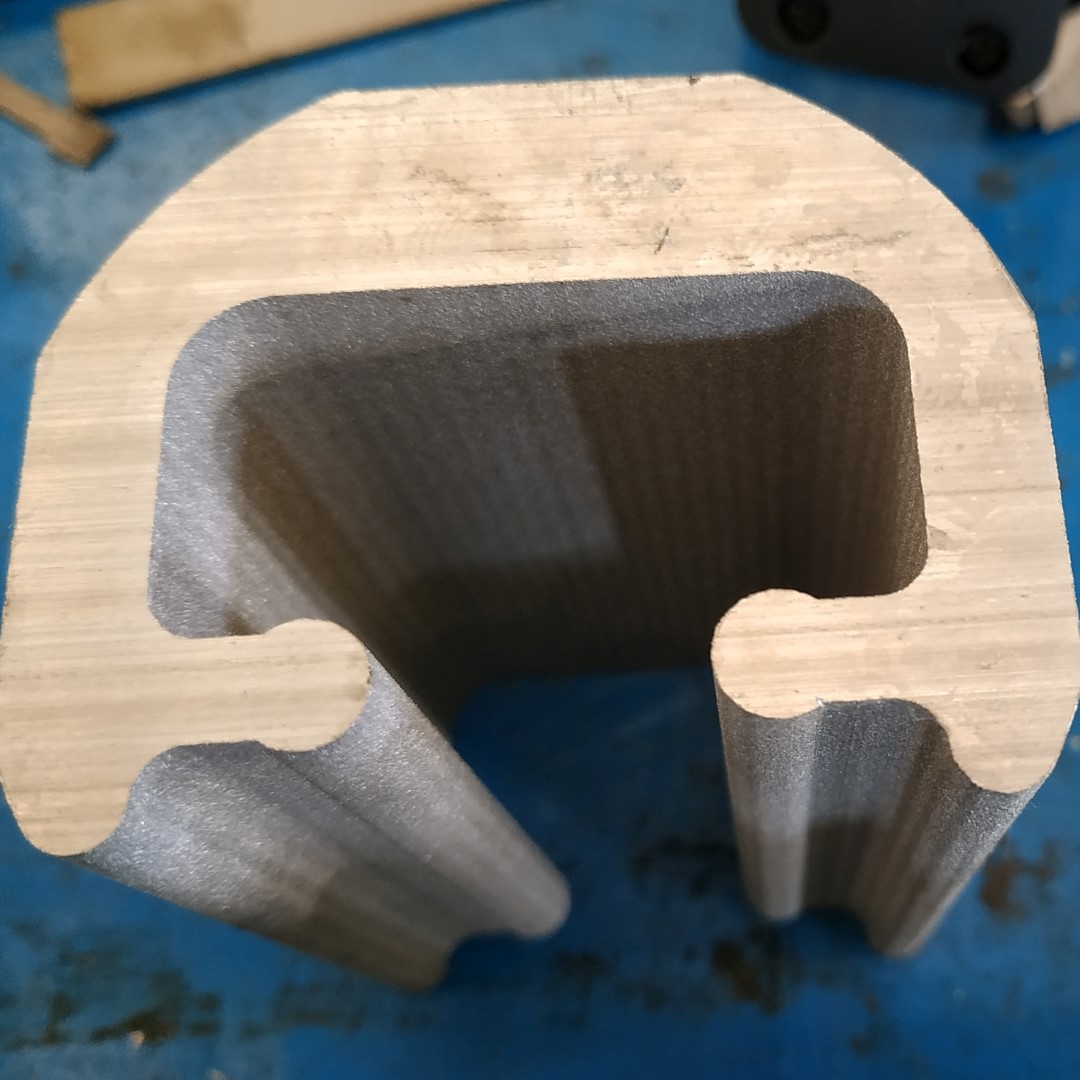
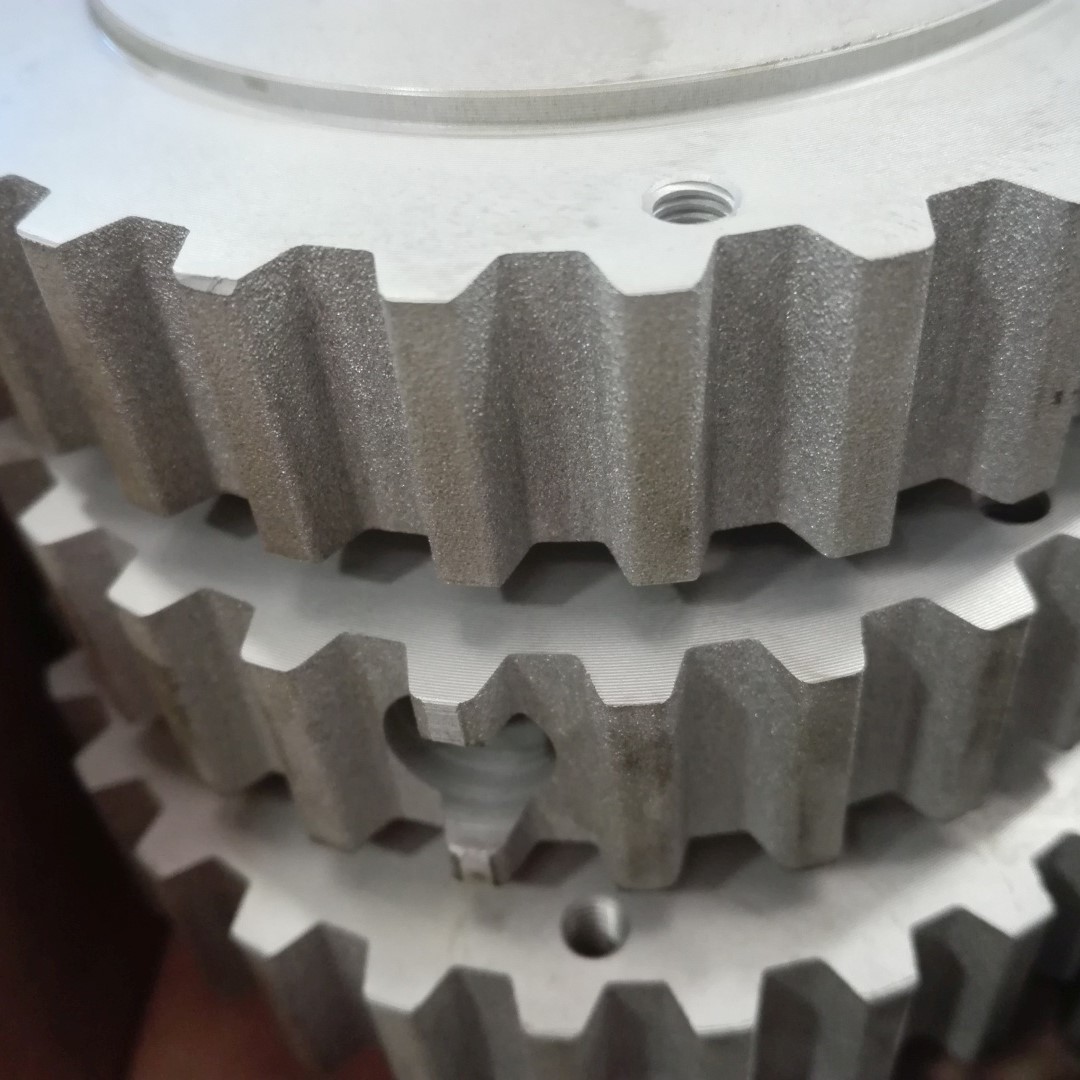
ADDITIVE MANUFACTURING – ADDITIVE METAL PRINTING
Ecut is used by all manufacturers of metal parts through Additive Manufacturing. Ecut’s range covers all sizes of plates used. Any material is cut with minimum cut thickness, much faster and cheaper than other methods, including conventional wire erosion.
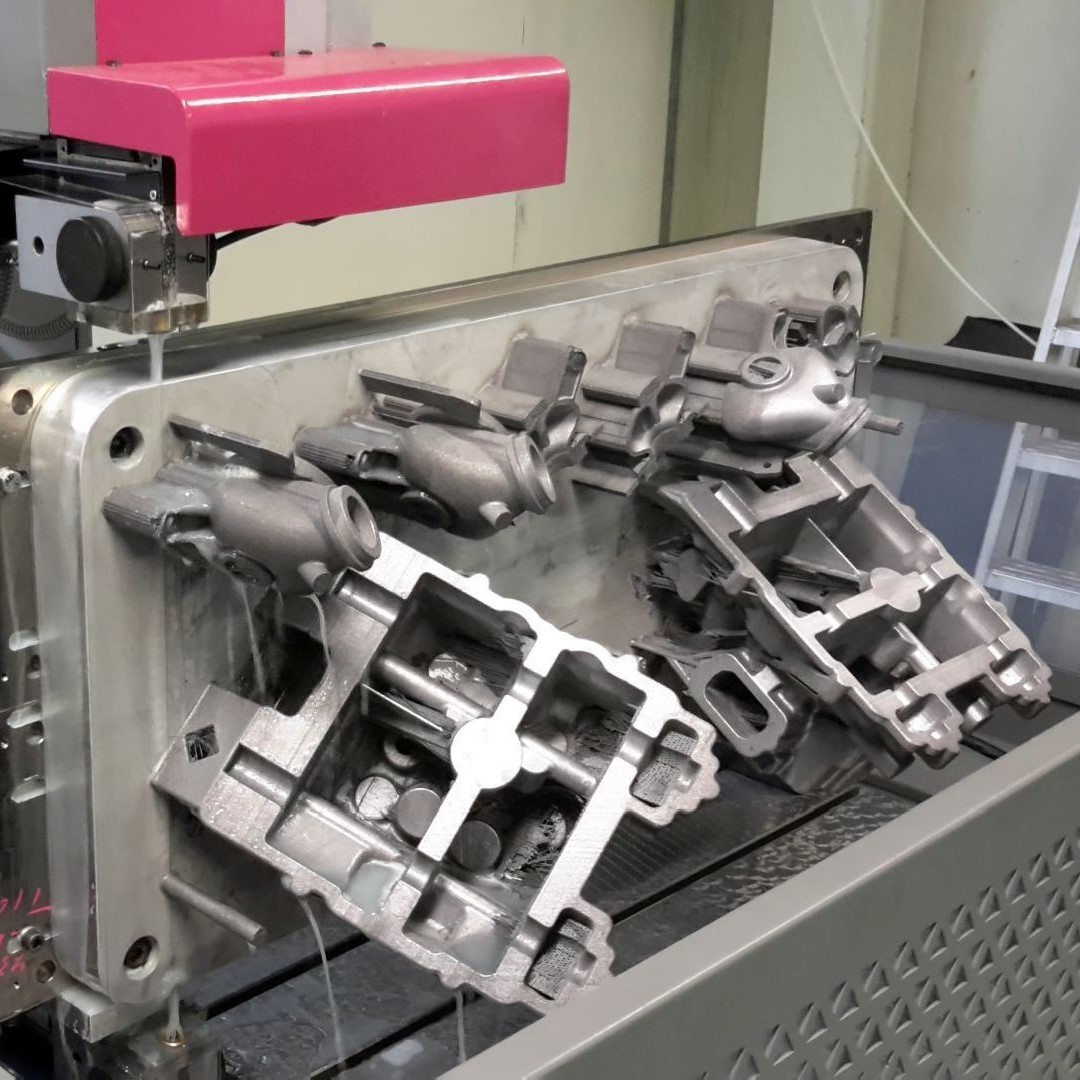
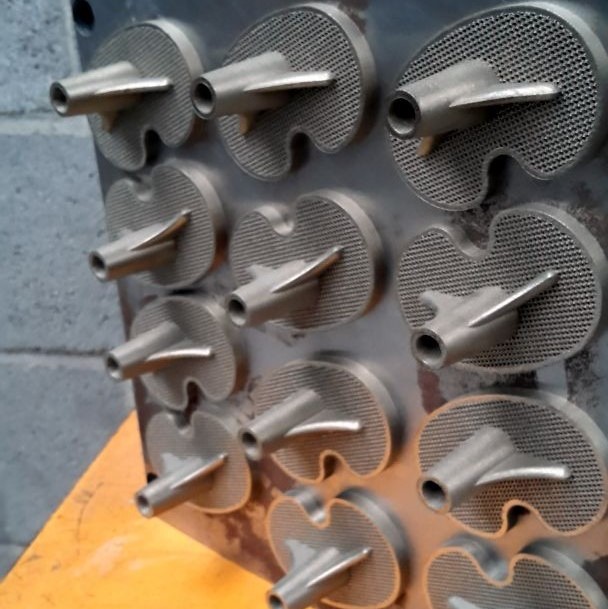
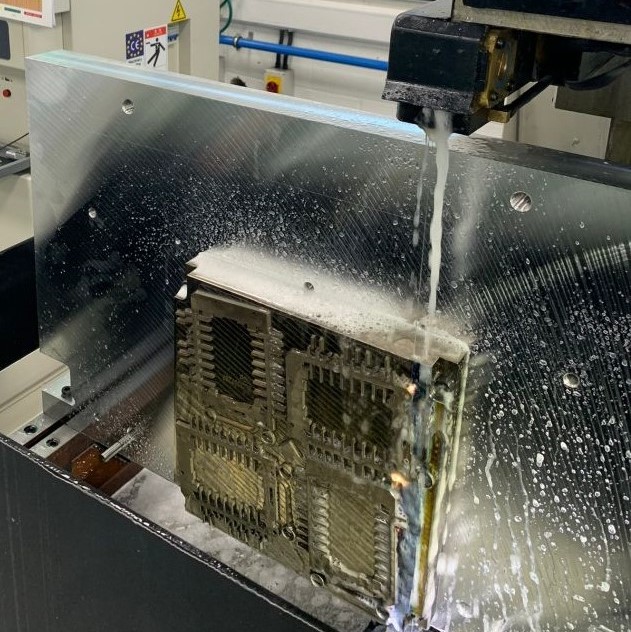
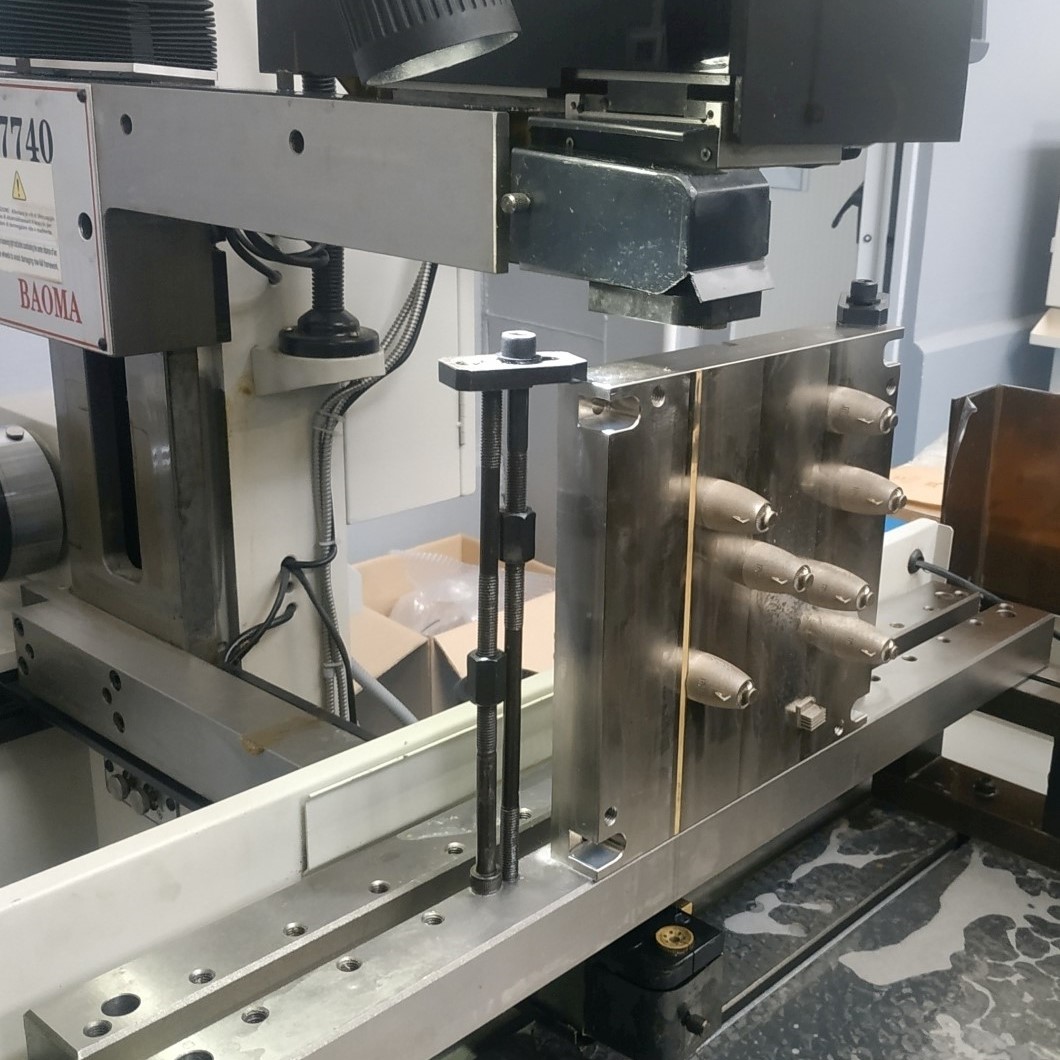
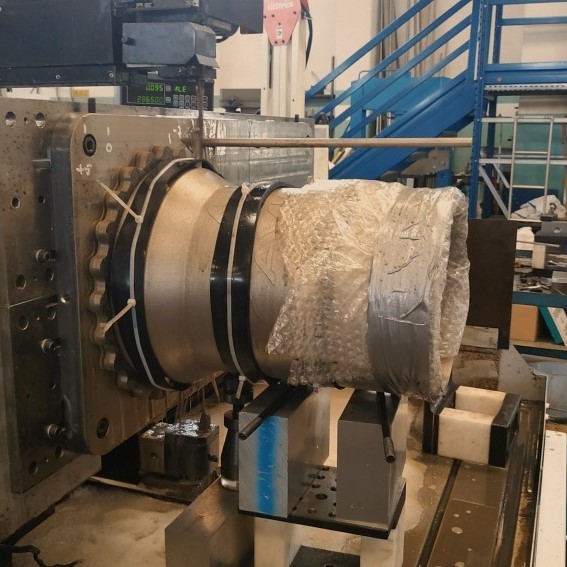
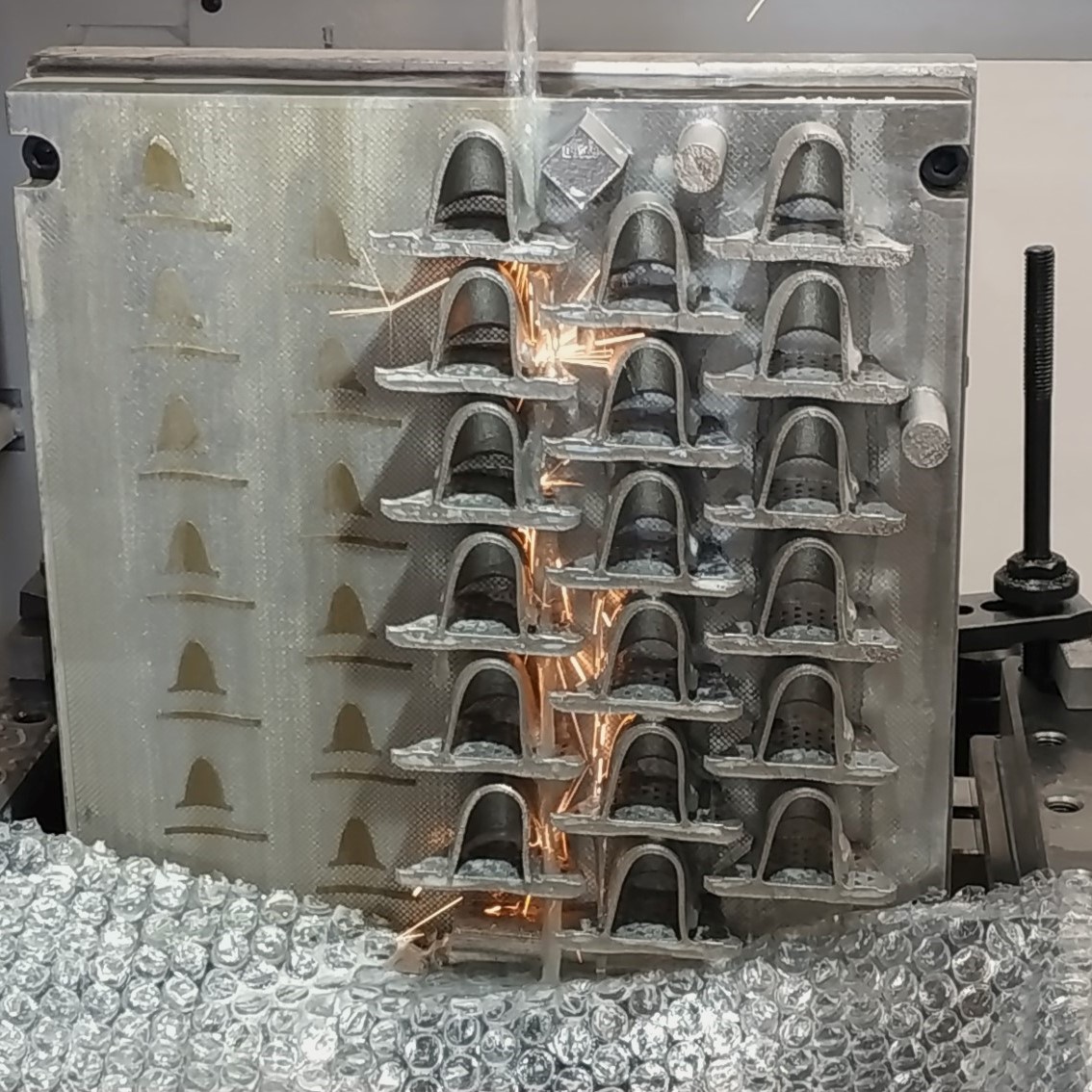
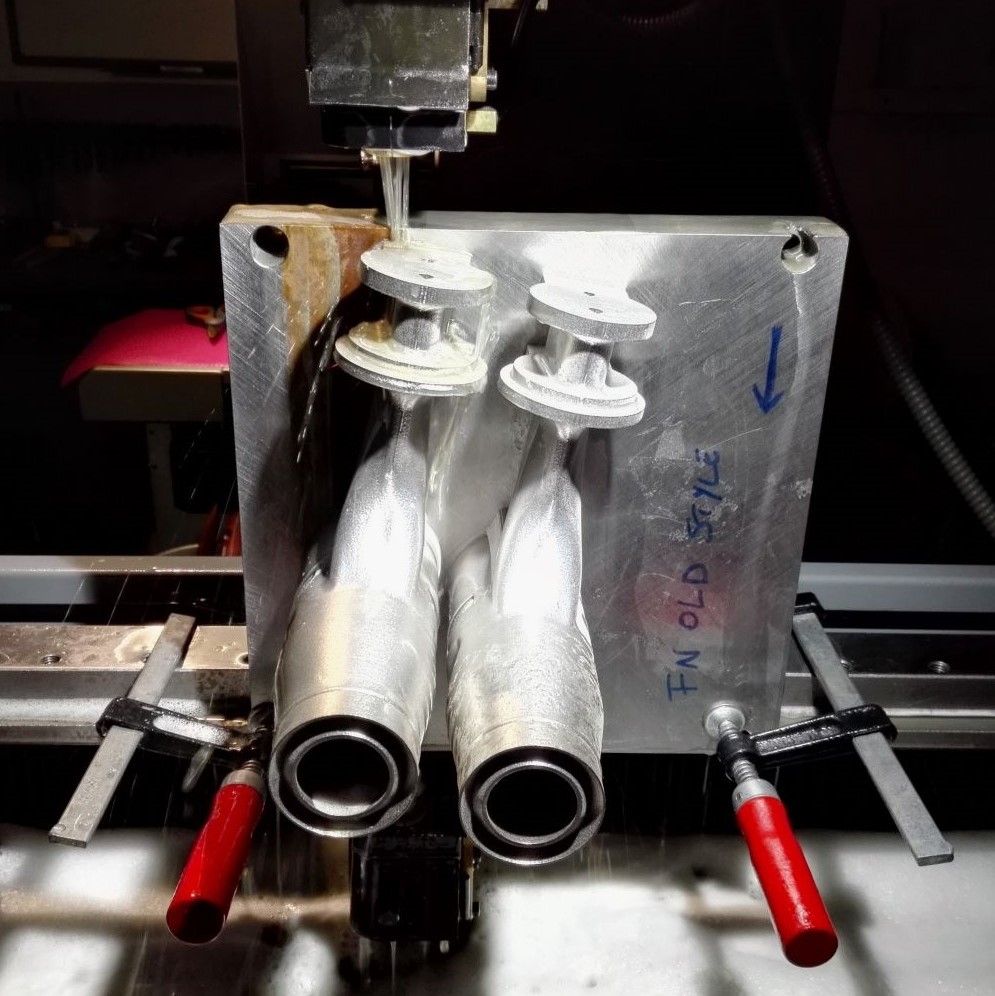
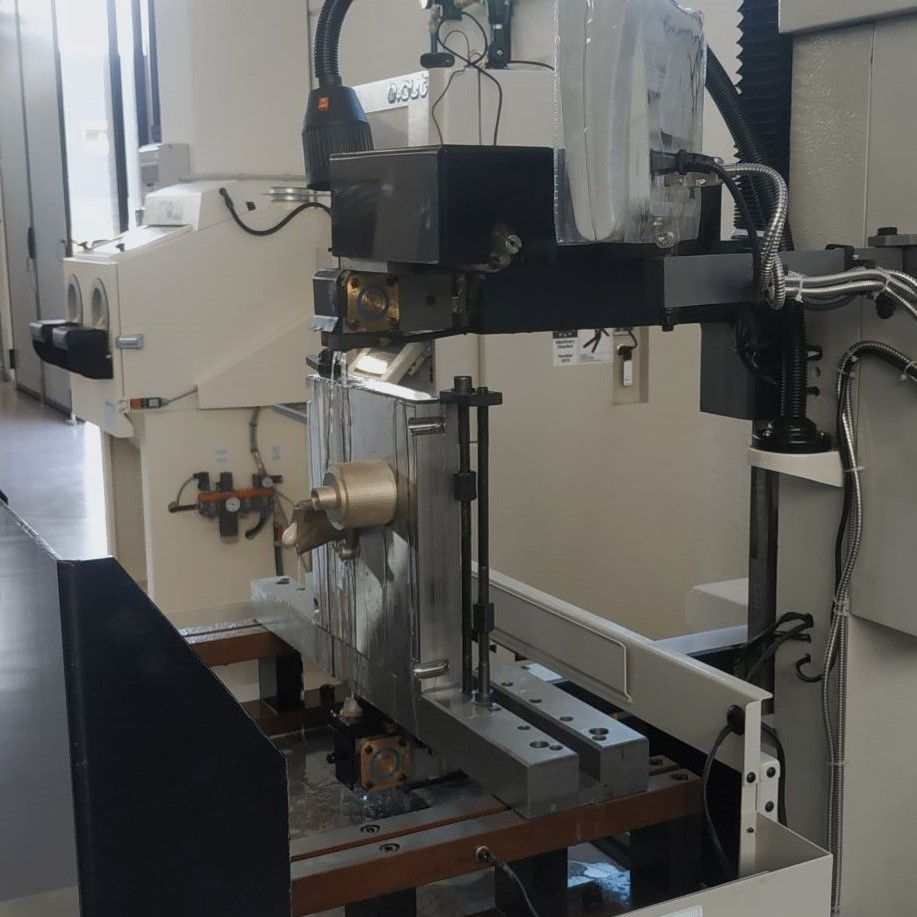
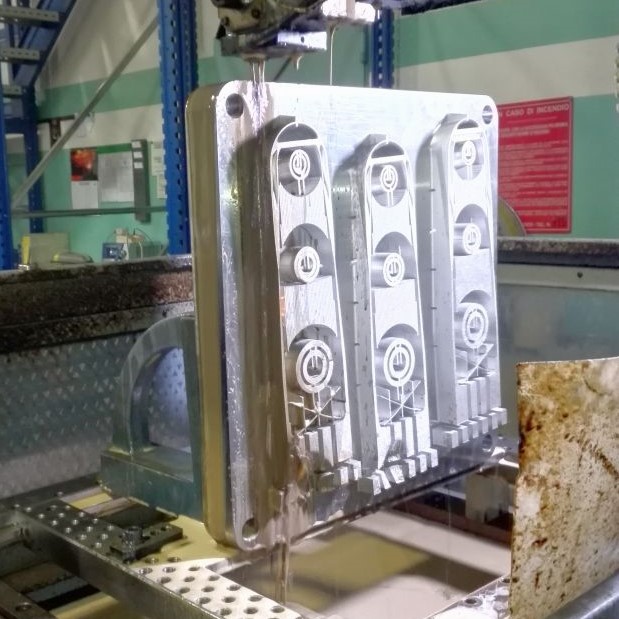
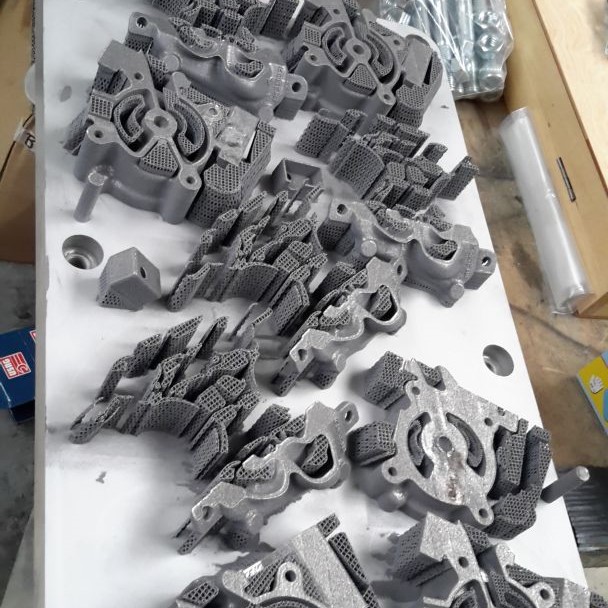
GEARS, KEYWAYS AND BROACHING
The execution of keyways on large workpieces is enormously advantageous with Ecut. The ‘absence of “barrel effect” allows perfect geometries on thicknesses up to, and over, 500mm .
The great precision, +/- 0.0075 mm, allows Ecut to outperform normal shapers in large keyways.
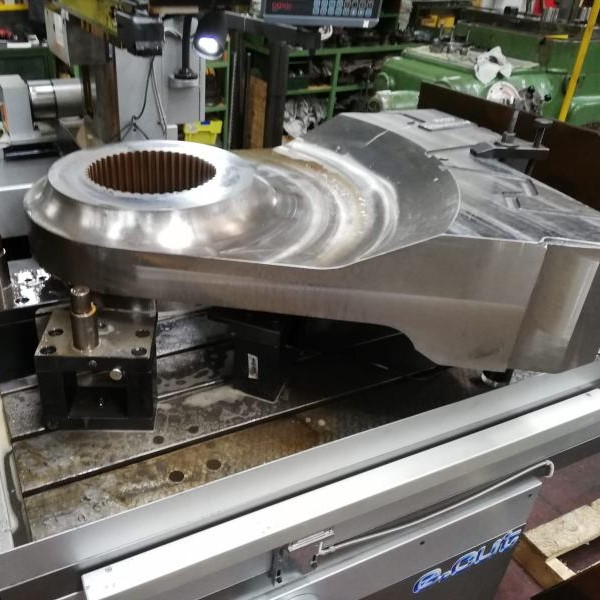
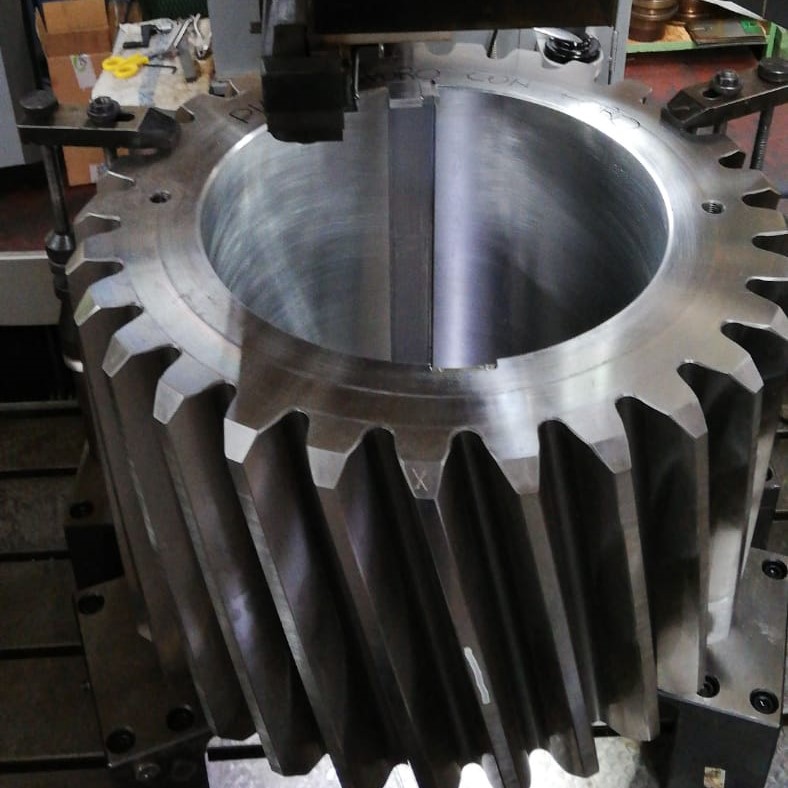
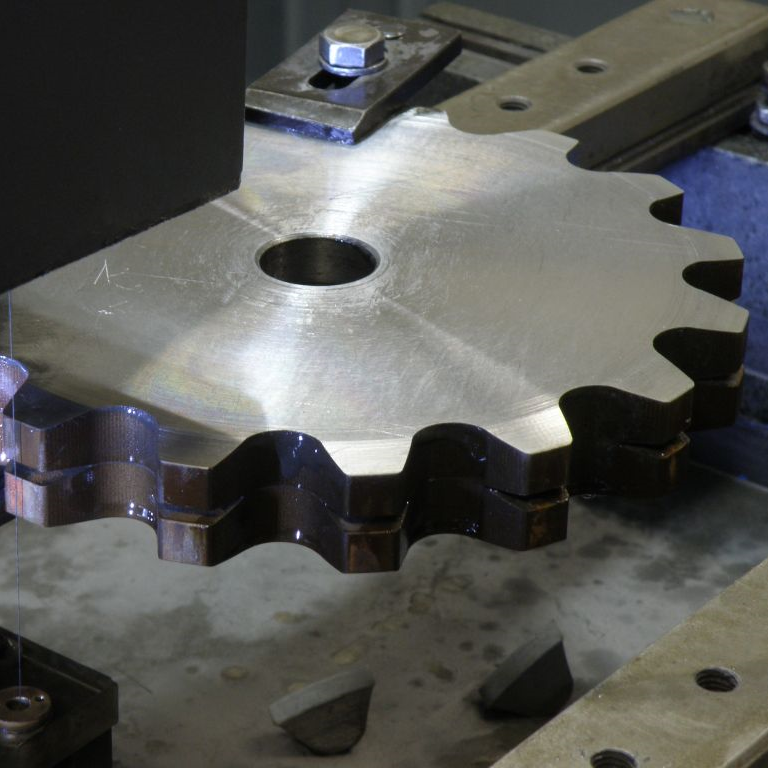
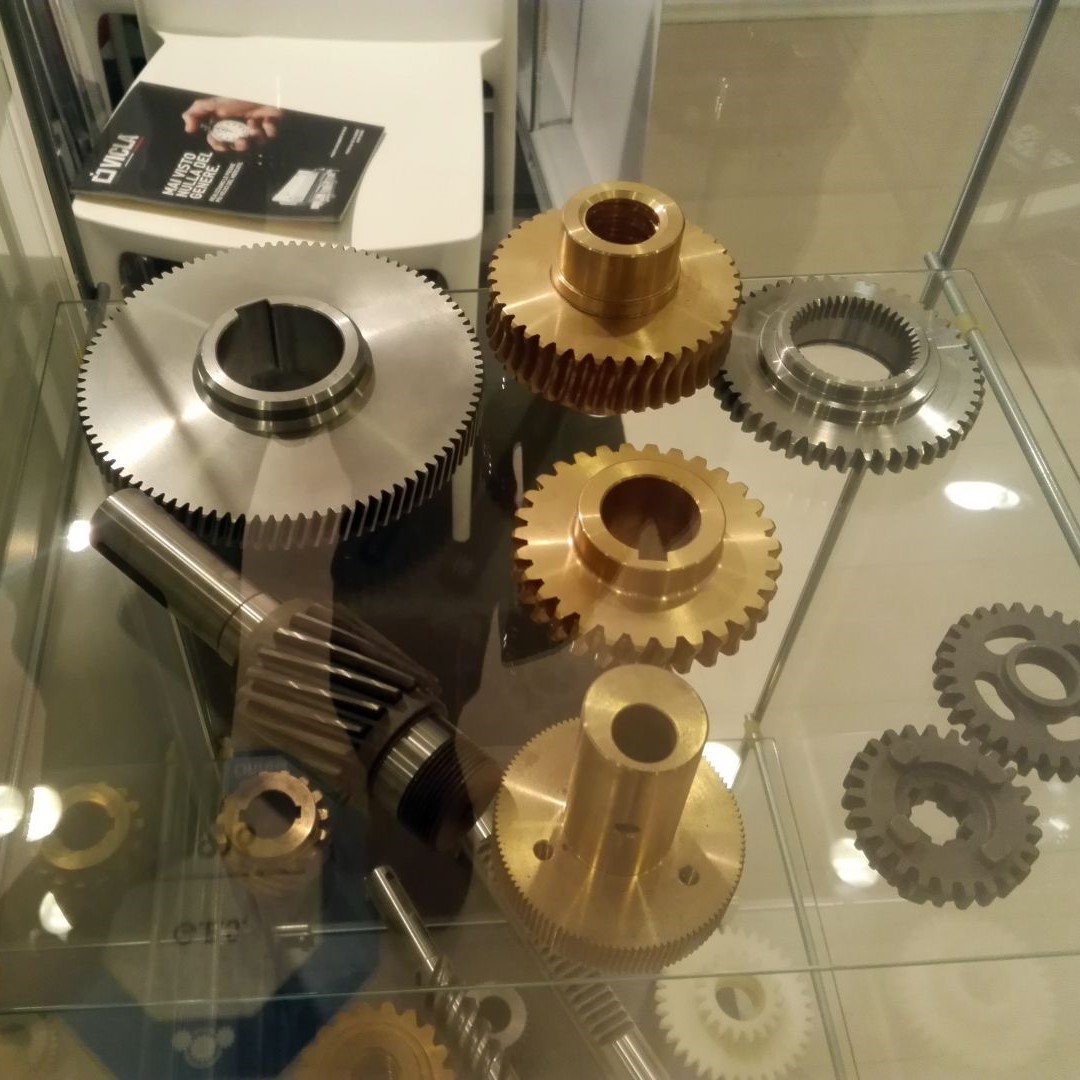
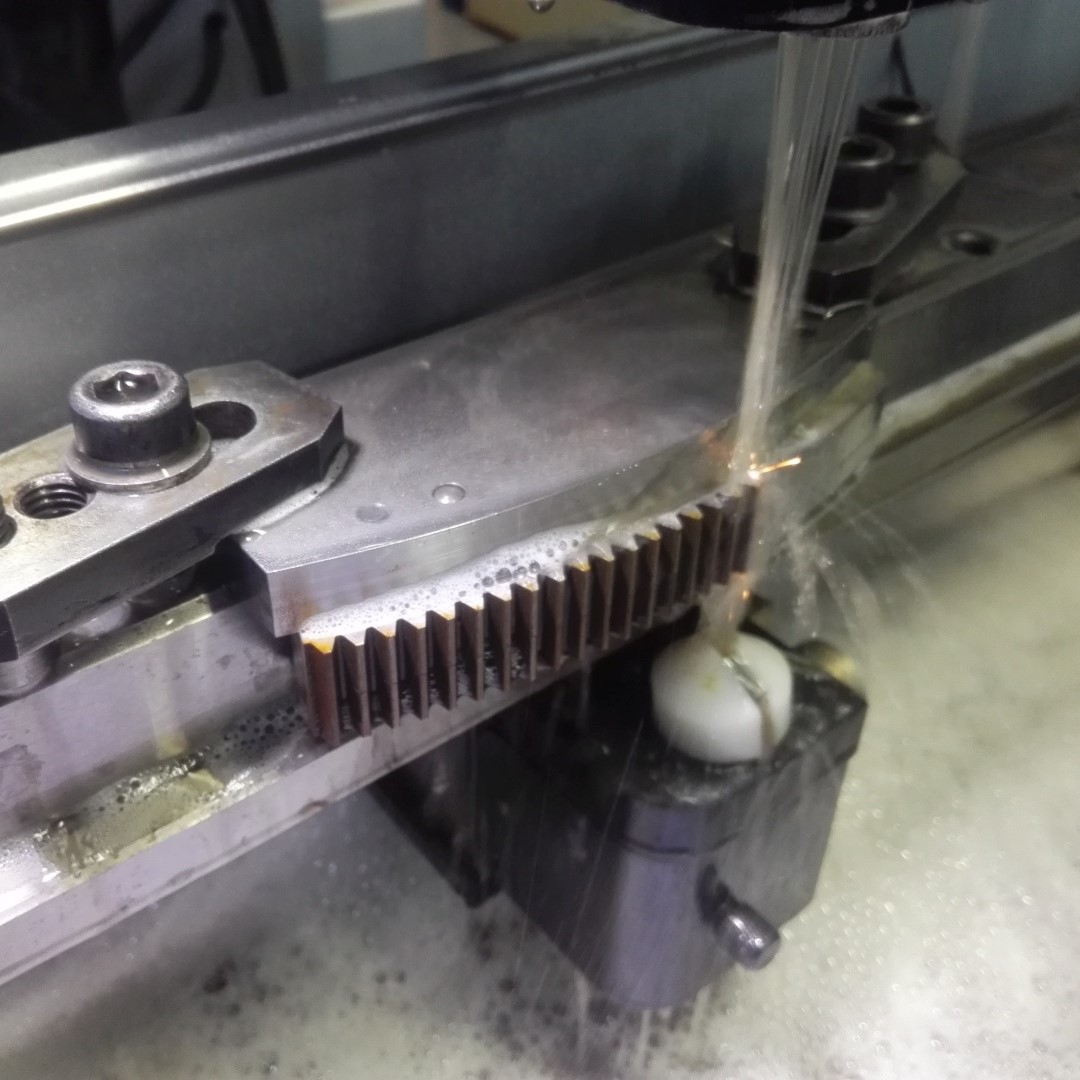
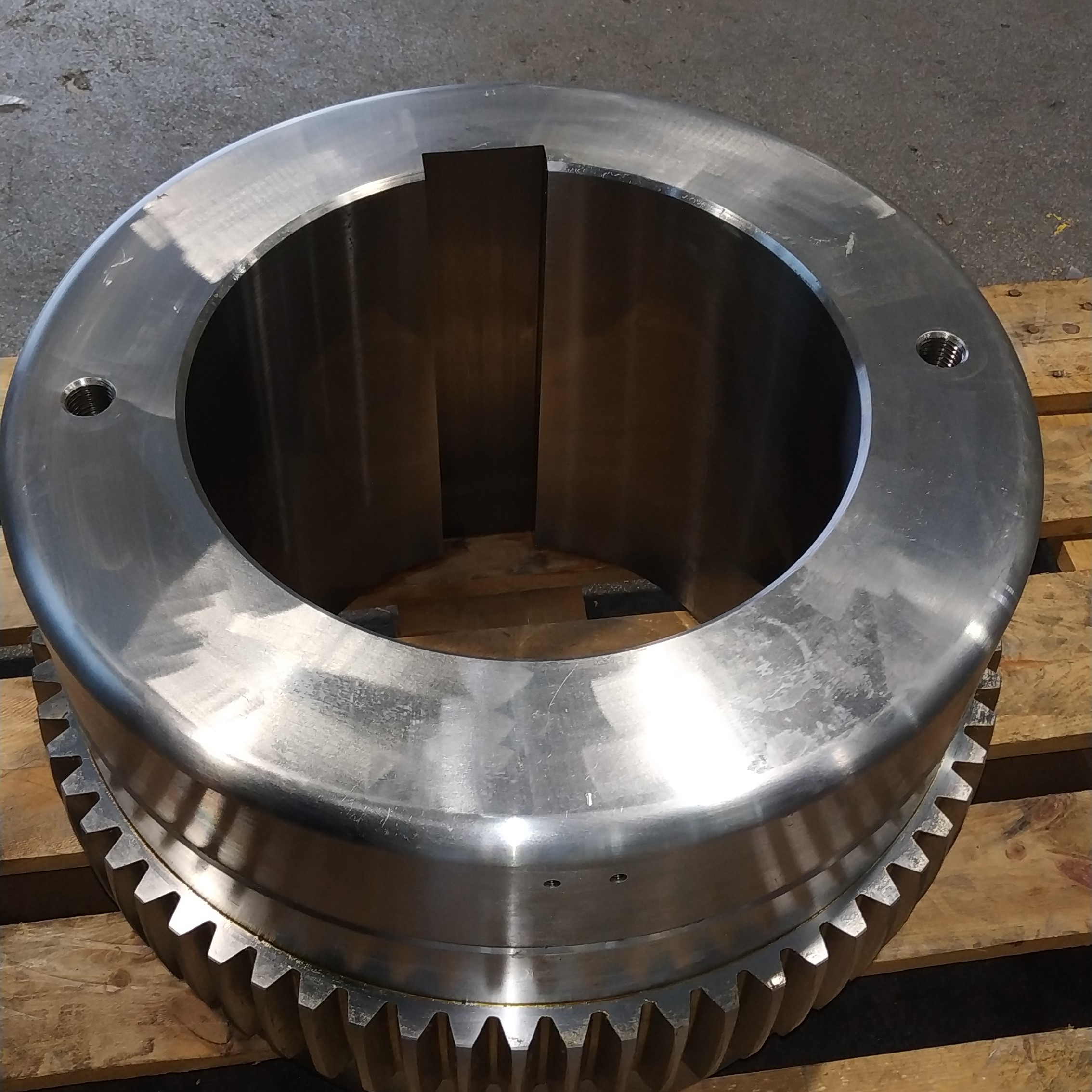
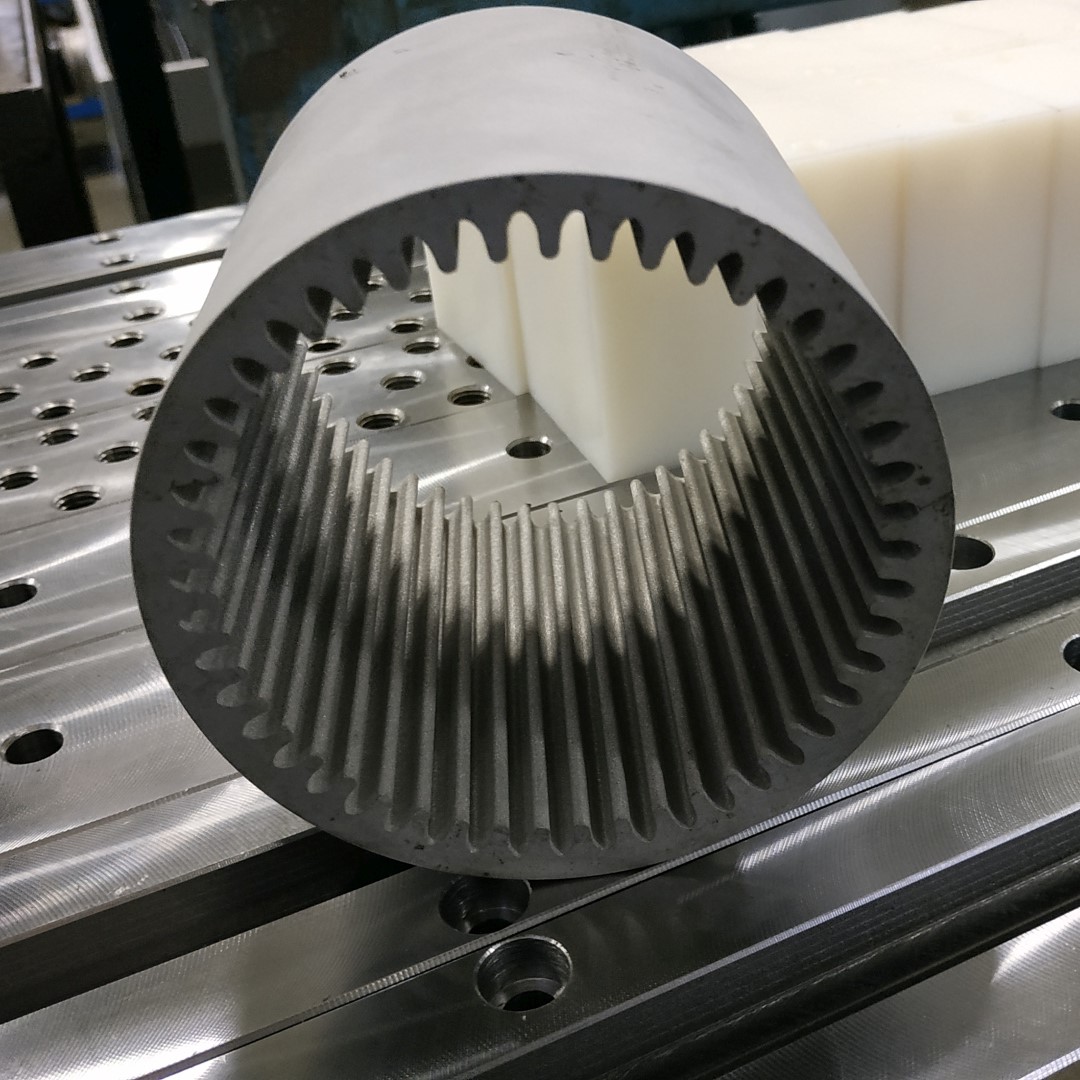
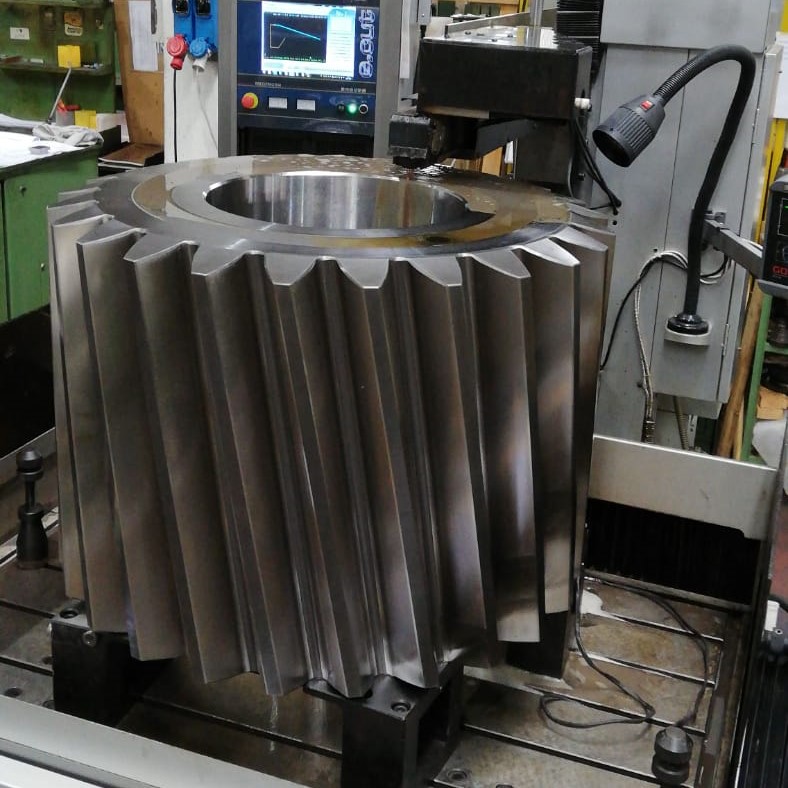
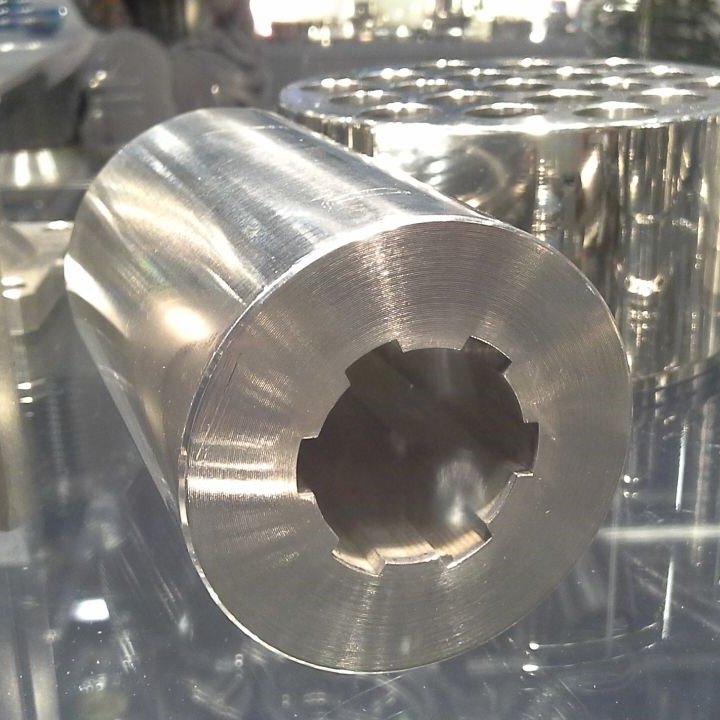

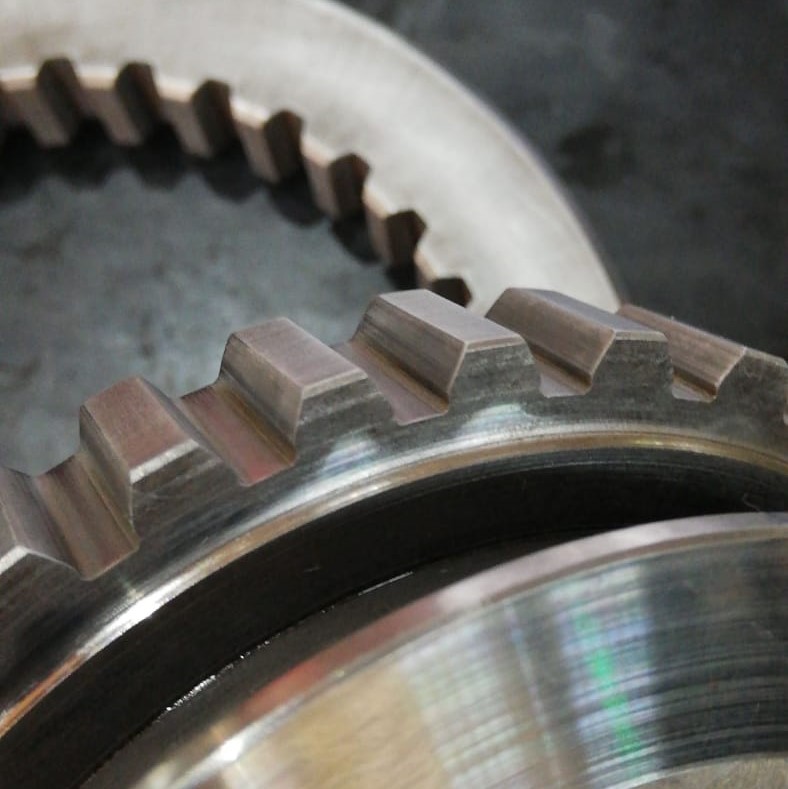
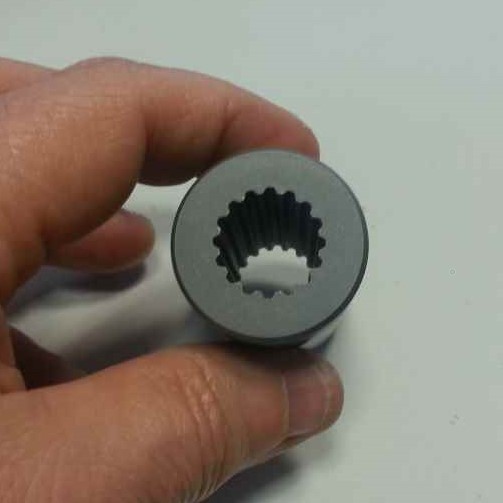
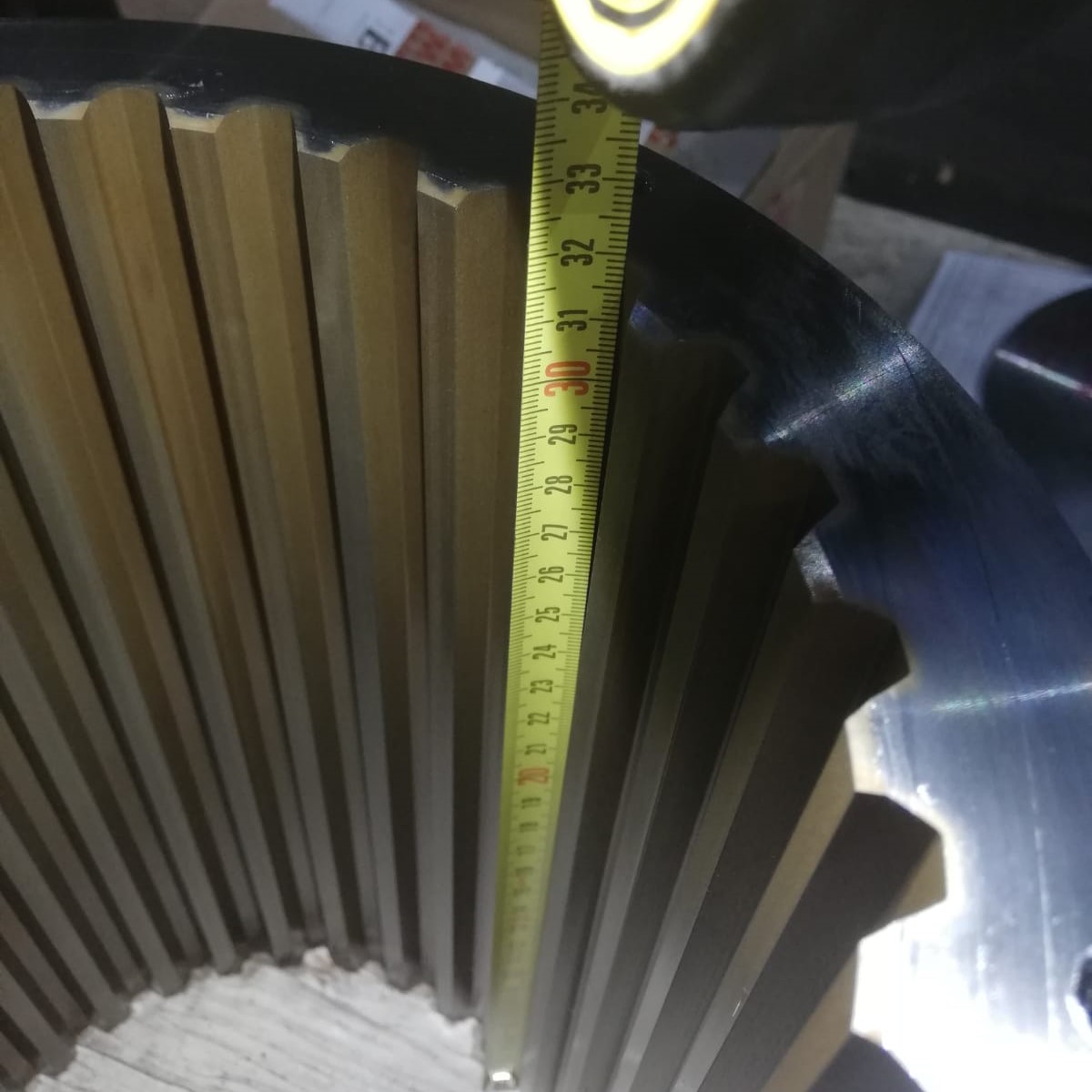
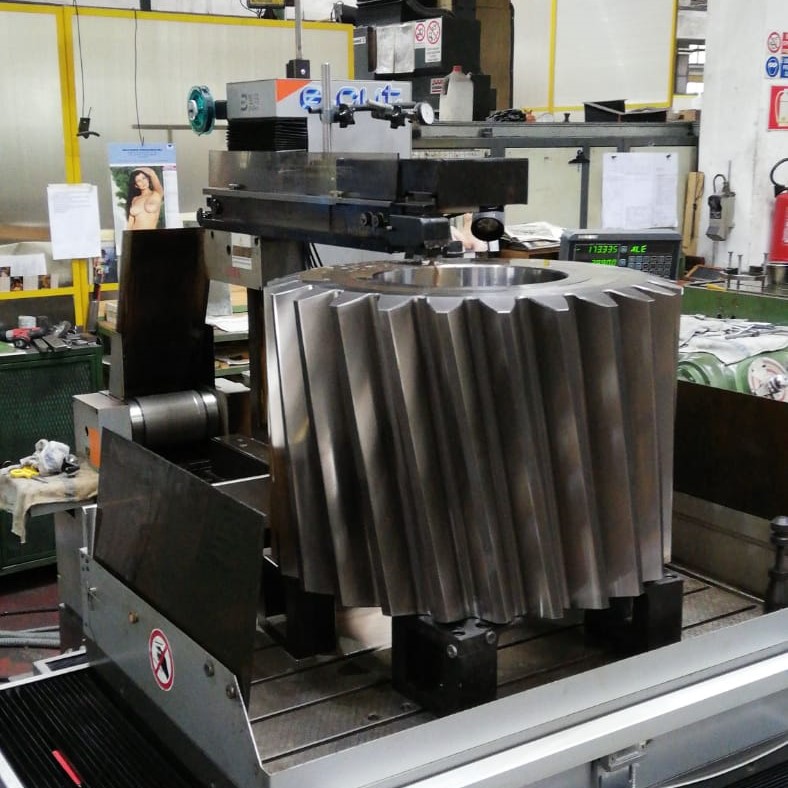
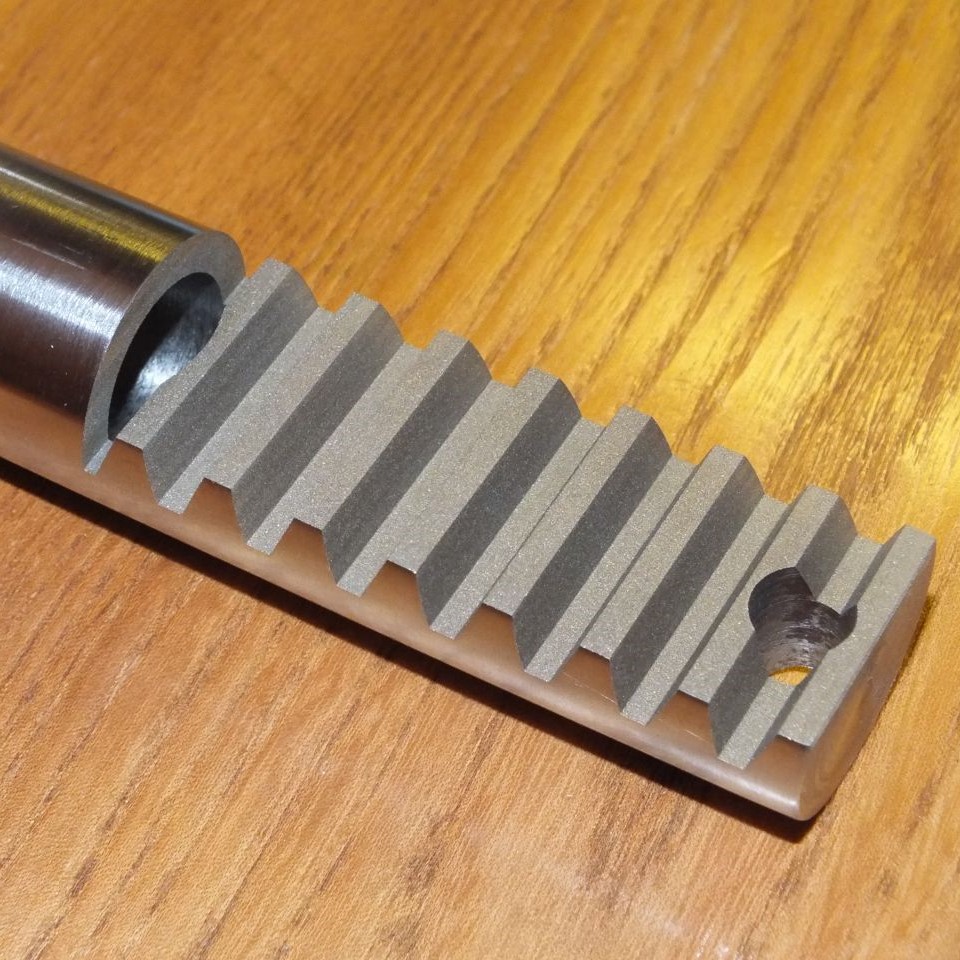
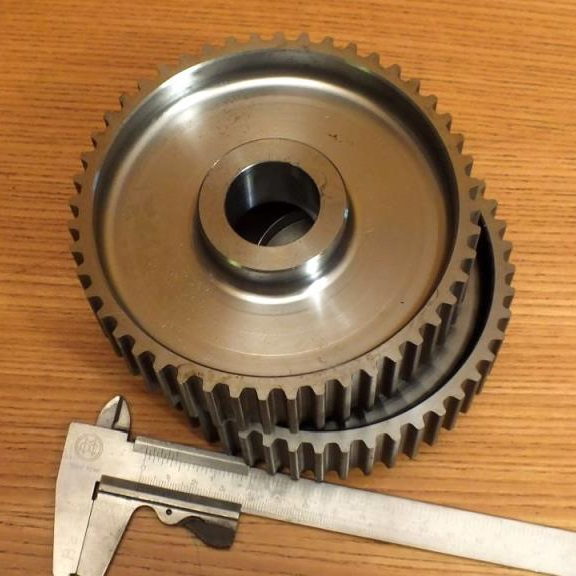
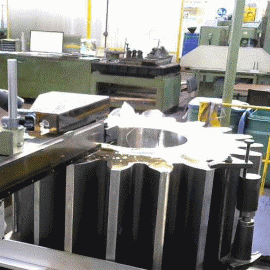
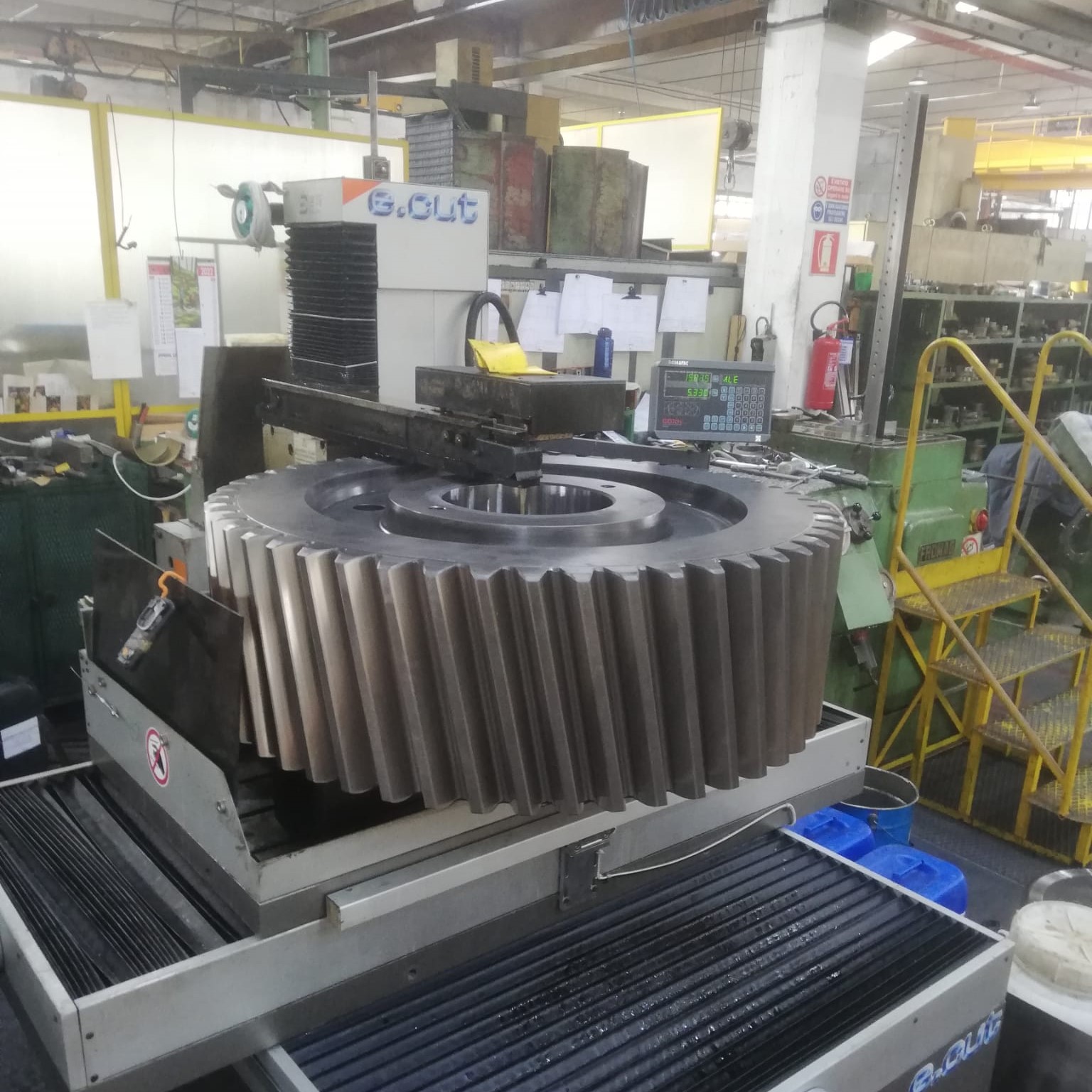
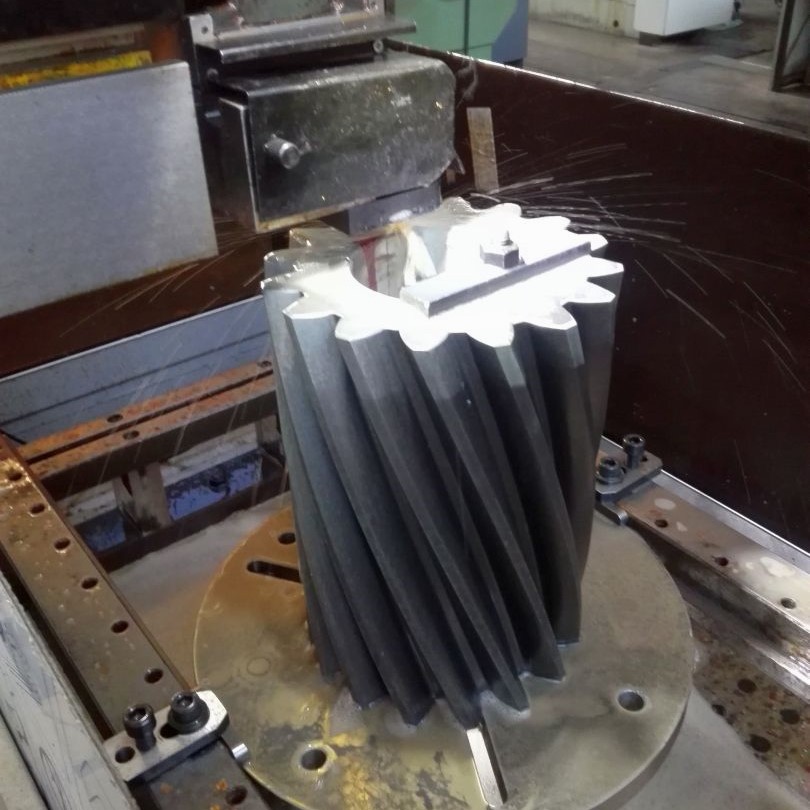
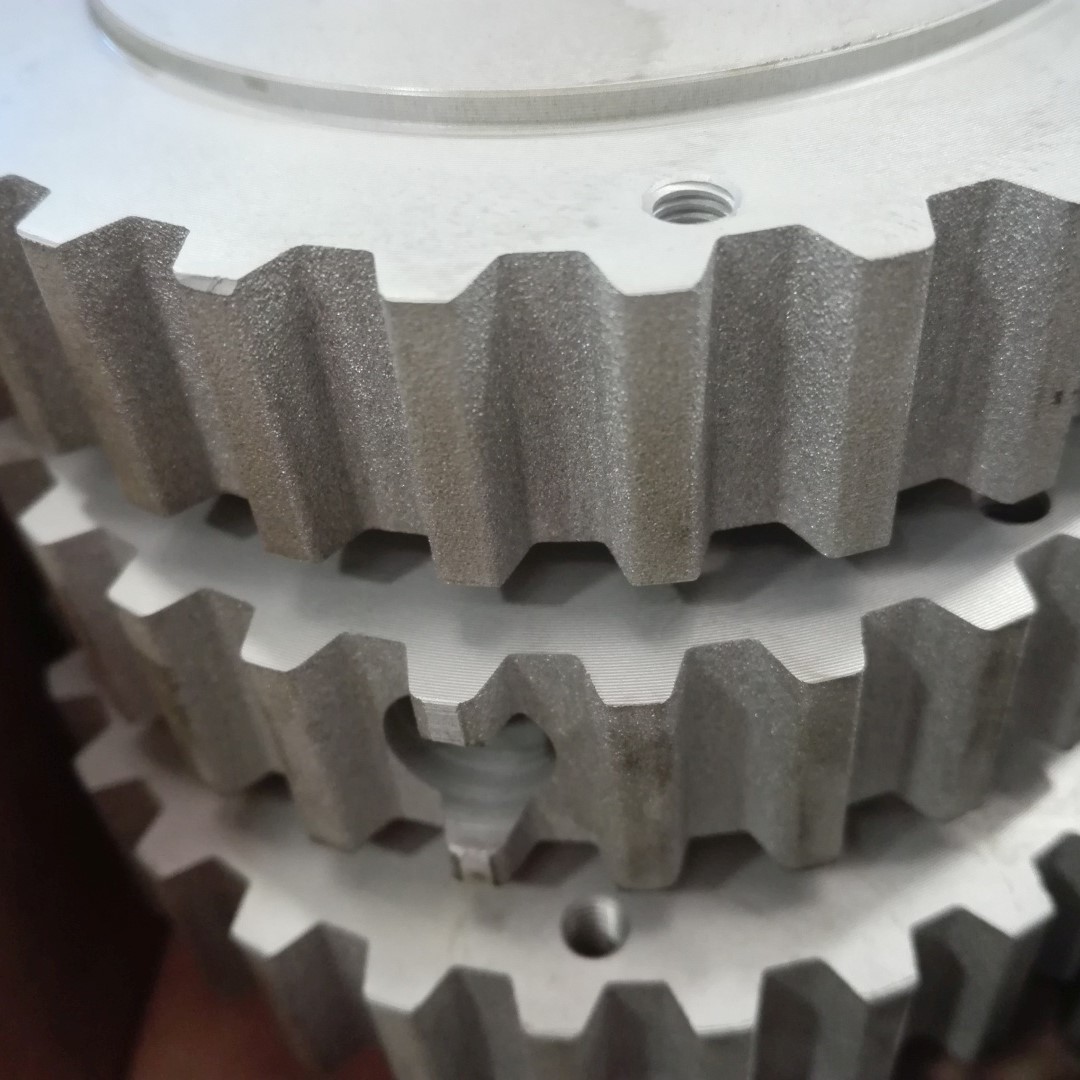
TITANIUM, INCONEL, STAINLESS STEELS
Low operating cost opens Ecut’s use to machining materials that machined by chip removal would be much more expensive. Cutting leaves usable scraps instead of chips !!! .
The costs of conventional wire erosion make it uneconomical to use, and the lack of an immersion tank allows cutting even on large workpieces.
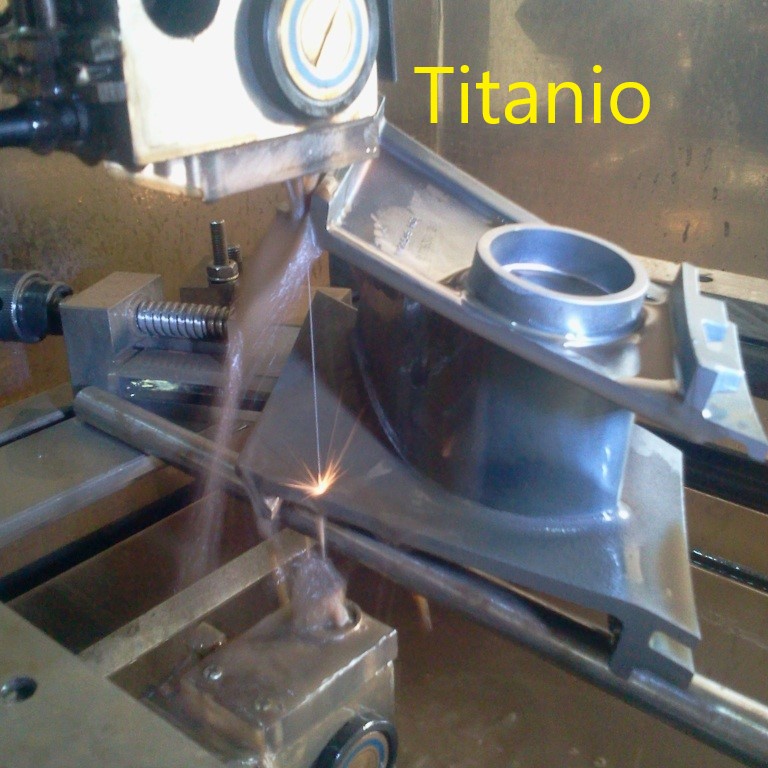
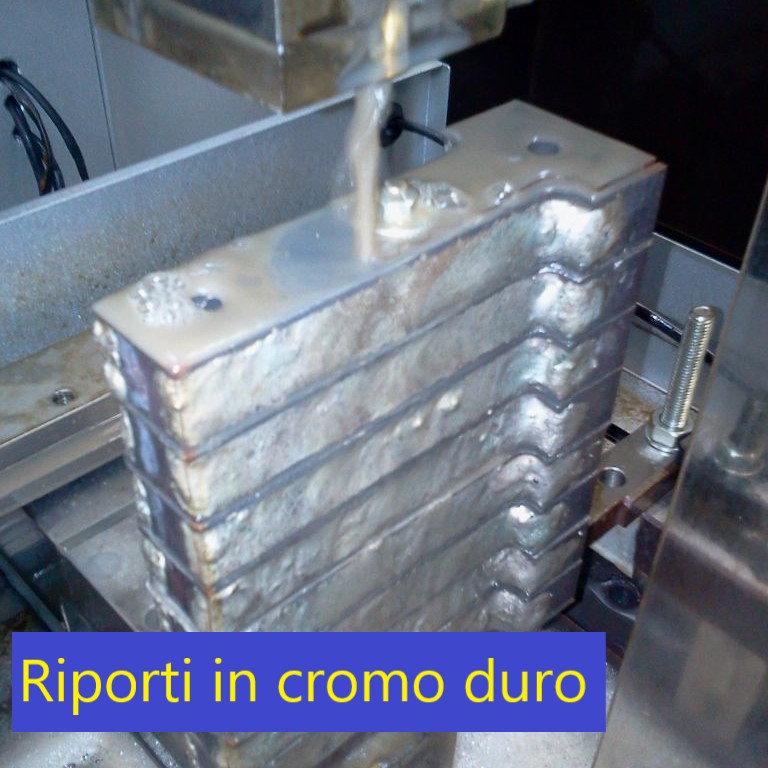
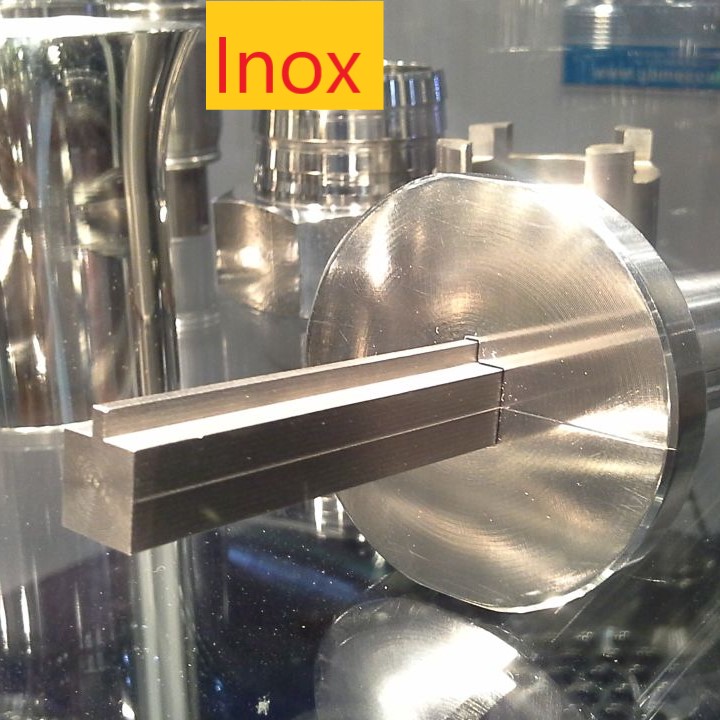
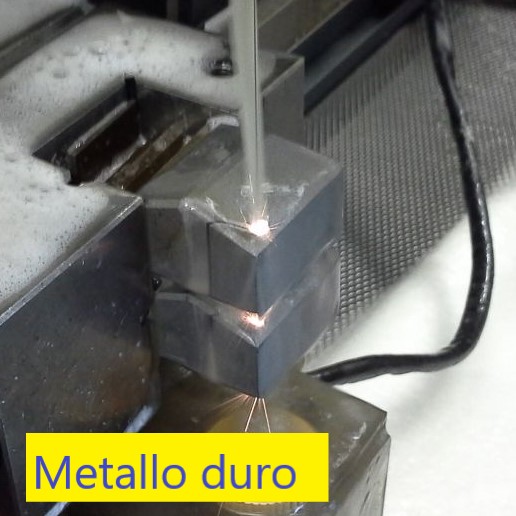
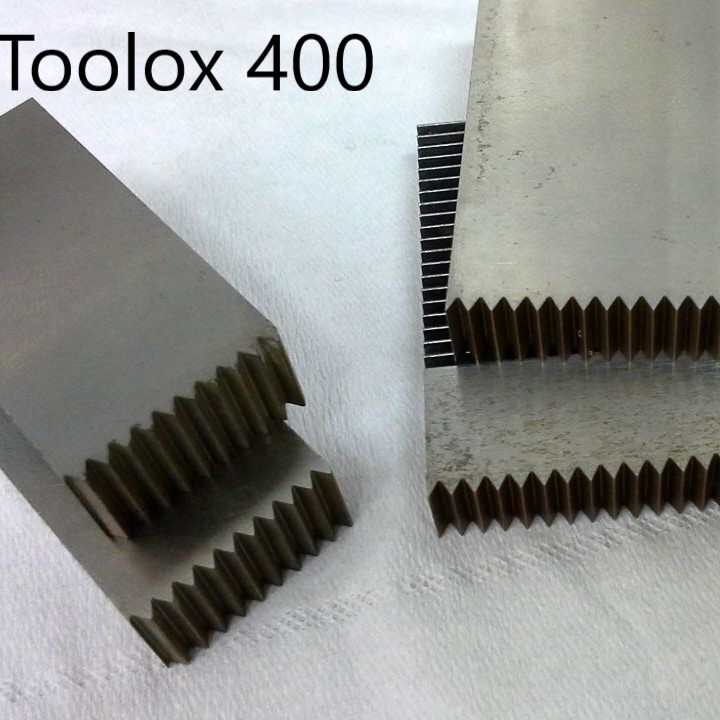
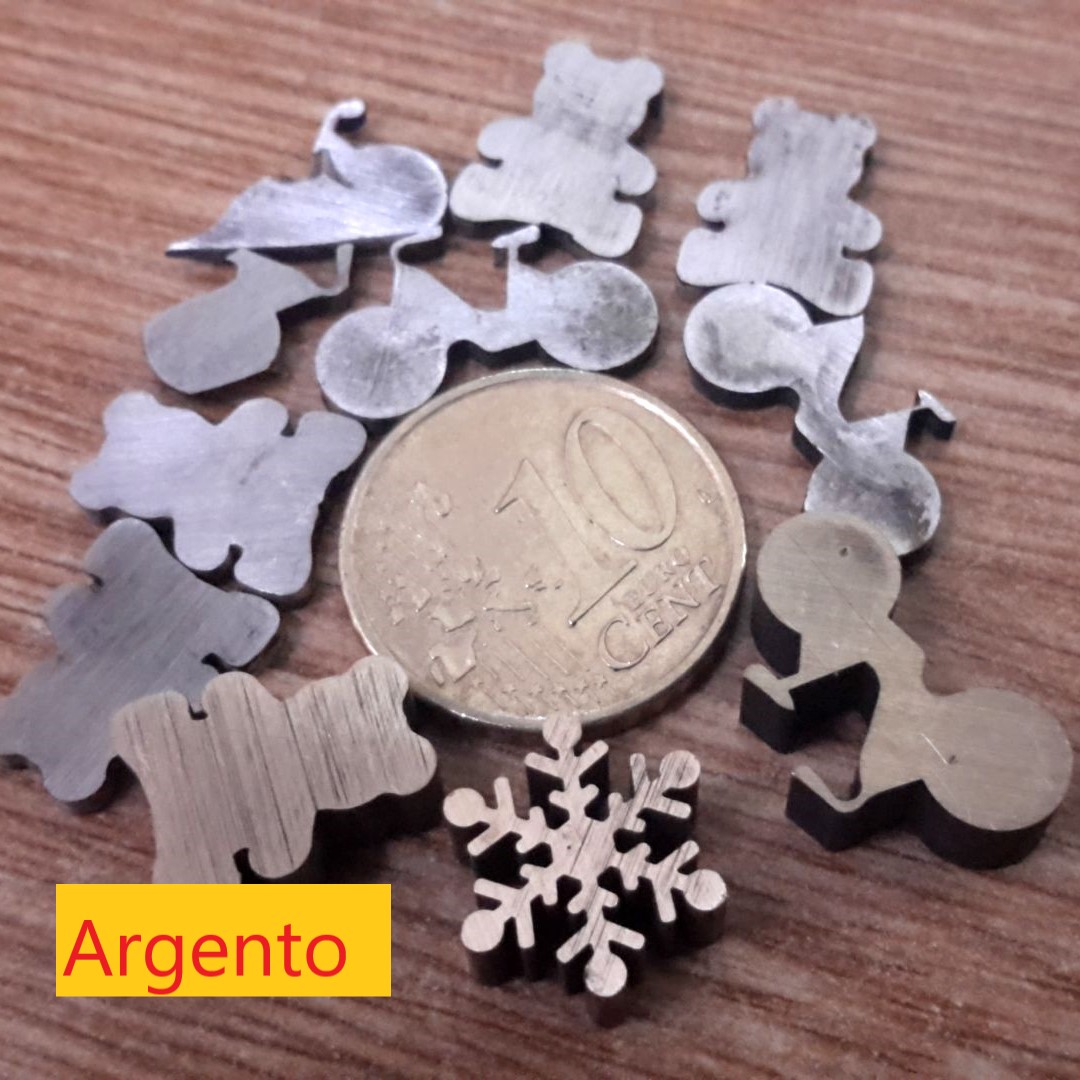
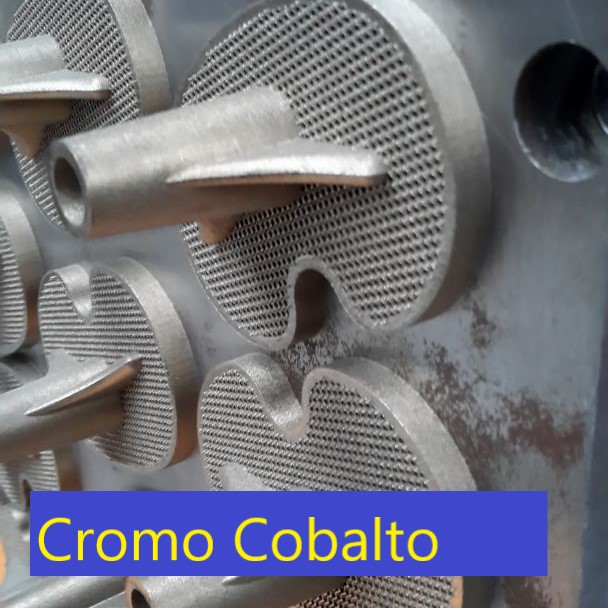
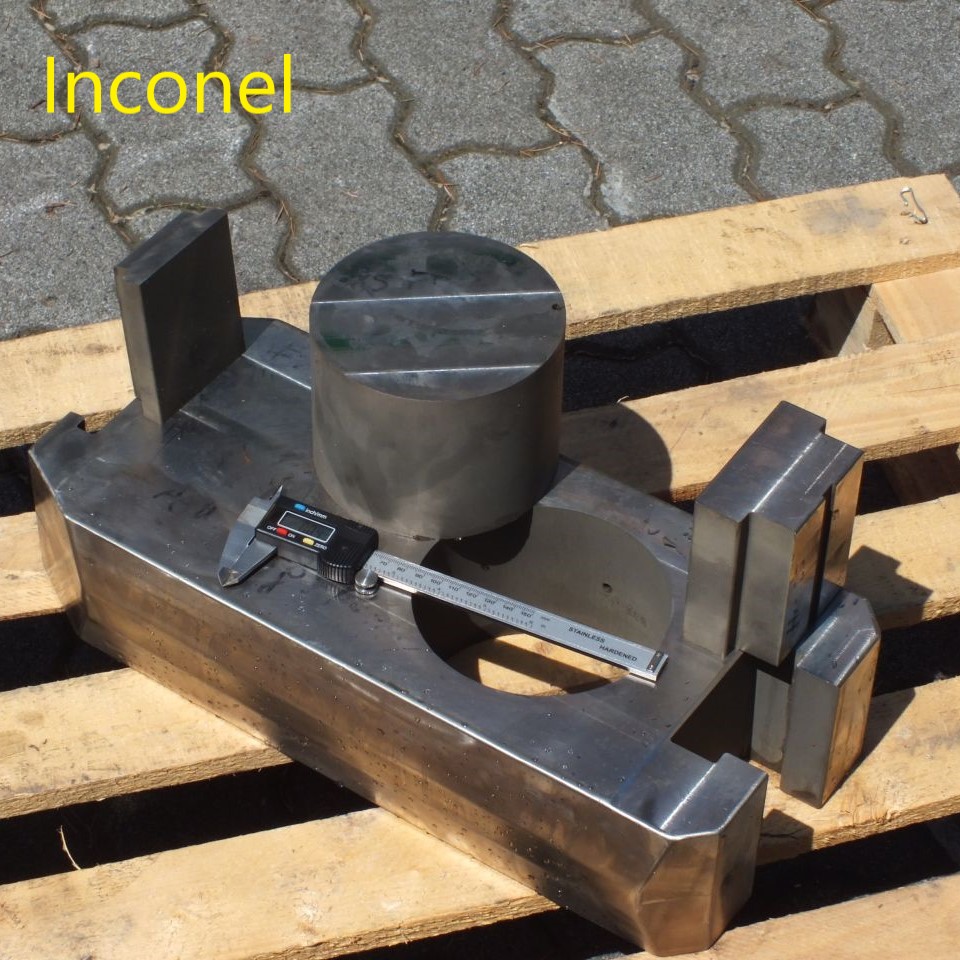
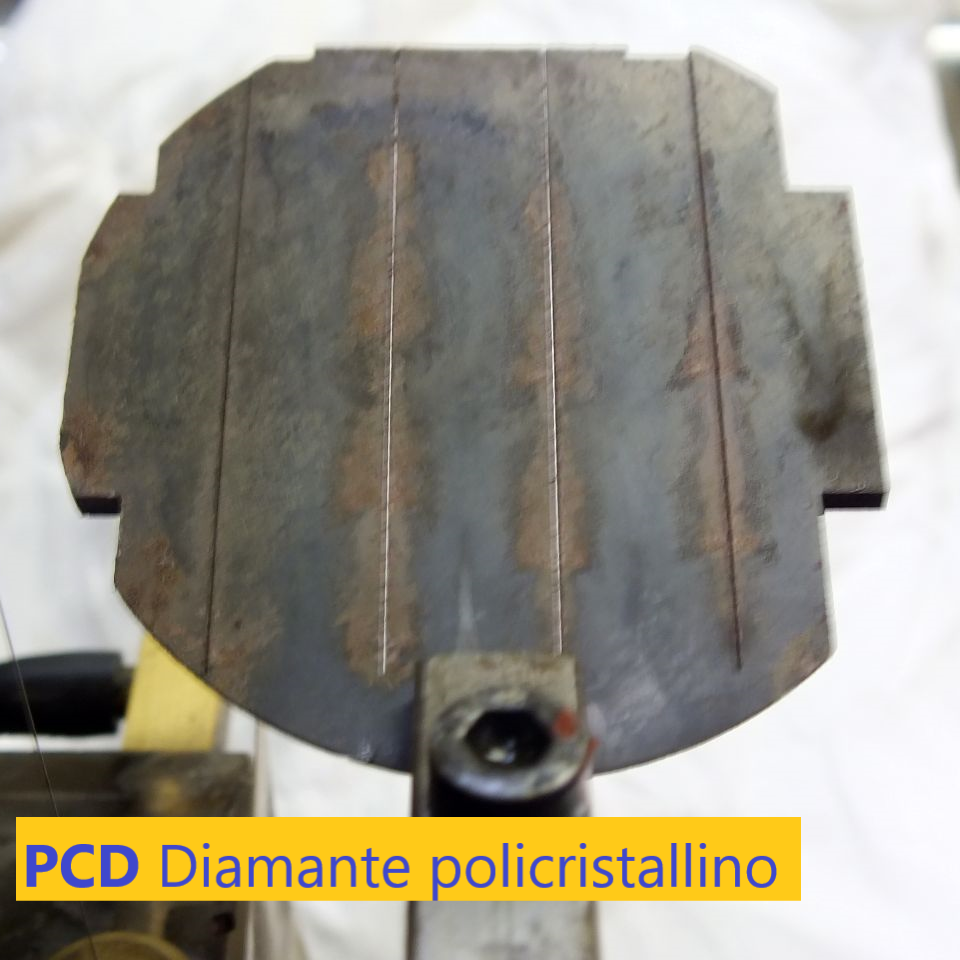
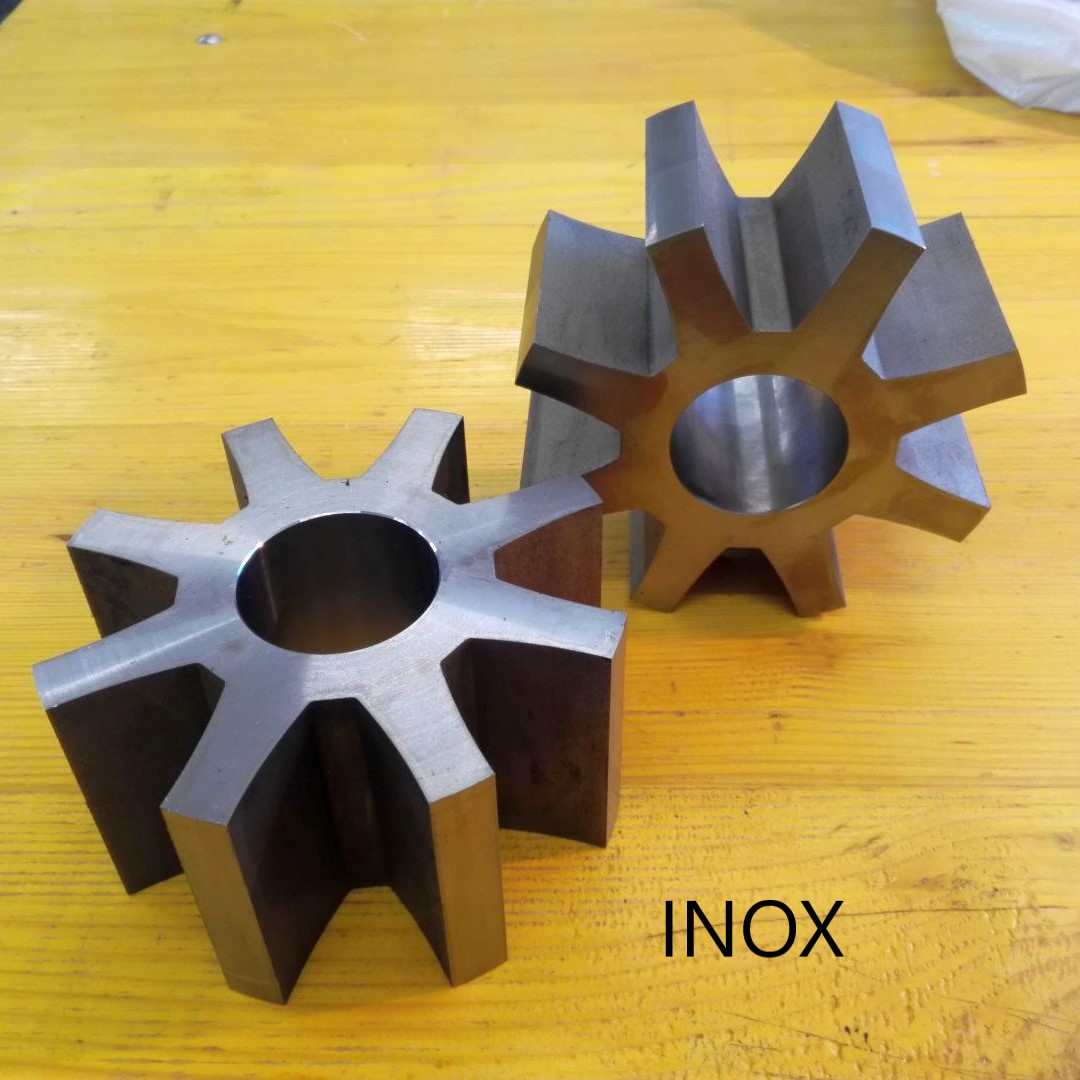
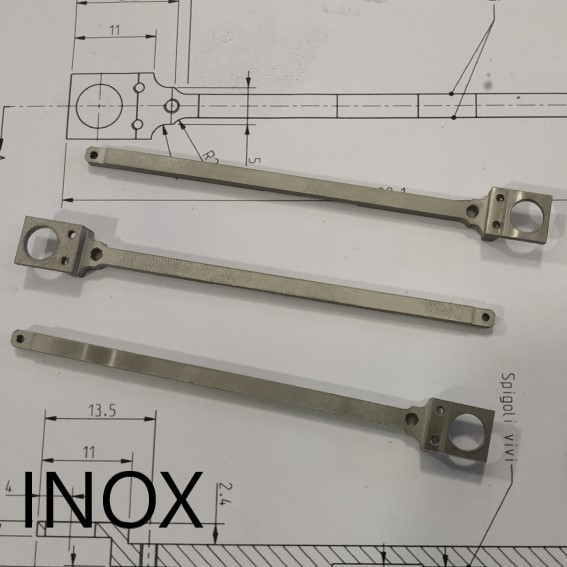
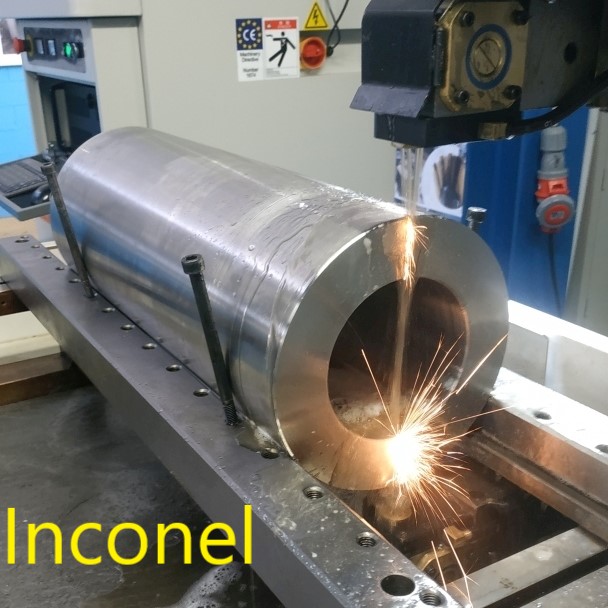
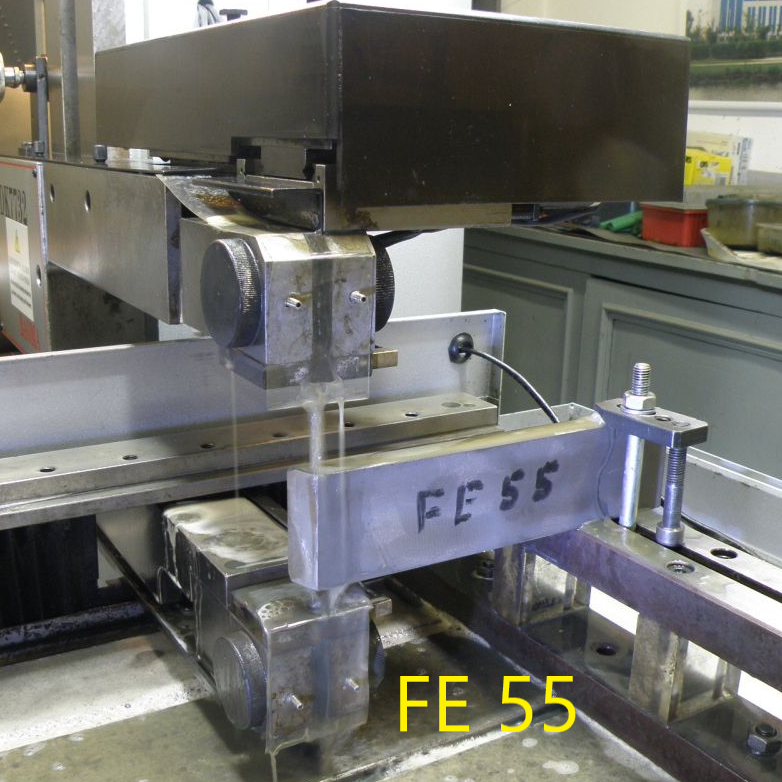
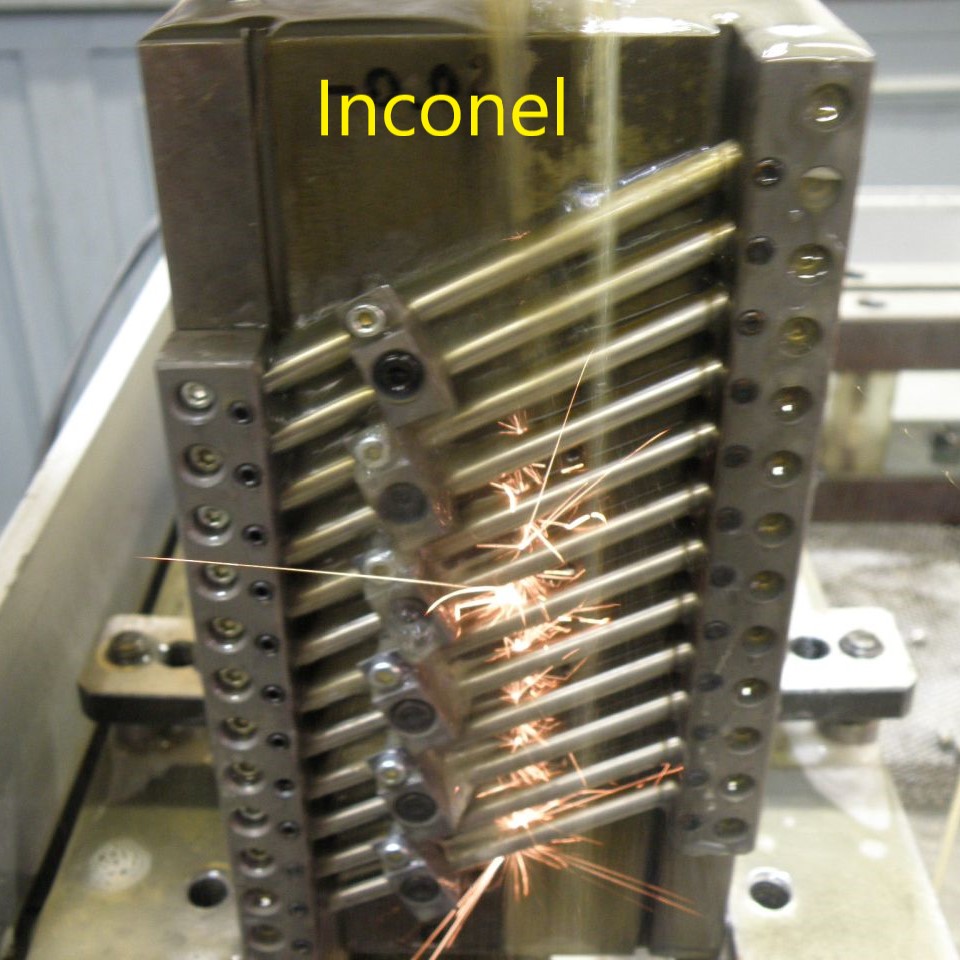
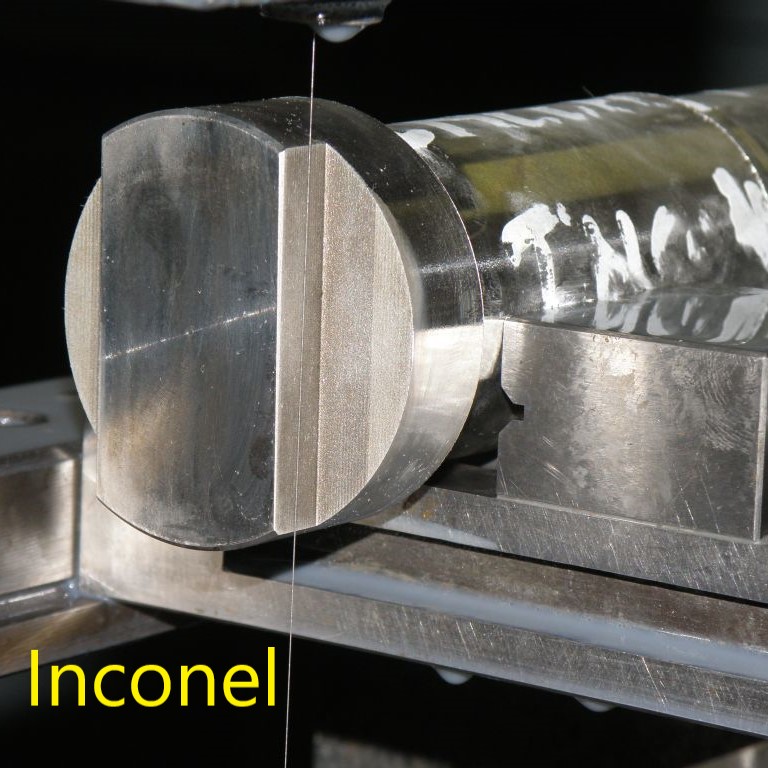
TUBES, THIN TUBES, PROFILE CUTTING OF TUBES, TUBULAR STRUCTURES
Ecut’s cutting is burr-free. Light clamping is enough, with no risk of deformation. Drop cooling allows machining of overlapping parts or complex profiles.
The ability to cut the full ‘height, without the hindrance of the plunge tank allows pendulum machining. One jig is loaded while the other is working !
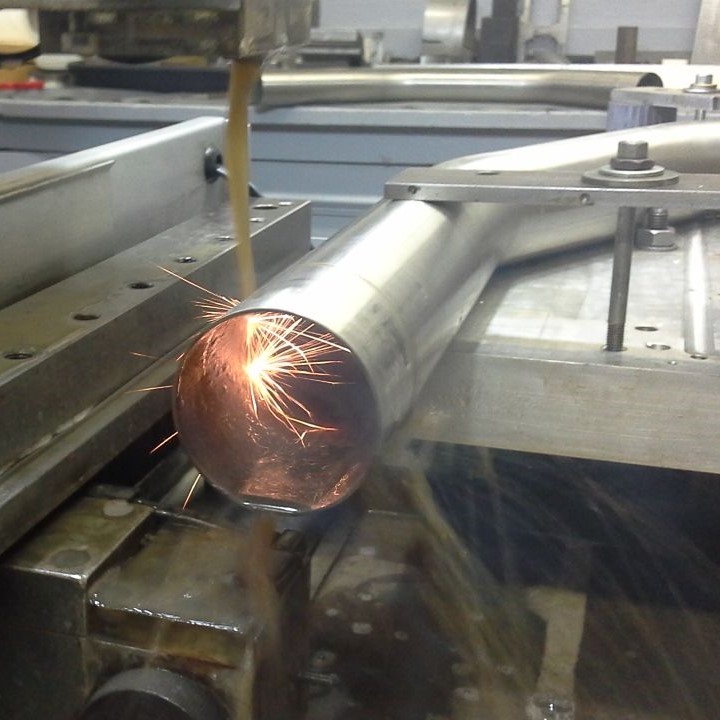
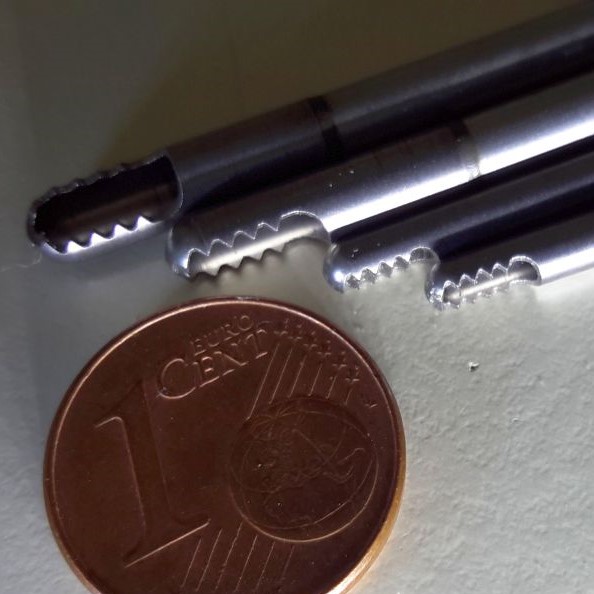
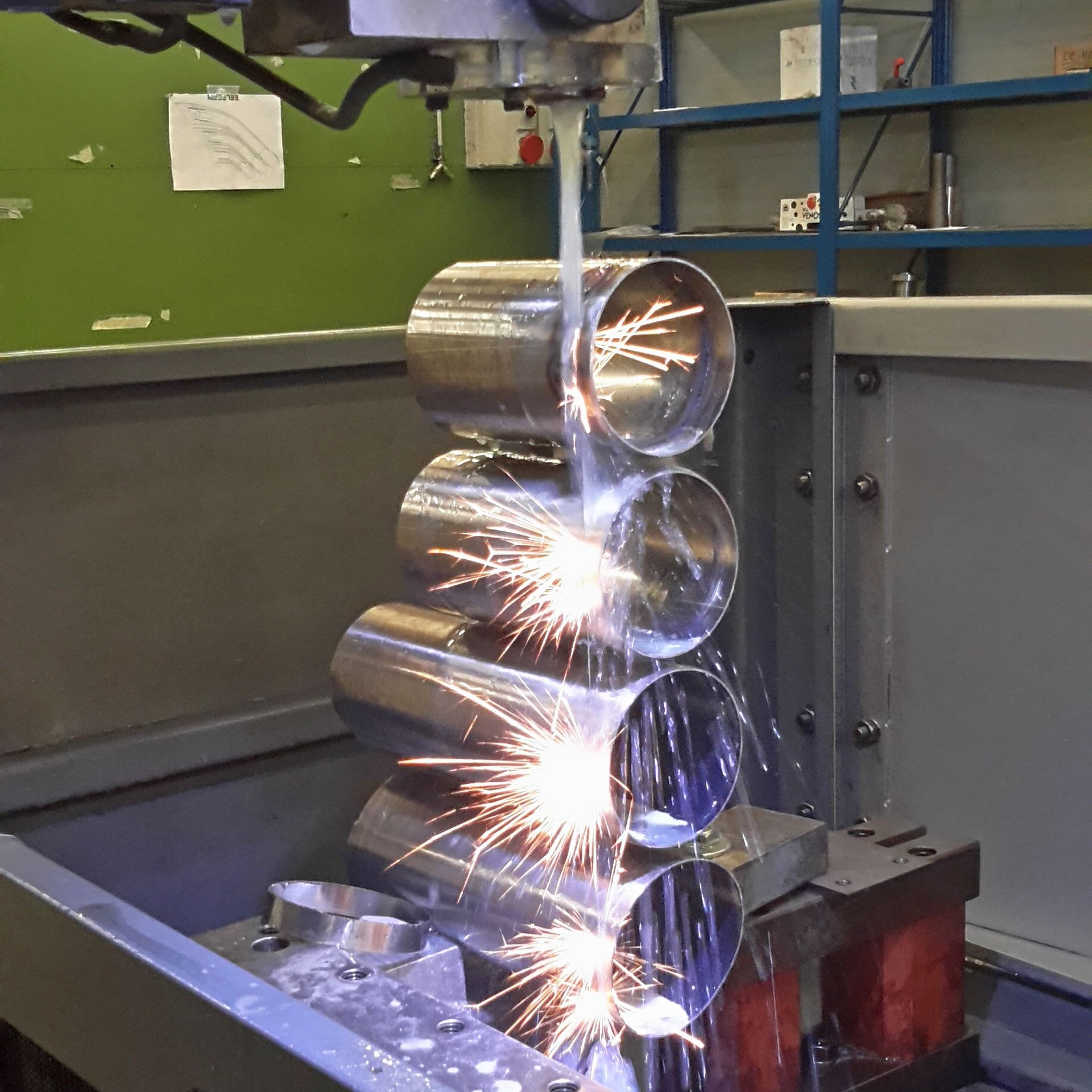
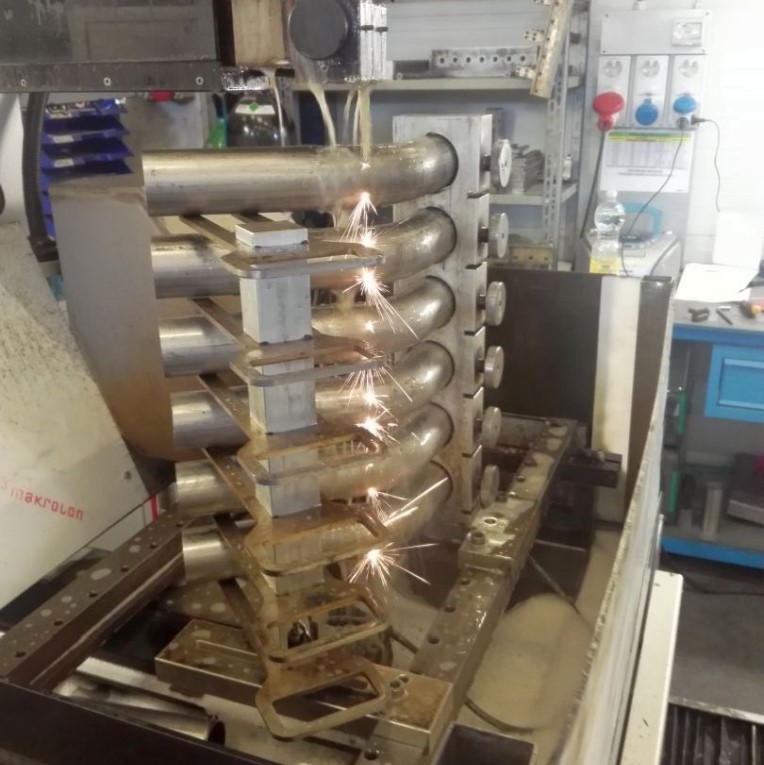
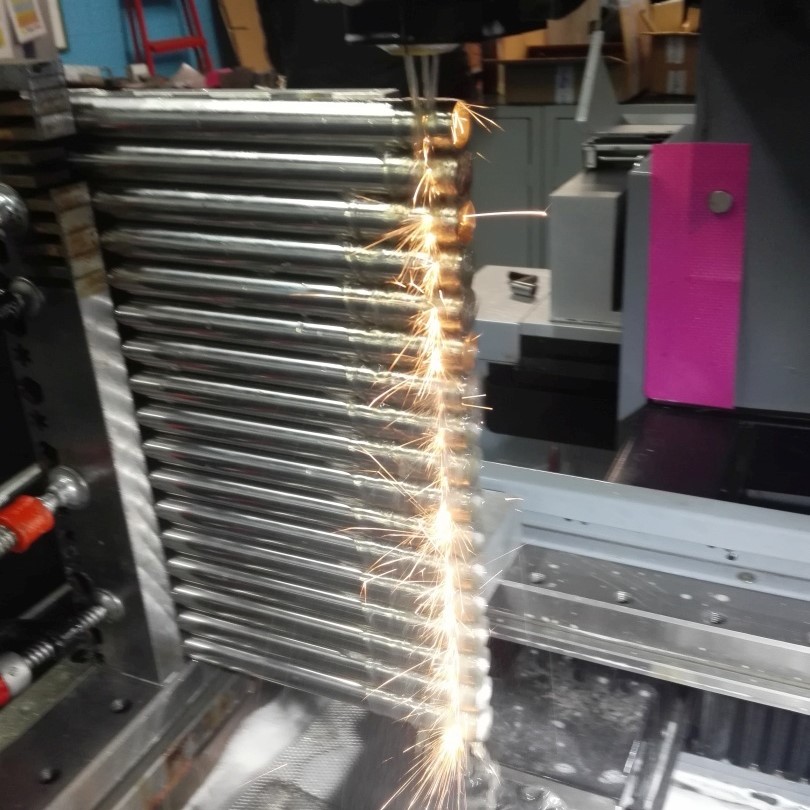
CUTTING AUTOMATION – DIVIDERS
The lack of an immersion tank, like conventional wire erosion, makes possible the ‘use of dividers, rotary tables, and workpiece moving equipment.
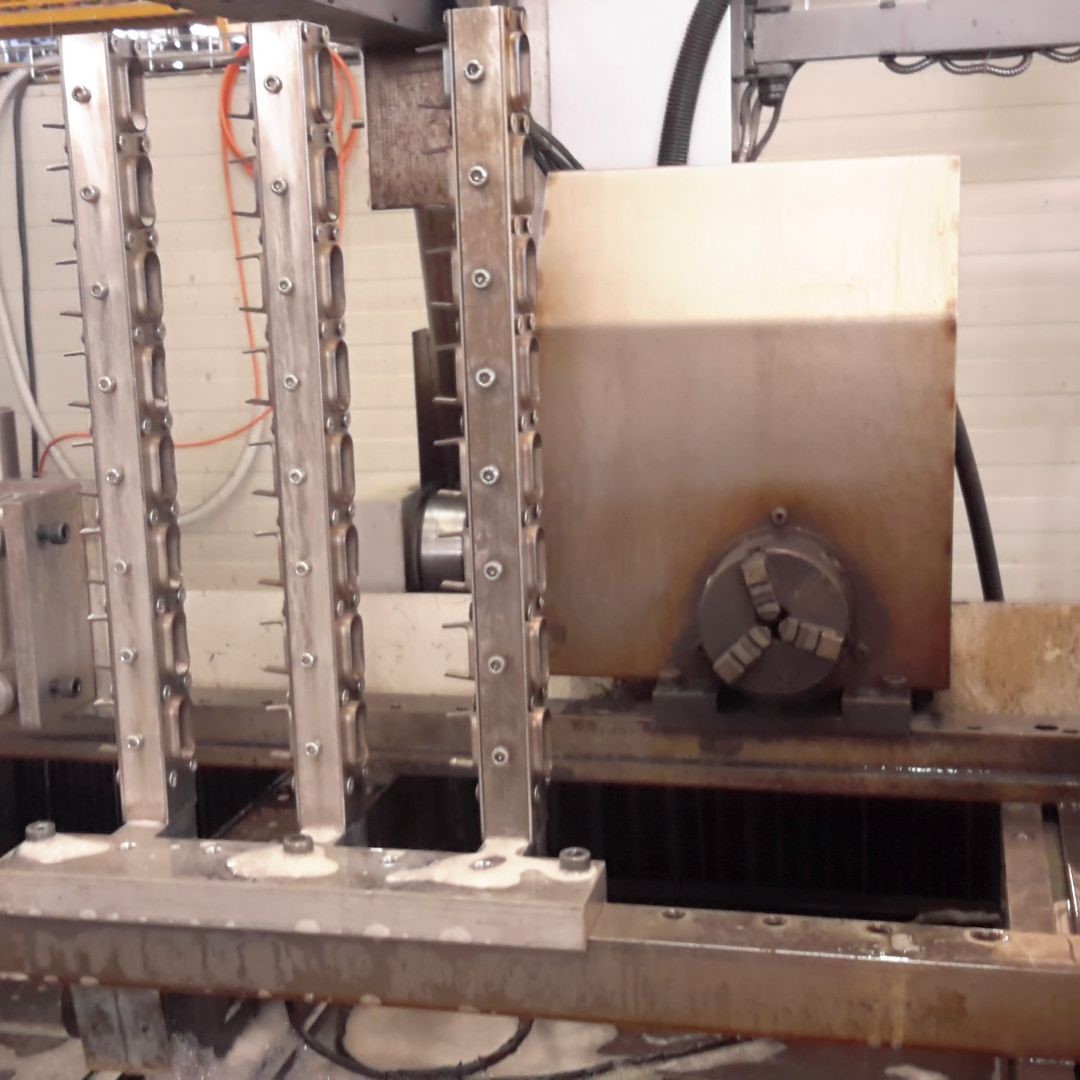
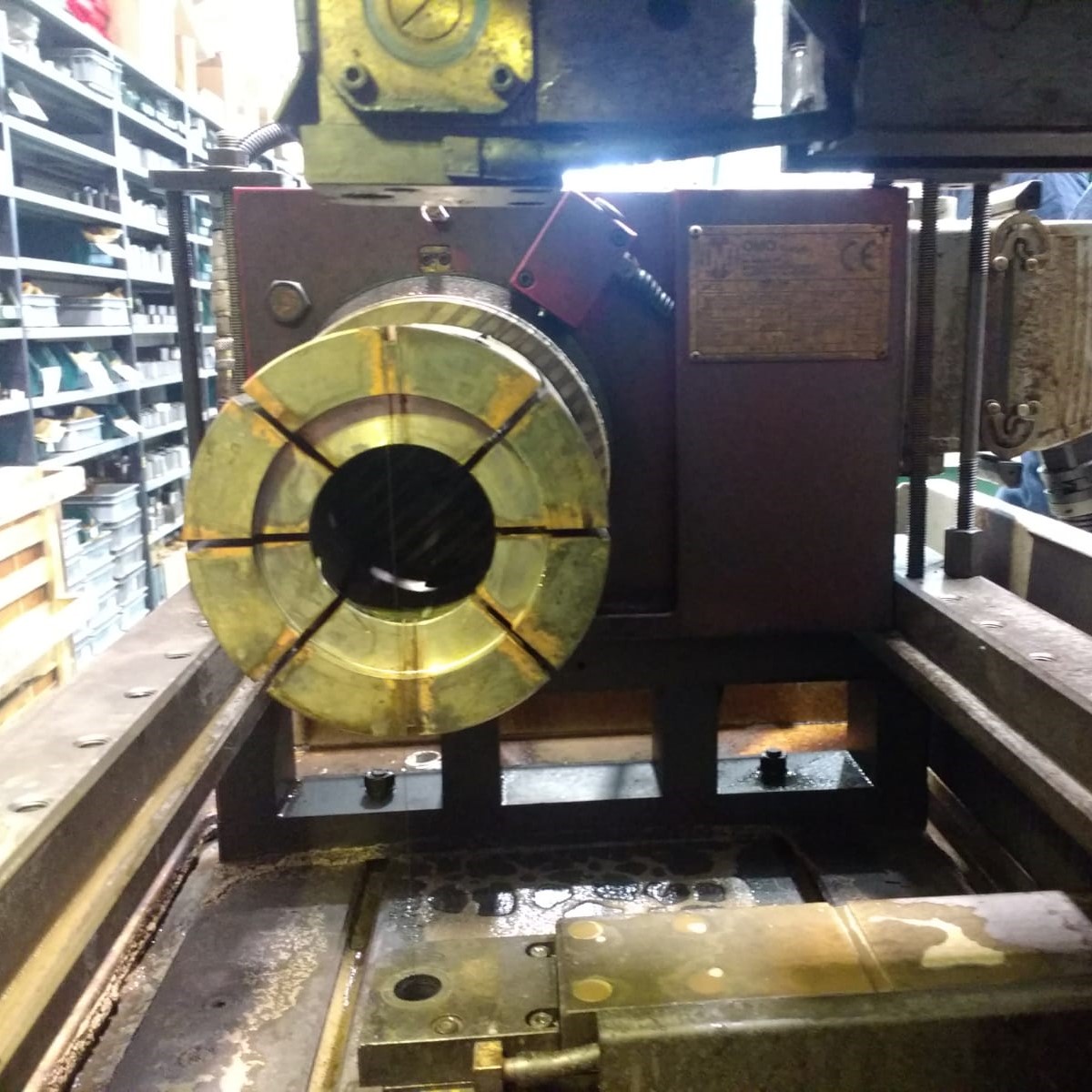
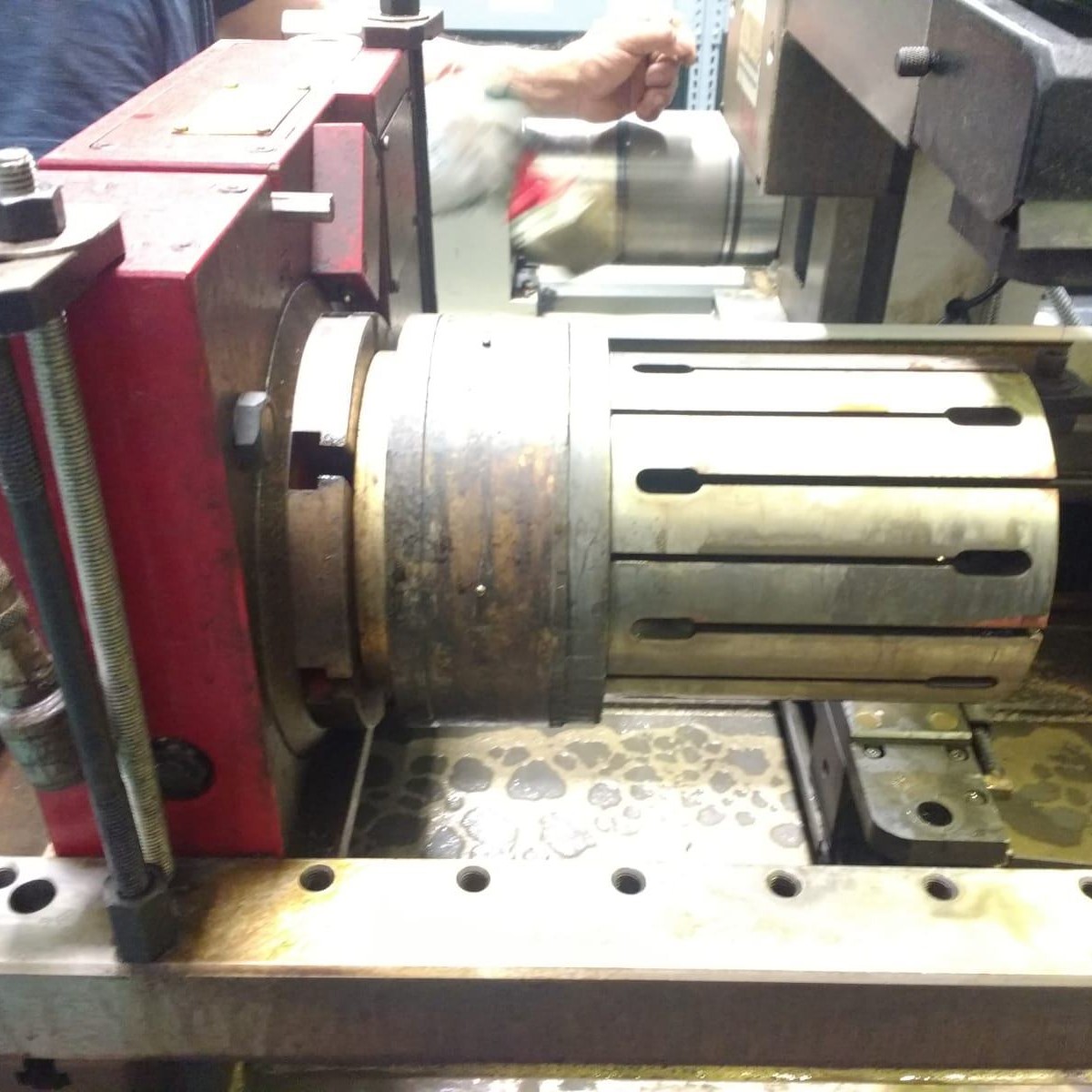
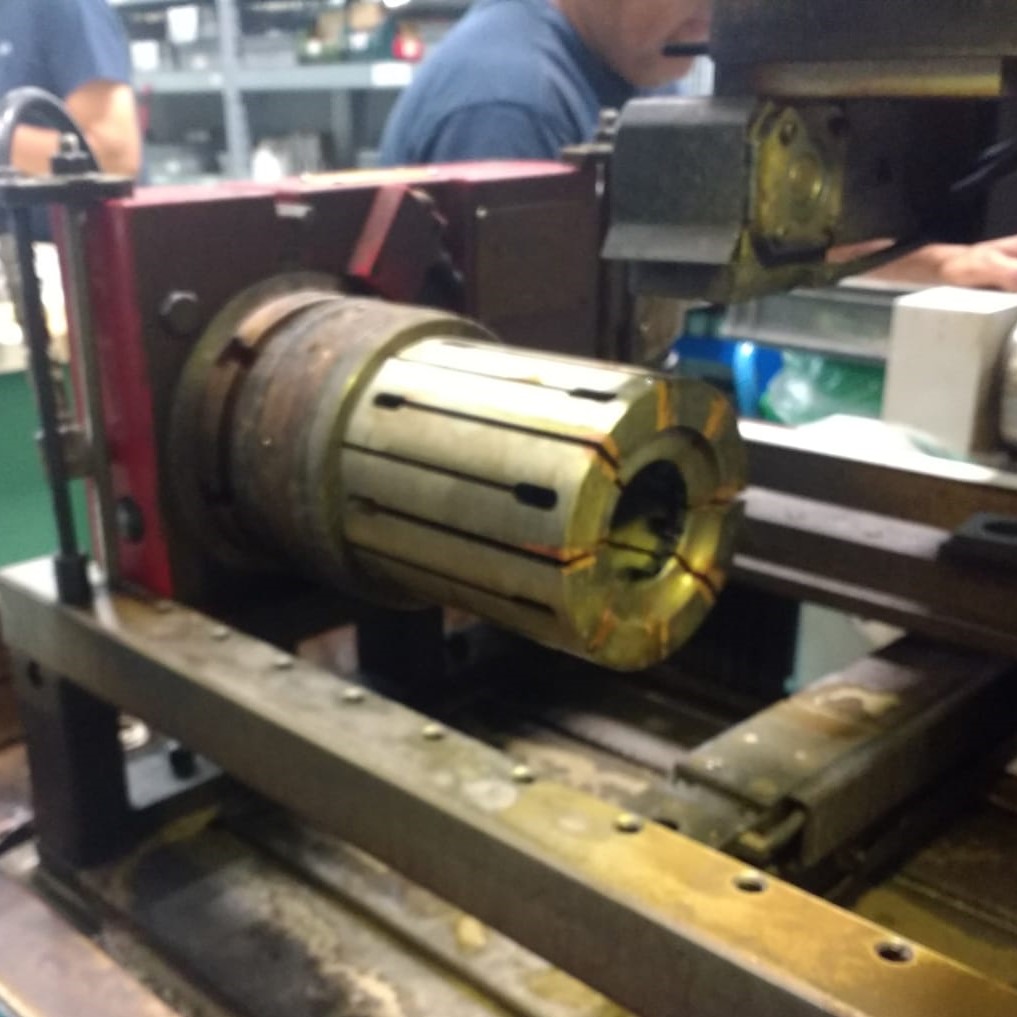
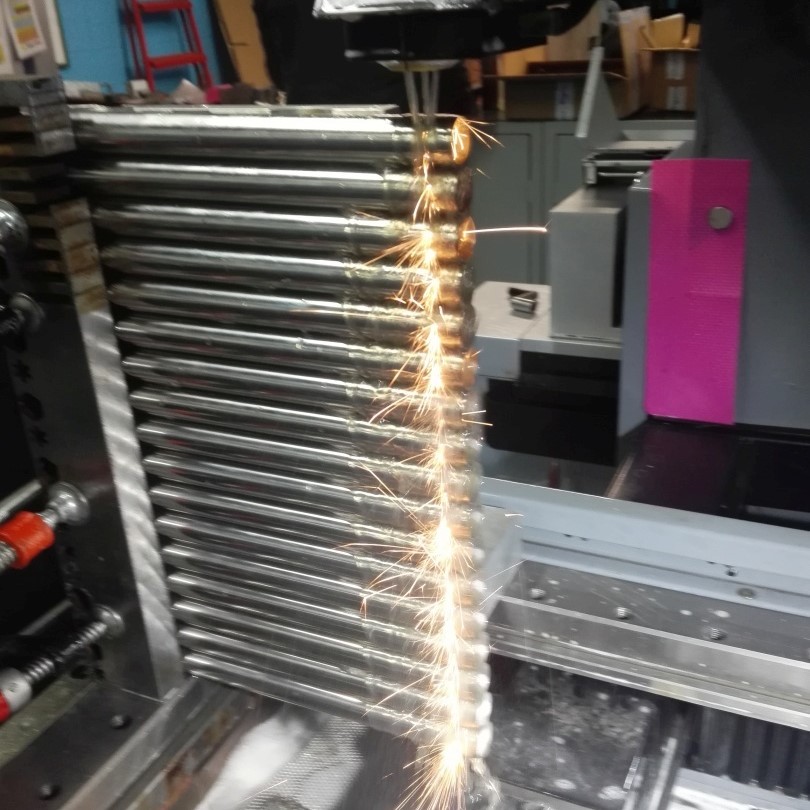