A new way to cut metals
For more than 30 years, these machines have been widely used in eastern countries for metal cutting and processing.
The basic reason for the widespread use is the low cost of operation.
The simplicity of the machine’s structure results in negligible maintenance costs, low incidence of breakdowns, and a decidedly low machine cost.
The ability to cut even with the smallest models very high thicknesses, up to 500 mm, with an accuracy within 0.015 mm and a lack of “barrel” effect, makes the system “revolutionary” compared to the expensive technology of conventional wire erosion
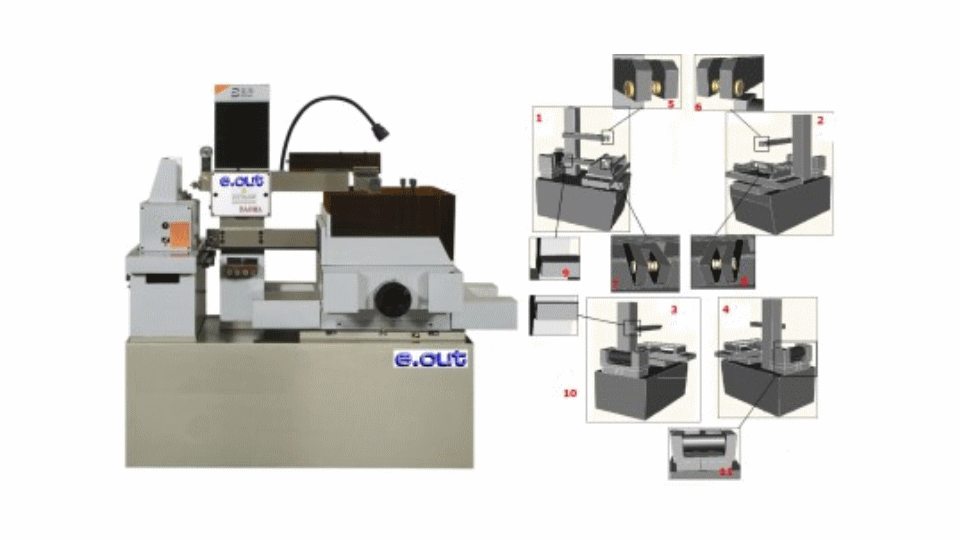
The following piece, designed and made with E.cut™ machines by G.E.S., ( https://www.gesingranaggi.com ) perfectly illustrates the great possibilities of the system.
It could have been made with conventional machining by removal, or with any conventional wire erosion, but the cost would have been at least 10 times higher.
With Ecut there are no tools to preset and load.
The ‘tool is the wire that makes a 0.2mm cut. The cutting path is obtained directly from the drawing in DXF format.
But the ‘aspect that makes it “revolutionary” is that this machining was performed in a small company, in which there could hardly have been wire erosion !!!
At G.E.S. in a little over a five-year period 3 Ecut machines have been installed, and the range of machining to their customers has been expanded.
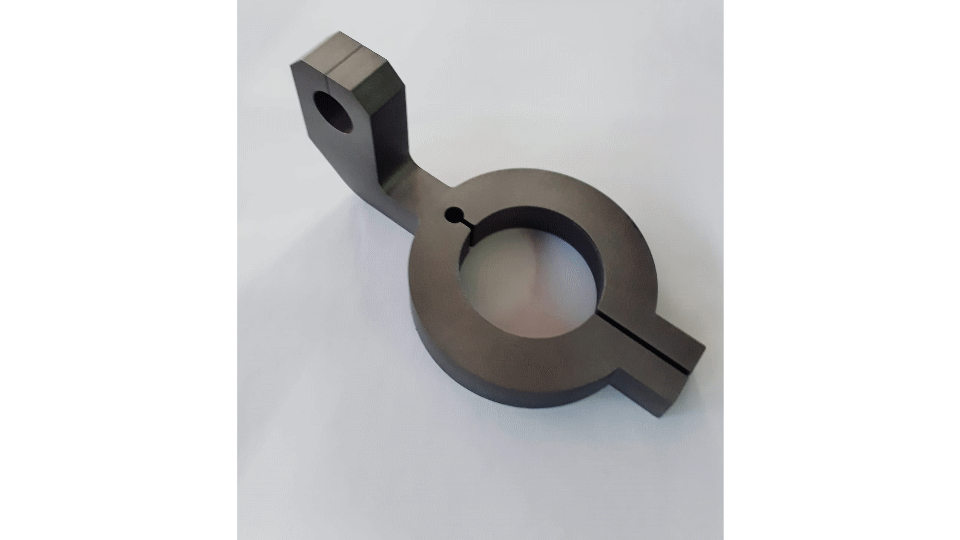
Cutting, or a profiled cut of pipes or profiles is uneconomical with conventional wire erosions.
The problems are :
– Wire breakage due to uneven washing/cooling.
– Size limitation due to tank processing.
– Limitation of bar feed equipment due to tank machining.
– Limited cutting height with “normal” machines.
With the E.cut™ system these limitations do not exist.
– Processing does not take place in the tank.
– Wire washing/cooling is drop-in.
– Already from the smallest Ecut the cutting height is 500mm, and can be up to 800mm
– The lack of a tank makes it possible to prepare systems for bar feed.
The cut is without burrs, not altering the characteristics of the material.
Pipe fixing is “gentle” and does not cause deformation.
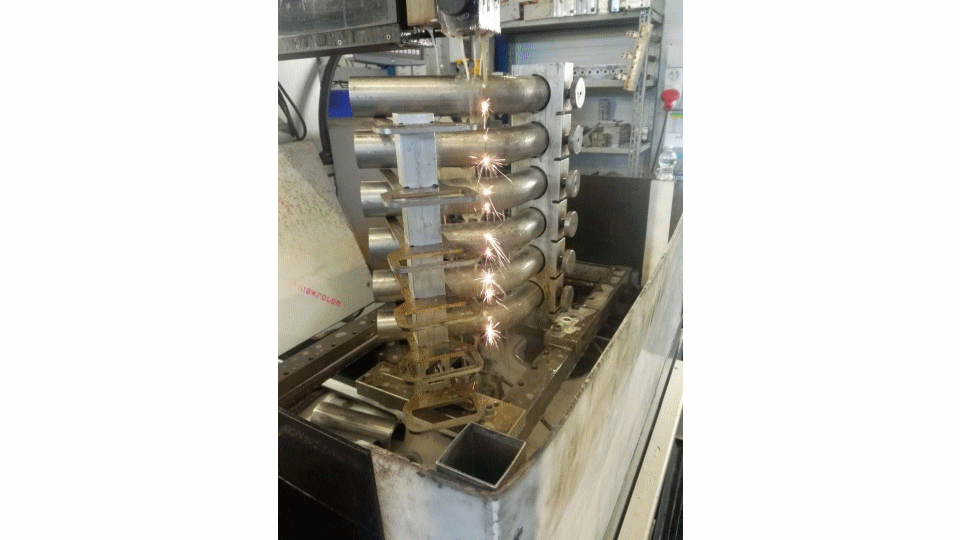
The simplicity of construction makes it possible to prepare large machines with working ranges practically impossible with conventional wire erosion.
Working strokes of up to 2000mm x 1200mm with cutting heights of up to 800mm and workpiece capacities of up to 6000 kg make wire erosion machining possible on large workpieces, with considerable economic advantages.
A modest cost favors its ‘use for machining operations hitherto unimaginable with wire erosion.
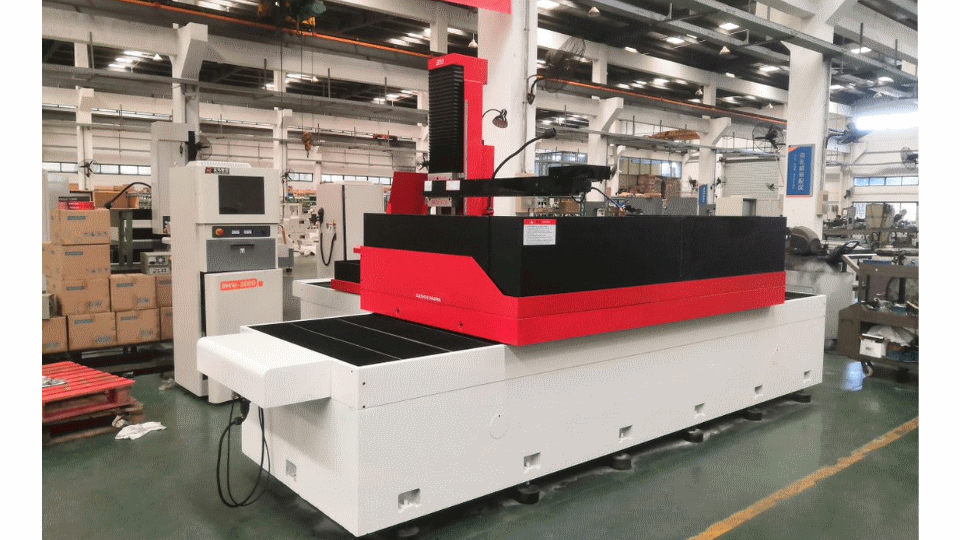
.
E.cut ™ is just Genesis, if it’s not E.cut ™ it’s not the same !
E.cut™ at Kilometer Zero – From fairs, exhibition, end of rental –
Ask if your E.cut ™ is there.