Cost counts
The toothed profile on these tubes, (instruments for anthroscopy), has a derisory cost.
The calculation sheet shows the cost to the end customer as a fraction of a euro. The times and cost indicated are for the cutting of 17 overlapping pieces, so the values must be divided by 17, at a very low removal speed, to obtain a better surface roughness.
The overlapping of 17 pieces is random and due to the height of the clamp jaws. The clamp is a standard clamp, not made of stainless steel. It is not immersed, and the washing liquid, emulsion with normal water, is anti-rust.
The low cost of cutting with Ecut allows the use of wire erosion technology.
The precision, within 0.015 mm, the very low roughness and the absolute absence of burrs are the ideal solution for cutting these teeth.
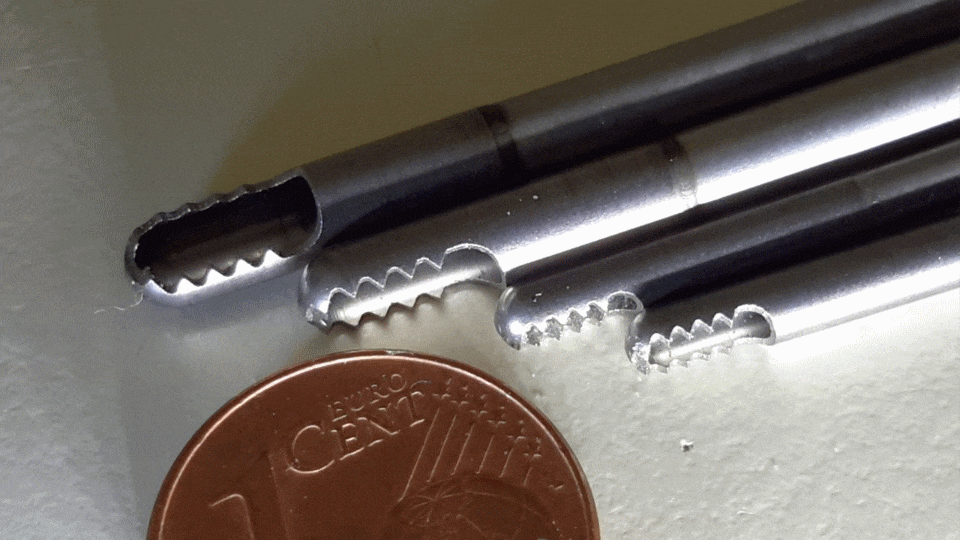
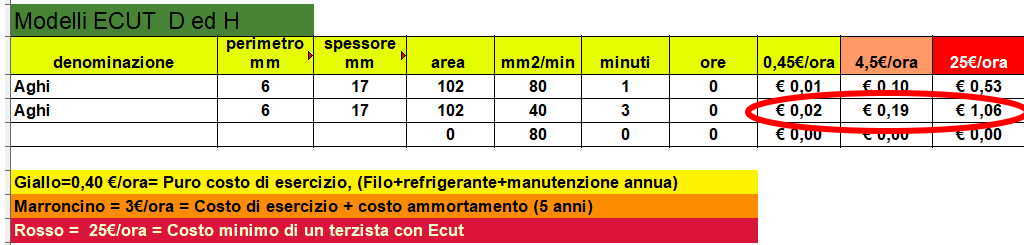
The execution of this aluminium heatsink could also be carried out by mechanical machining, but there are several critical points.
The path of wire erosion is therefore the only choice. The difference between a conventional wire erosion and an Ecut™ is the cost per piece. In the case of a single piece the difference, a cost from 8 to 15 times higher, can also be ignored, but for a series of pieces, the total difference becomes very relevant.
If you have a subcontractor who owns an Ecut™ do the work, the savings, even on just a dozen pieces, would be significant, but if you own an Ecut™ the difference in cost becomes very important!
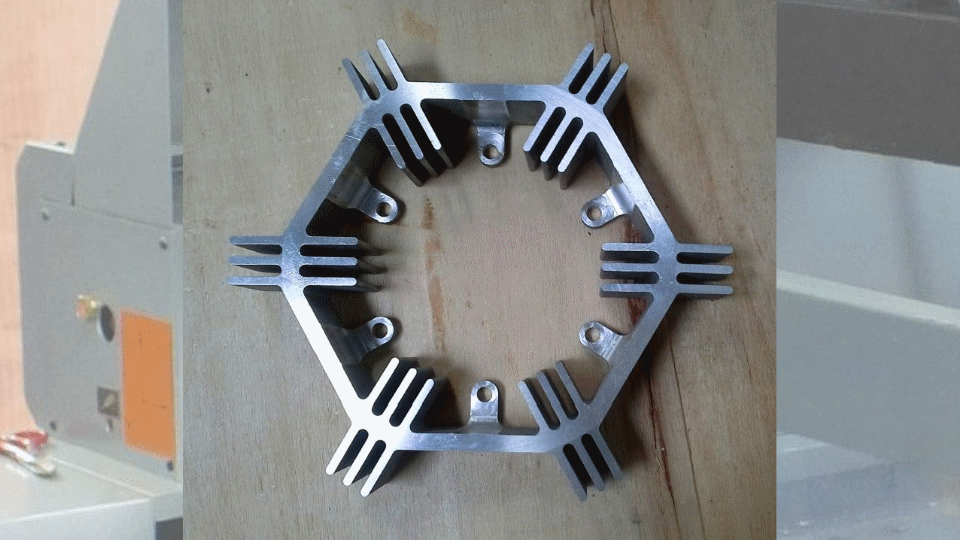
In the case of large diameter sprockets the division into sectors is quite common. In the case shown in the figure, the equipment adopted for normal wire erosion already available has been used.
With an Ecut™ it would have been possible to cut double arc sectors and overlap more pieces than those shown in the picture.
Already the smallest Ecut™ has strokes of 400mm x 320mm with a cutting height of 500mm. Moreover, the Ecut™ technology with a wire sliding speed 100 times higher than conventional wire erosion is not affected by the barrel effect, so it is possible to superimpose more pieces, in the picture there are only 2 pieces, one on top of the other, having the same identical size for all, without any reworking.
In the calculation sheet the values are for the cutting of 2 pieces of 20mm thickness, so times and costs for each rack must be divided by 2.
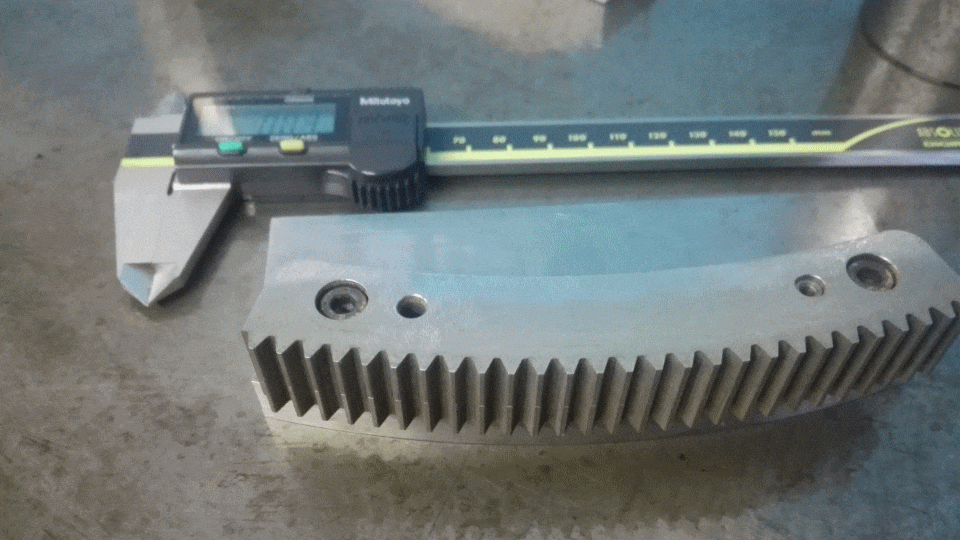
Keyless and broaching seats on large pieces. Slotting or wire erosion ?
Both !!
For small and medium sized pieces, and quantities of a certain size, the Slotting Machine is the compulsory choice. The costs of the tools are amortized in quantity.
When, on the other hand, the quantity is limited, often the single piece, the adoption of wire erosion becomes the most rational.
The reasons:
– Virtually no tool cost
– Simplicity of preparation and processing
– Accuracy within +/- 0.0075 mm on any height
– Machining of parts after heat treatment
With conventional wire erosion these advantages collide with the high hourly cost, especially if large machines are required.
With Ecut™ the operating cost is up to 20 times lower, making its use extremely advantageous.
Even with the smallest Ecut™ machines you can cut up to 500mm thickness, and with the biggest ones you can cut up to 800mm and have capacities up to 5000kg.
Spreadsheet times and costs are reduced in speed to achieve a good finish.
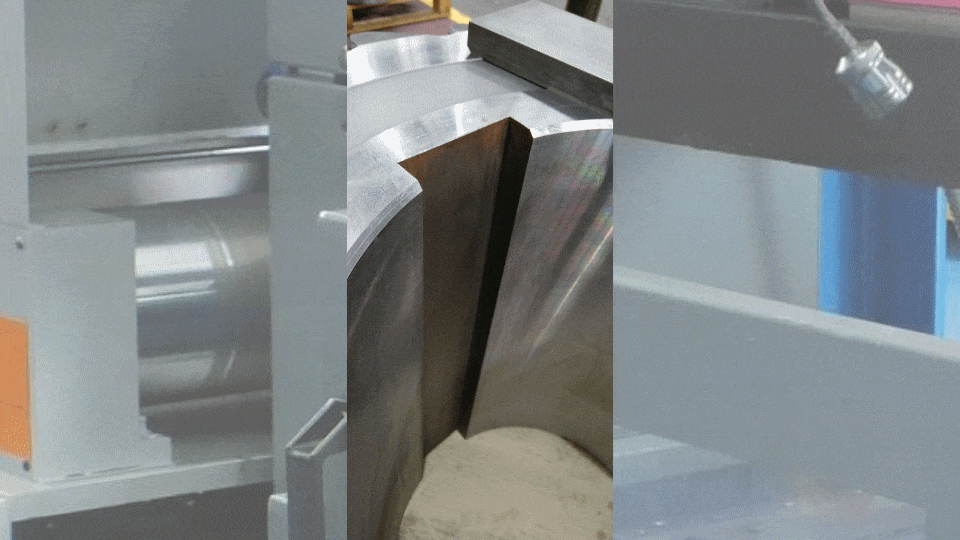
The piece in the picture is a classic example.
The stock removal machining presents some problems:
– the culisse is small in size and requires a special tool.
– The inclinations of the two sides of the culisse are different, so two special tools !
– The cut is very narrow and deep
– The final precision required is compromised by the cutting process.
The person who made the parts, a small company that carries out third party machining and owns two Ecut™, cut the indicated part after the heat treatment, obtaining optimal precision and finish.
The modification of many working cycles through the adoption of Ecut™ has brought great advantages. Advantages in terms of cost of parts, and therefore acquisition of new orders… and new customers
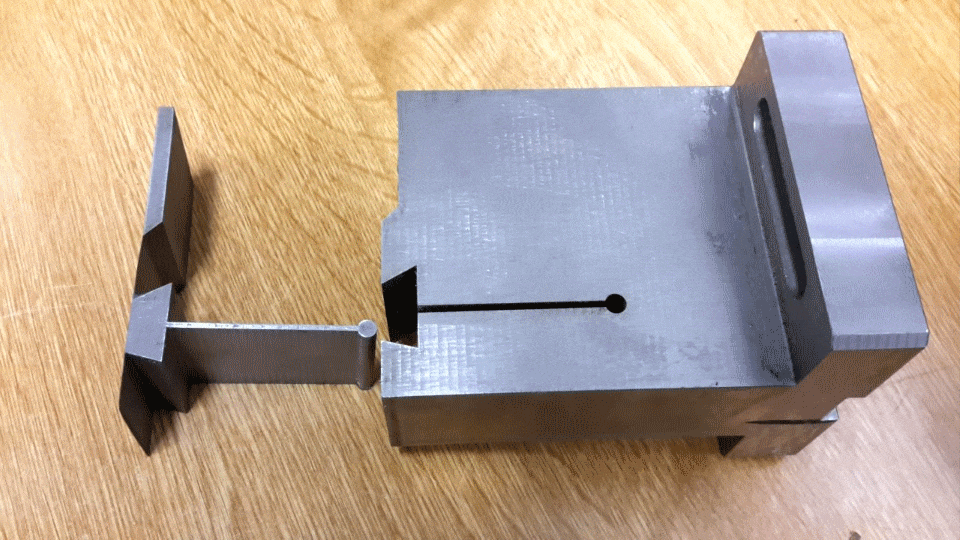
E.cut ™ is only Genesi ! Not E.cut ™ ? Not the same !