Increase yield
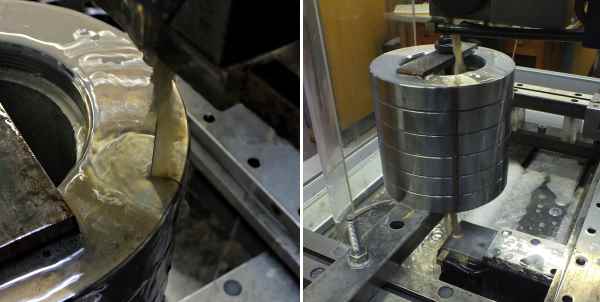
The four notches of these six large special hard steel ferrules, (45Hrc), were obtained without any fastening equipment, without any special hob or cutter, in one fell swoop. They cost about 20 times less than with normal wire erosion. An incomparably lower cost than normal milling.
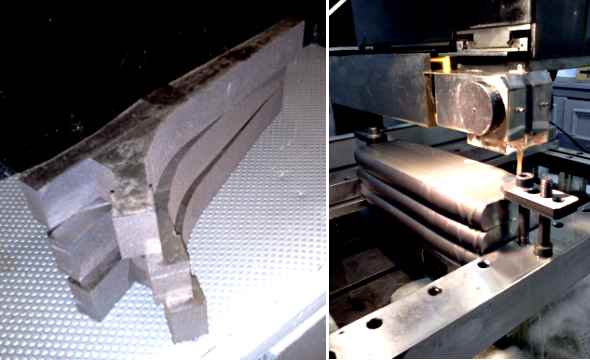
Titanium’s a bad beast to cut. The best thing is to get as close as possible to the final measurement with erosion, and so it’s done. But here an E.cut is used. The 12 hours of work to cut these pieces, of pure cost are worth 6 euros with E.cut, at least 120 euros with a normal wire erosion. The precious, and expensive, wire erosion is better to stay still, or maybe do jobs that make it pay for what it costs!
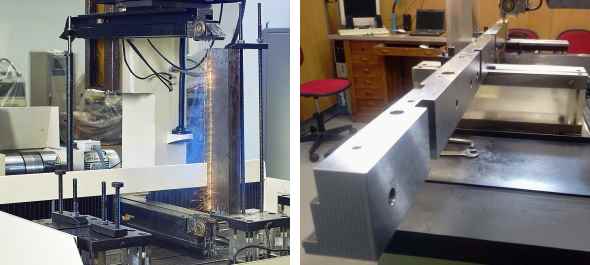
Of course, it doesn’t happen every day that you have to work on such high or such long pieces. But when it happens, or you go out, with costs and expectations that everyone knows, or if you have machines so ‘capable, you do not look at what it costs. The smallest E.cut cut cuts a thickness of 300 mm, and an average machine has strokes of 800×630 mm, with capacities up to 3000 kg.
With a cost ranging from 30,000 to 50,000 euros, with the possibility ‘to rent a car in advance zero, for 60 months, and blackmail 1%, an E.cut and’ a minimum investment to make it more’ your machines!