Wire erosion NO, E.cut YES
Wire erosion is a useful technology in any metalworking business. The limit to its general use is given by the price and hourly cost of operation.
A cost of over 100,000 euros is normal for a machine that cuts up to 150mm. The hourly cost, between brass wire, demineralized water, resins, filters, and maintenance exceeds 10 euros per hour, which added to the amortization brings the hourly cost to 20/25 euros per hour.
Often there are no hours of wire erosion that justify the purchase. So it is done by third parties. Asking please, waiting, suffering,… and paying!
Sometimes you choose the used car, and often it’s another bloodbath. Obsolete technologies with very high costs are recycled hiding behind incredibly low used prices.
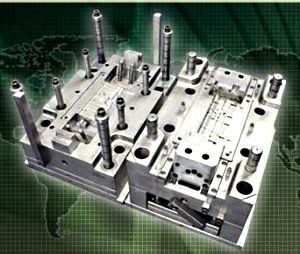
But at the same price you can buy an E.cut!
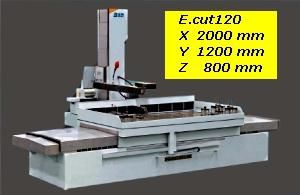
Thanks to an ultra-modern technology that takes full advantage of the possibilities of electronics, wire erosion becomes easy, and incredibly economical.
The basic idea is the use, indeed the reuse, of the same wire. The drum on which a spiral of molybdenum steel wire is wound and unwinds, allows a speed of sliding of the same 100 times higher than that of a normal erosion. The result is that there is no need to work with a submerged tank, no need for high pressure jets or sophisticated wire tensioning and retention systems. In concrete, a simple and rational structure, and… very important, of enormously lower cost.
The most Ecut bushes cut a thickness of 300 mm, and the largest ones reach 800 mm. And with a perfectly straight cut, without any barrel effect. The lack of a tank greatly simplifies the clamping. The processing is visible and always controllable.
The new BMXP CNC uses an industrial PC with XP operating system. The power of the whole guarantees a high control of the machining, and prevents the breakage of the wire. The company network, through a remote control program allows you to control and command the machine from the office, … or from home!
Ecut has a cost of operation + depreciation that does not exceed 3 euros per hour. That’s why more and more printers are adopting it!
Not only as a first wire erosion, but also to flank expensive wire erosion, which today are made to perform simple machining at an extremely high cost.
The machining of a mould of this size is prohibitive with a conventional wire erosion. Ecut 120×200 has X 2000, Y 1200 and Z movements up to 1000, with a capacity of 6000 Kg.