E.cut, opportunities for third parties
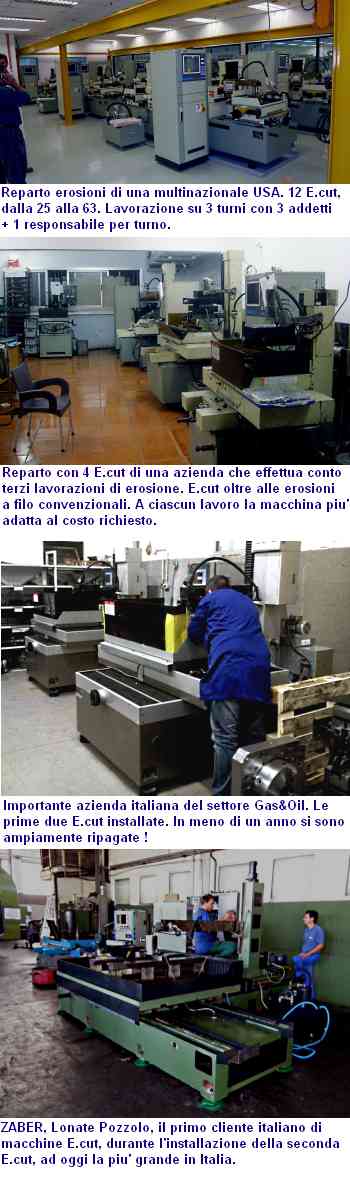
The use of E.cut™ expands at companies that carry out work on behalf of third parties.
In fact, they are the subcontractors, the most attentive to the possibilities that new technologies offer for the execution of parts obtained before milling, or cutting with laser or water.
In the field of conventional mechanical workshops, the adoption of wire erosion is not favourably seen, both for the high purchase cost and for the considerable operating cost.
The resulting hourly cost makes it too expensive and impossible to adopt, even when wire erosion technology would be the ideal solution for many processes.
( Without counting the difficulty of an uncommon technology outside the mould sector ).
E.cut™ technology, thanks to its simplicity, has very affordable purchase costs, from 3 to 10 times lower than similar machines.
The insignificant operating costs and more than 20 times lower, ( 0,40 €/hour against 10/15 €/hour of a conventional wire erosion ), open new horizons, and new opportunities.
Both for the customer and for the contractor who fully understands how it works.
The cutting characteristics of E.cut™ are exalted when there are to be cut materials that are difficult to machine (stainless steel, Inconel, high strength steels, titanium, hard metal,..). No tools, no grinding wheels, no thrown wire, therefore practically no tool cost.
The first image is of an American company for its headquarters in the Far East. (There departments with 40 wire machines type E.cut are common).
The second image is of a company from Eastern Europe, a very important market for these machines.
But the last two are by Italian companies.
The last image is of a company that after only one year from the purchase of the first machine (you can see, blue, behind the one in the foreground), has bought a second one.