Only with Ecut
Some features make Ecut a different machine, and “new” in the field of mechanical processing.
1) the lack of immersion tank
2) the lack of the “barrel effect”
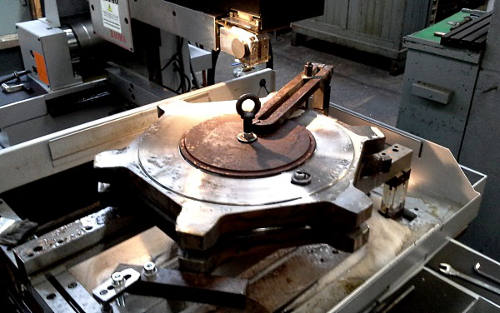
These large sprockets were made with one of the smallest Ecut, (40D). Although the machine strokes were not sufficient to execute the piece entirely, the lack of an immersion tank allowed with simple tricks to perform the work by rotating the pieces three times. The machined parts are not adjacent, there are about 20mm between one crown and another, and this makes it very difficult, if not impossible, the machining with a conventional wire erosion. With Ecut, no problem. The particularly difficult material, ( inconel ), is cut without any difficulty, and the cost is enormously lower compared to machining.
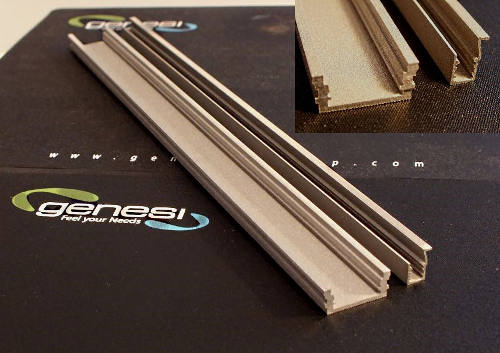
These parts are prototypes of a profile. The dimensions are 16×5 mm for one part, and 6×9 mm for the other. The length is 210 mm. Tolerances are +/- 0.02 mm. ONLY with Ecut it is possible to work like this ! The workpieces must be machined in a single pass. It is NOT possible to carry out rework, because such low thicknesses imply a deformation at the end of the first cut.
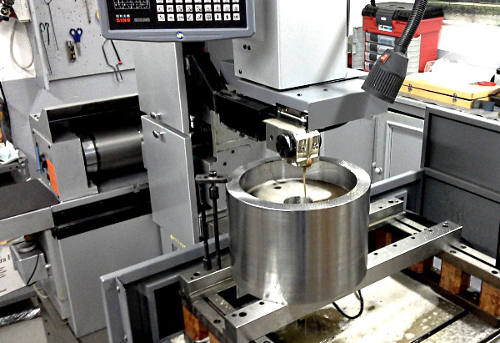
Running two simple flash drives wouldn’t seem to be a problem. But the piece is over 250mm high.
And this creates a problem!
Erosion machines that cut these thicknesses are starting to be particularly expensive, with a significant hourly cost, and those who own them certainly do not give the work!
The machine in the figure is the smallest in the Ecut range, it cuts 300 mm thick, with strokes of 400×320 mm.
The keys are obtained with a single cut, with a tolerance on the whole height within 2 cents.
NO MECHANICAL PROCESSING CAN PERFORM THESE PIECES AT THE SAME COST!
doubts ? CLICK HERE and request a machining quote