
Industry 4.0? There’s something new in the air today…
“The fourth industrial revolution is already underway and the so-called “smart manufacturing”, digital innovation in industrial processes, is the key to future competitiveness. It’s time to bring the Internet into the factories. That doesn’t mean allowing workers to use facebook or Whatsapp during working hours, but rethinking factories with digital. With “Industry 4.0” ( but we can call it Smart Factory, an intelligent factory…) indicates the set of digital technologies, tools for data and analysis that are found throughout the production chain: 3D printing, robotics, complete products with artificial intelligence, such as connected cars and other objects of the Internet of Things.
We are trying to understand….
…however, we put our machines on the net, we tele-assist them, we give them the possibility to command and manage them at a distance, even with a smartphone. We create and put manuals on board the machine that make them manageable even to unskilled personnel …. … we try to understand, and we start to adapt.
The ‘wire erosion we have known for many years, many more’ than almost all those who now sell wire erosion
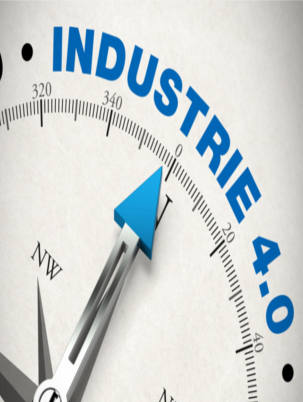
What is it?
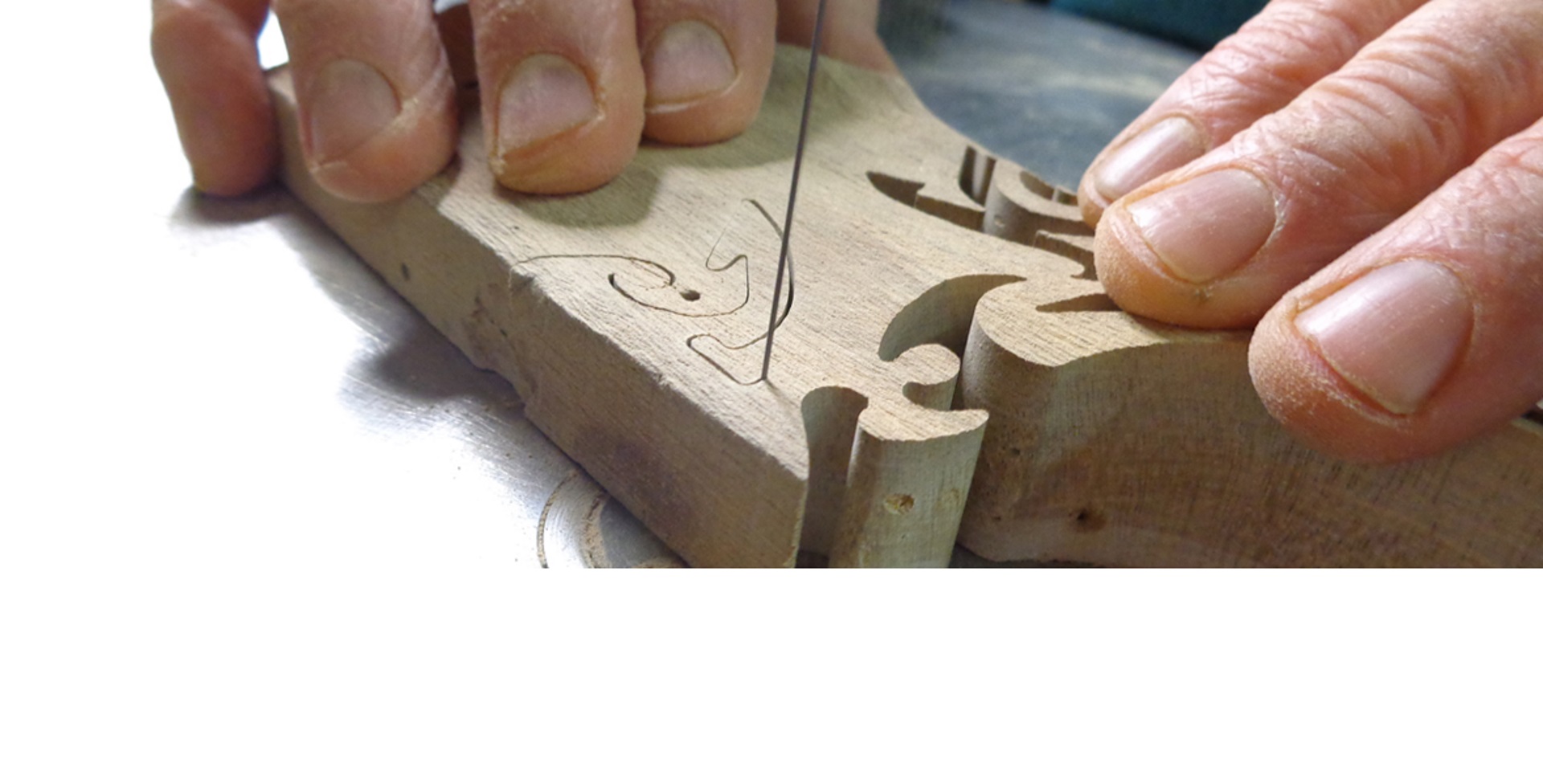
E.cut is a system for processing metallic materials. Like a fretwork, a molybdenum steel wire of a few cents (18, like three hairs!) cuts any metal material, of any hardness, up to a thickness of 800 mm. The precise and smooth 2-tenths cut is cold, and does not alter the state of the material.
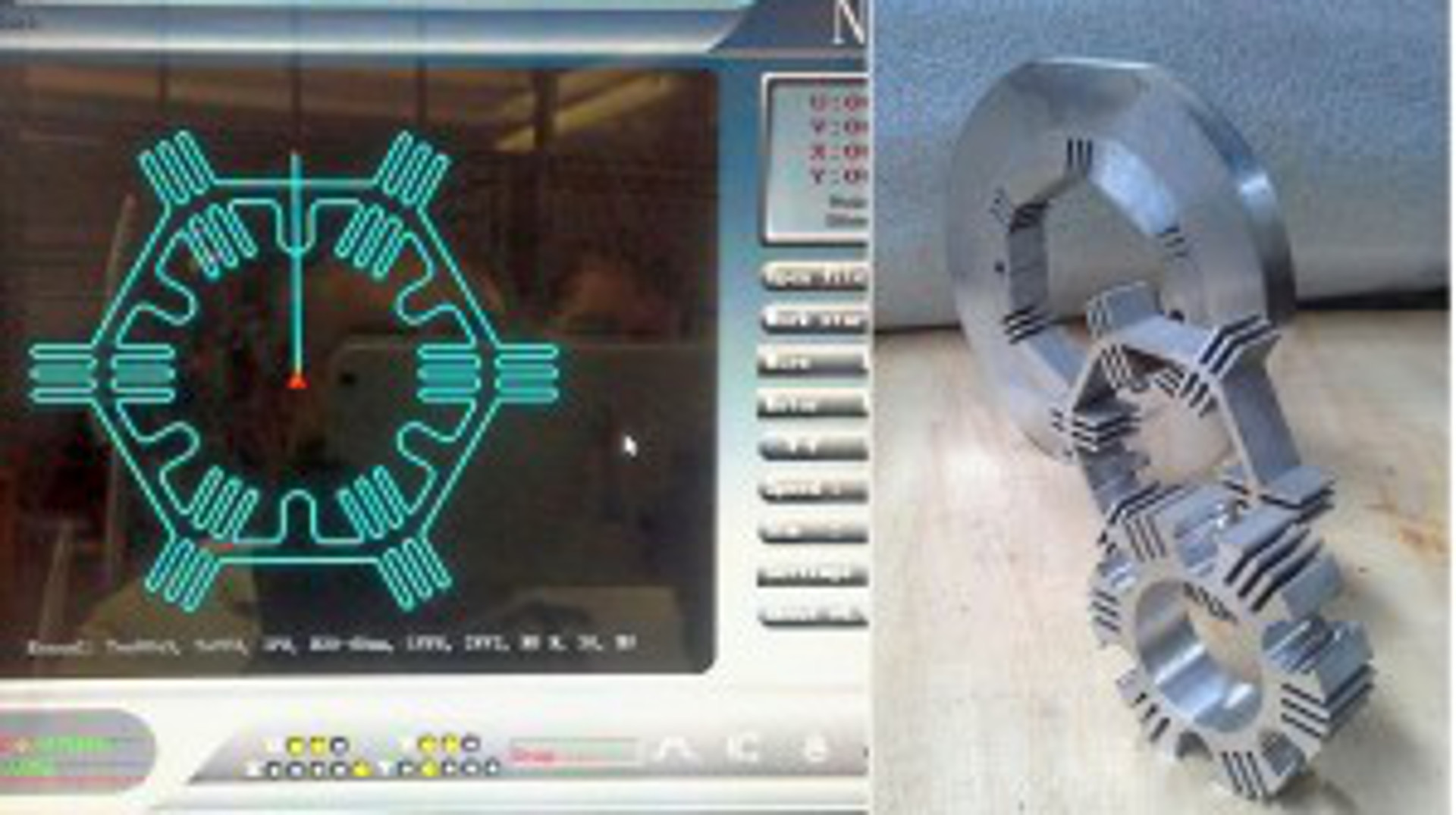
The numerical control that guides the wire allows simple cutting, as well as the execution of complex profiles, up to the cutting of gears. The combination of construction and technological features makes the cost of cutting incredibly low.
Exotic materials such as titanium, Inconel, tool steels, hard metal, hastalloy, stellite, copper, aluminium are cut, even in thicknesses up to 800 mm.
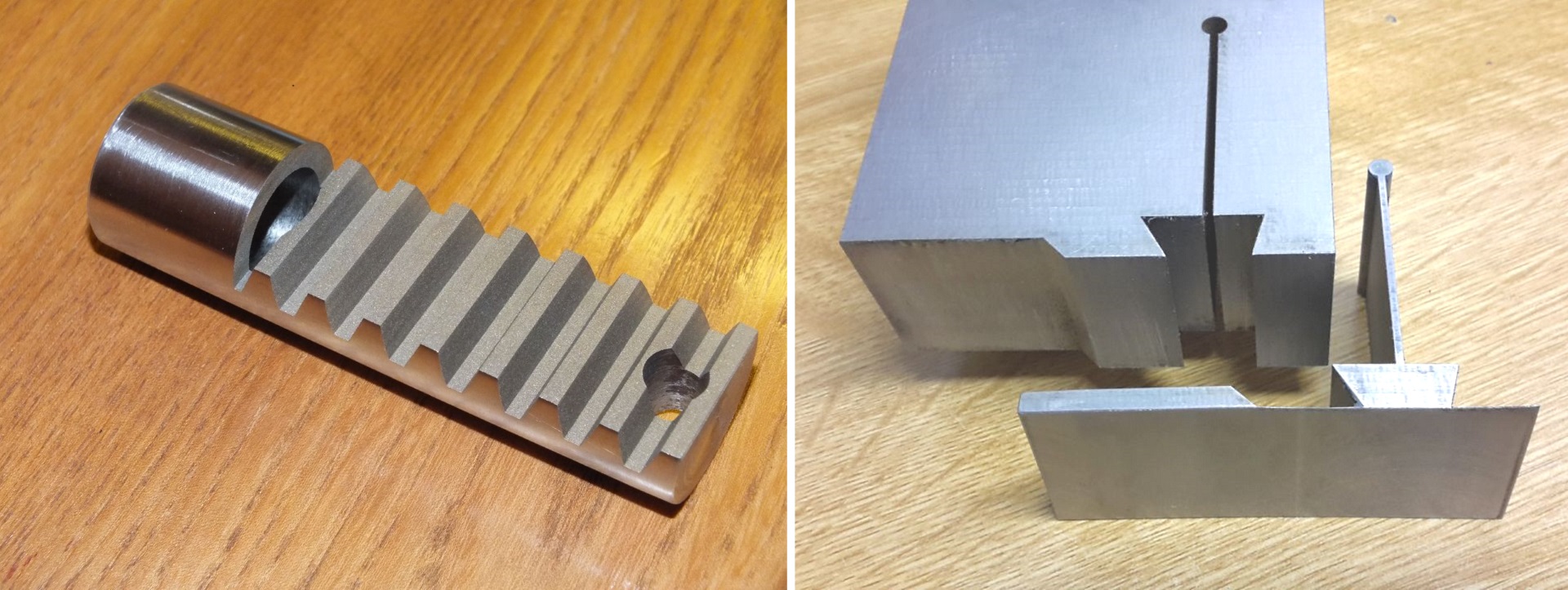
Complex work sequences can be advantageously eliminated by working directly on the finished dimensions of parts that have already been heat-treated, are of very high hardness (carbide), or are particularly difficult when machining by removing chips.
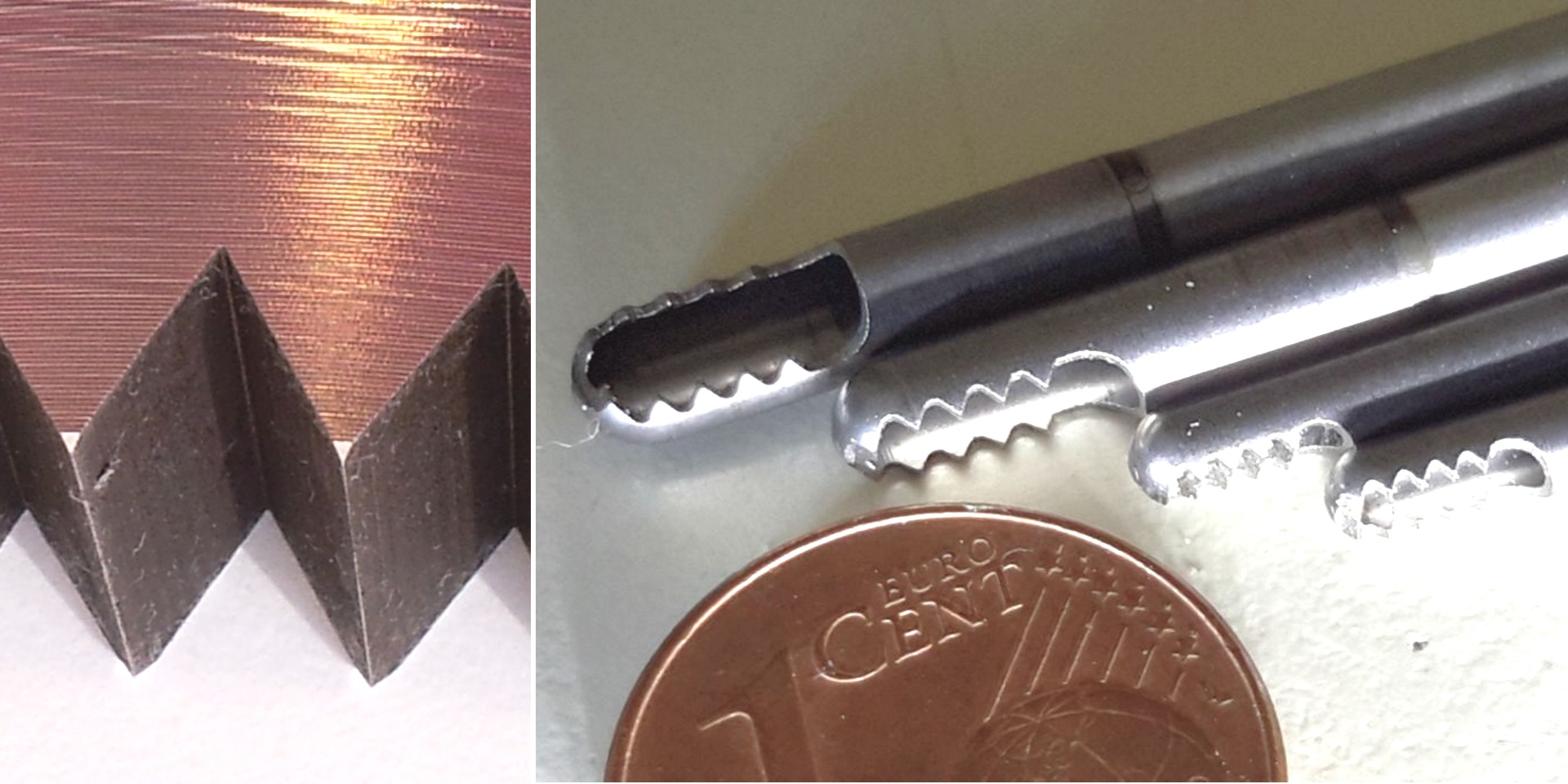
No burrs are generated, resulting in sharp edges, without any need for costly and difficult manual burrs.
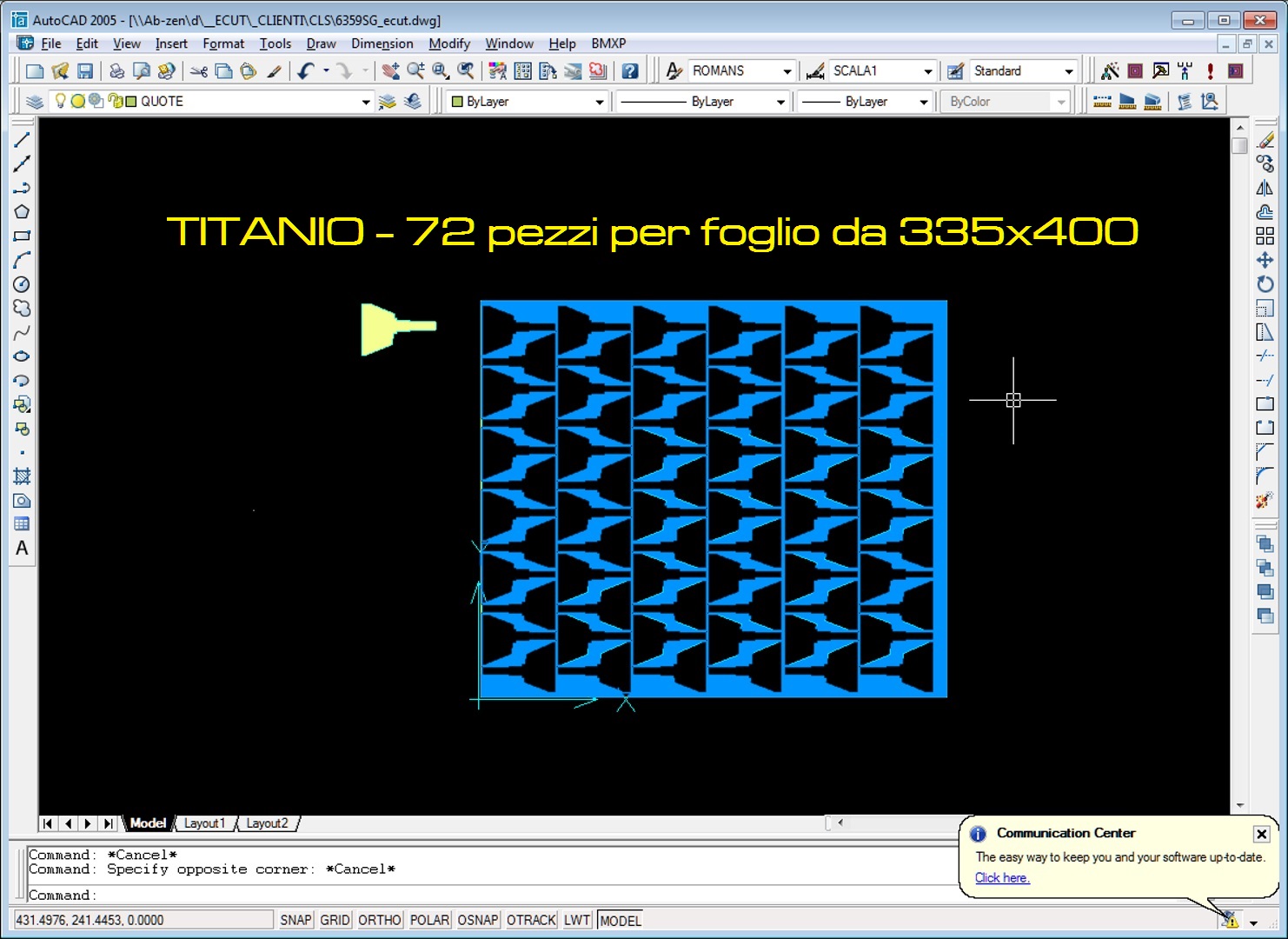
A careful arrangement of the profiles reduces the amount of waste (precious or expensive materials) to a minimum. Through the integrated CAD, the piece to be cut can be duplicated, rotated and arranged appropriately, and then generate the cutting path.
How is it
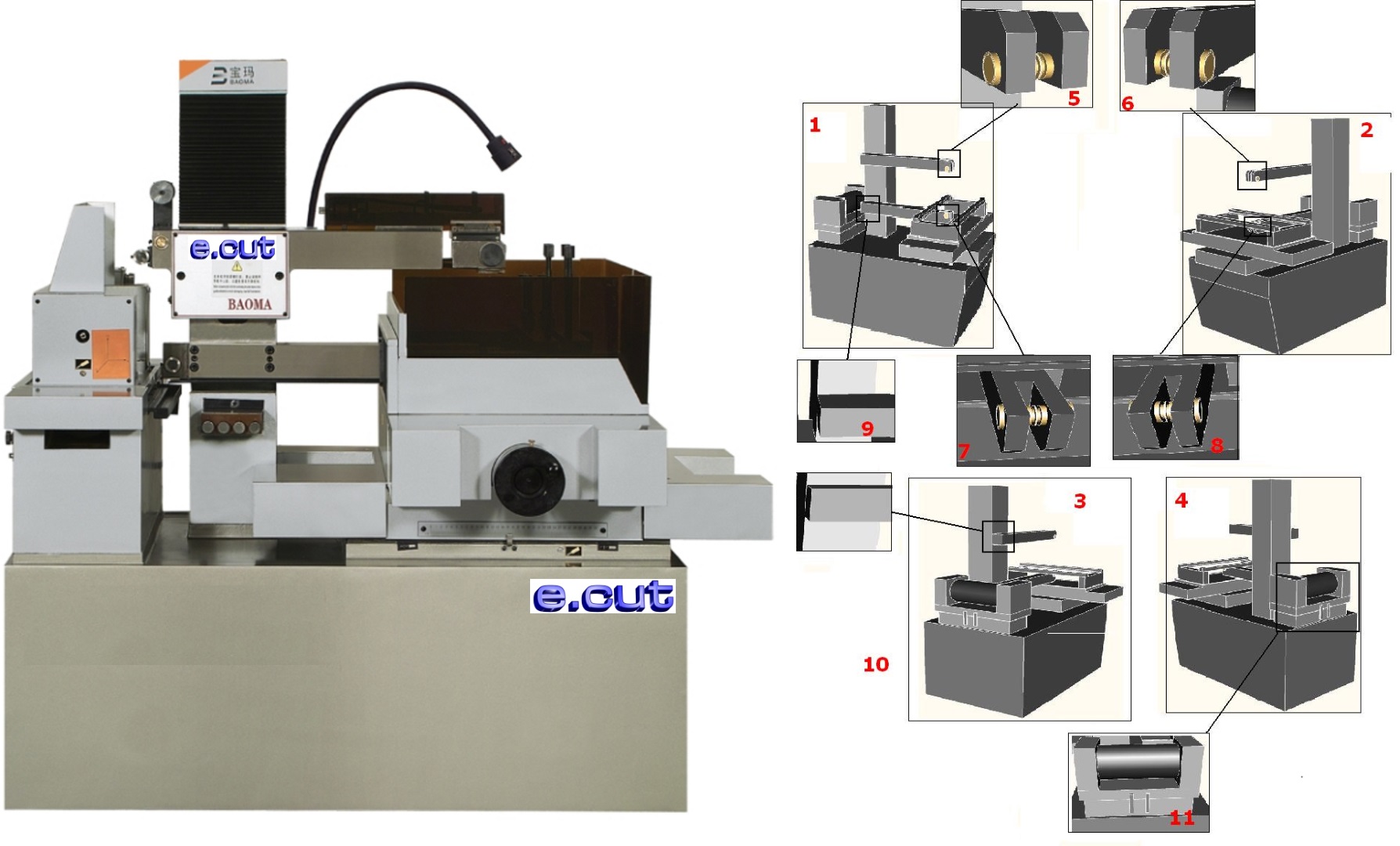
Base, cross table, upright with arms, wire reel drum.
Simple and rational construction, it is practically free of maintenance that goes beyond regular cleaning.
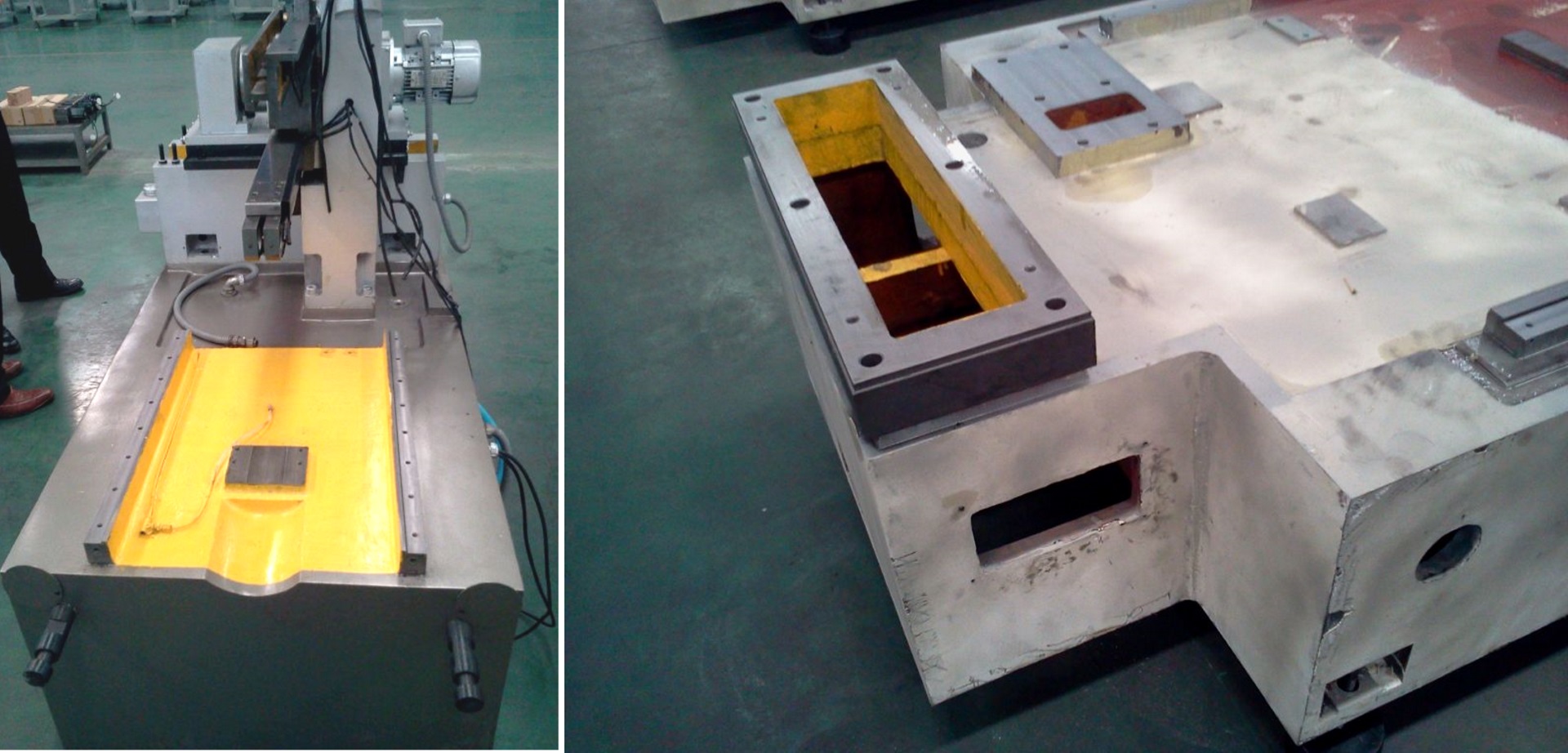
HT250 cast iron base, long seasoned.
Multiple treatments each time for optimum body relaxation before final assembly.
Great stability and guarantee of precision even after long years of work.
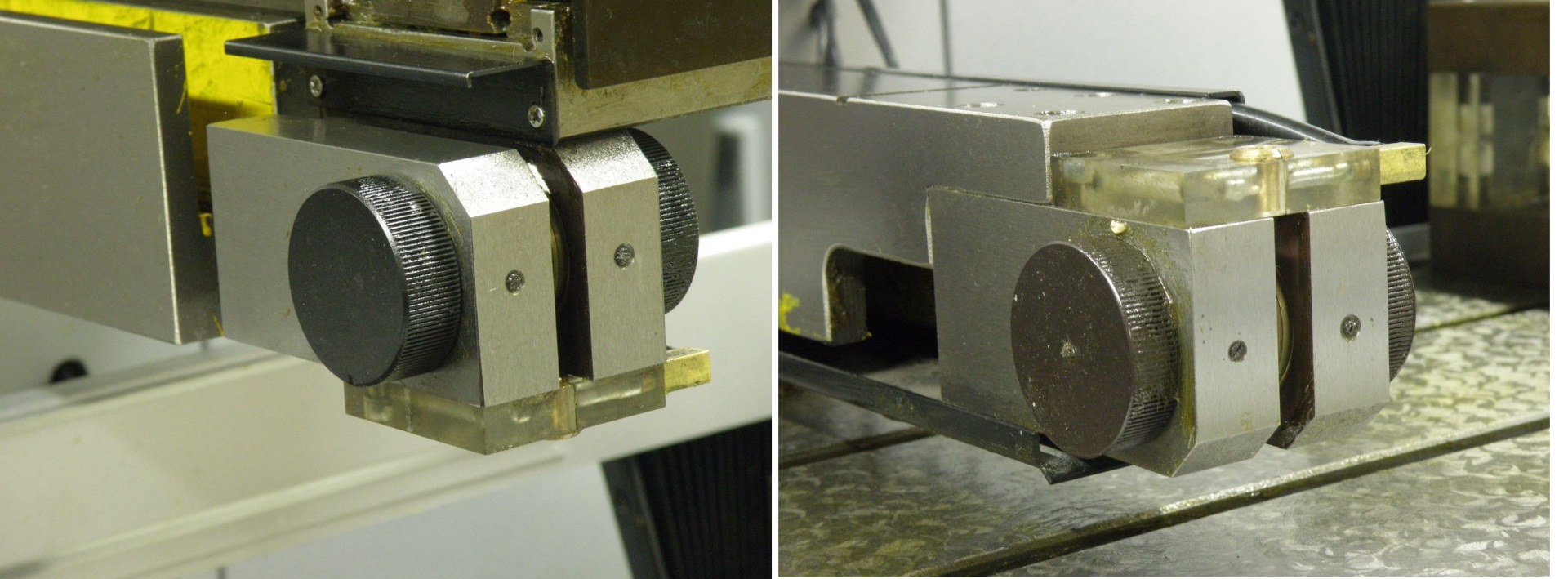
Wire guide roller heads with adjustment for vertical alignment and collimation on pieces not positioned orthogonal to the axis movement plane.
Upper head with U and V axes for tapering.
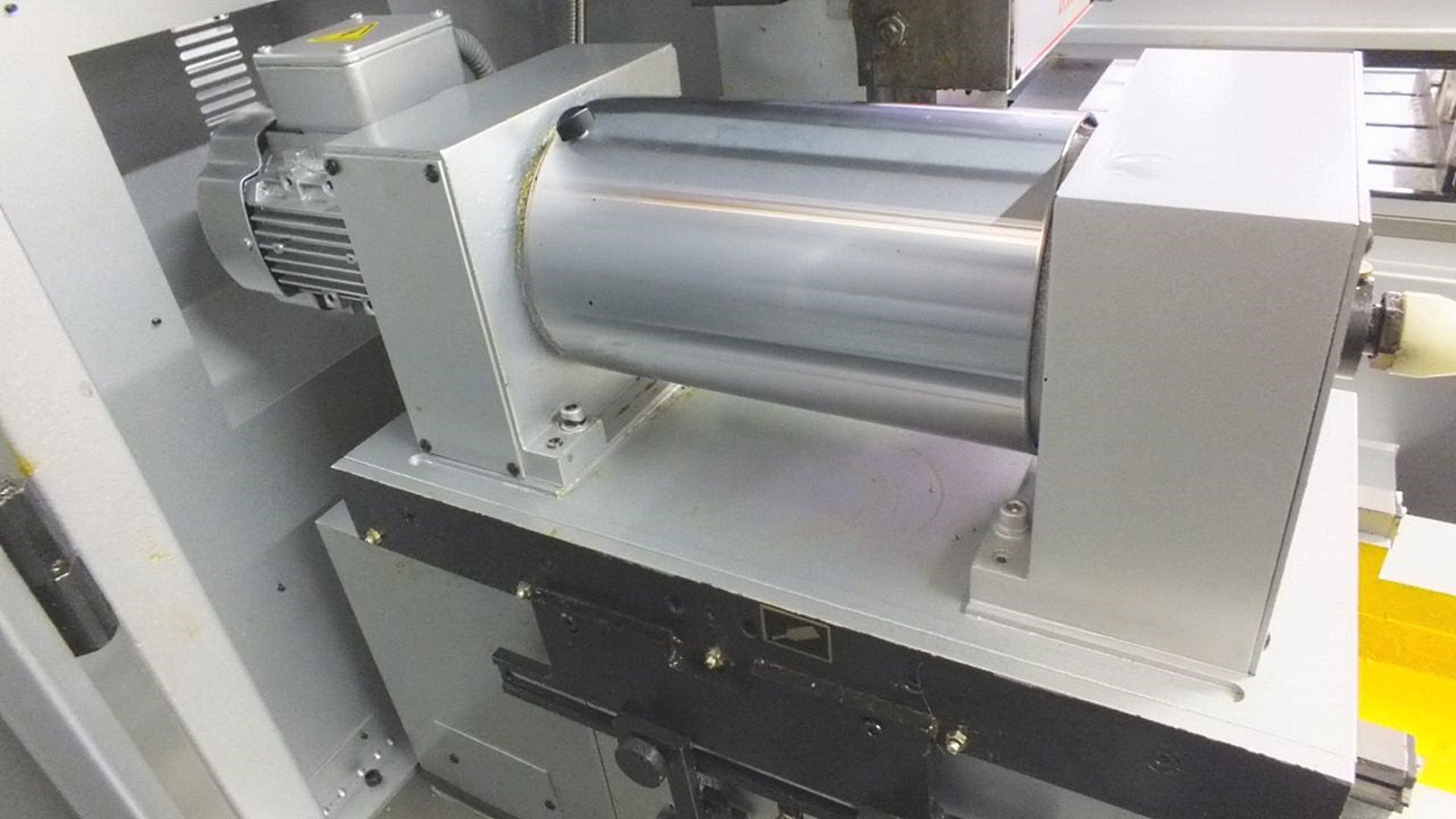
Wire rewinding drum with magnetic reversing limit switches.
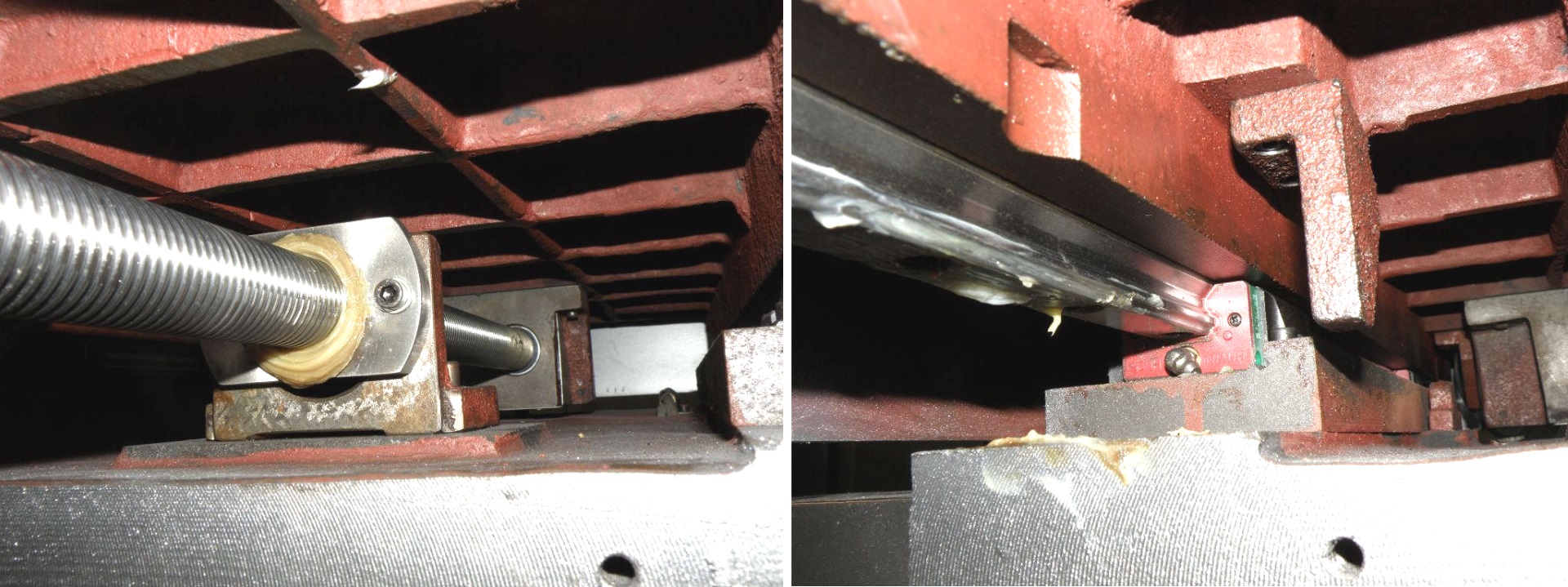
Oversized ball screws and steel guides with recirculating units.
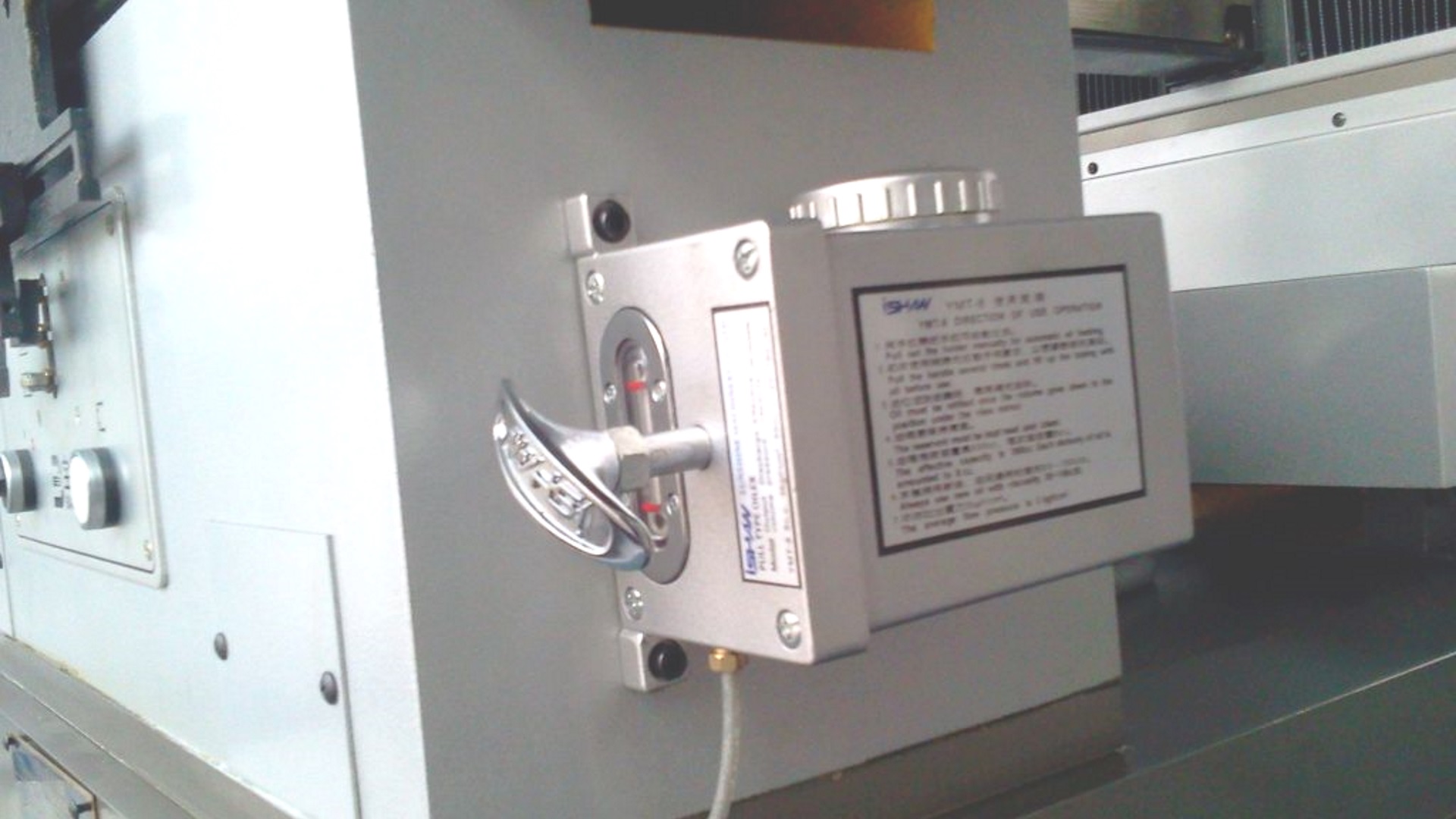
Centralized lubrication of all moving parts.
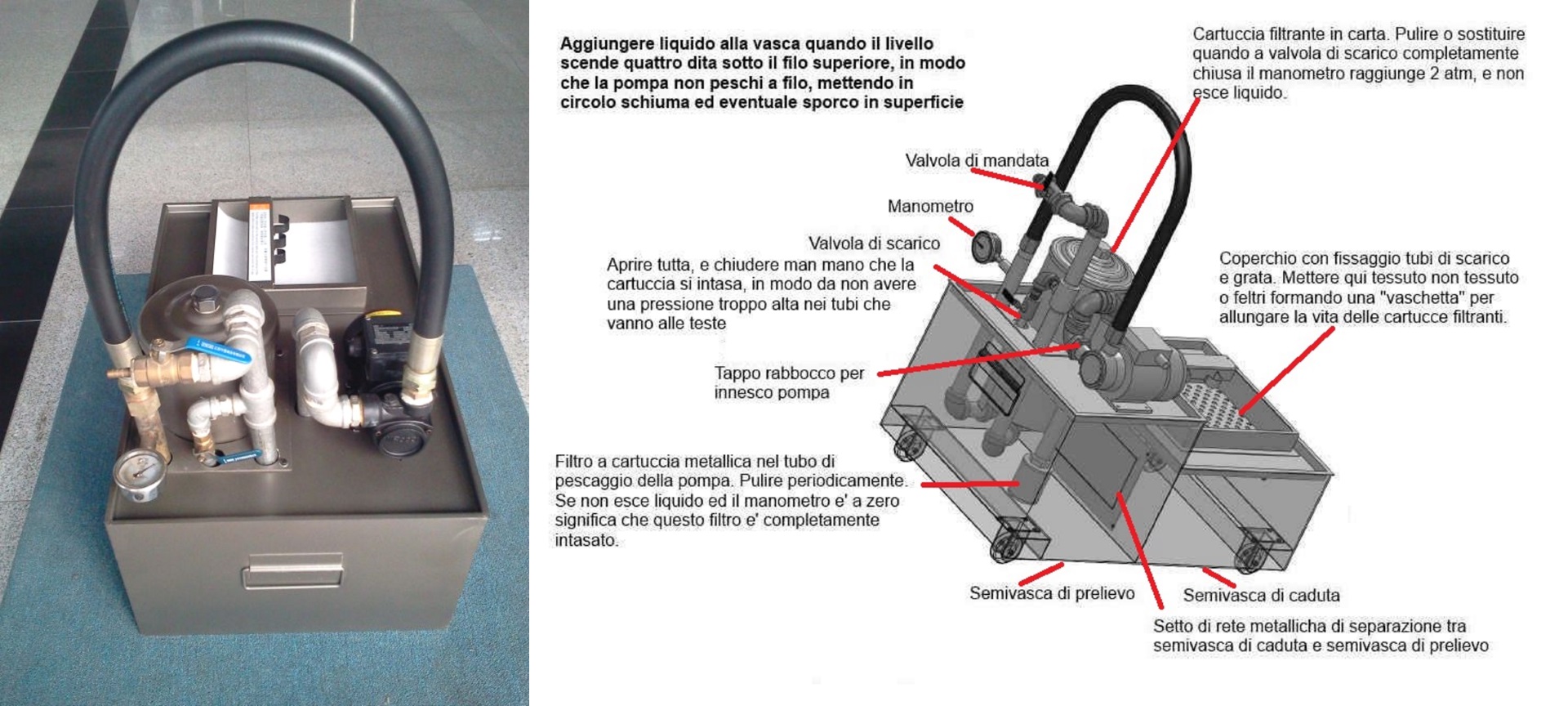
80 litre tank with multiple filter system.
Washing liquid obtained with natural water with the addition of gelatine with a completely vegetable base.
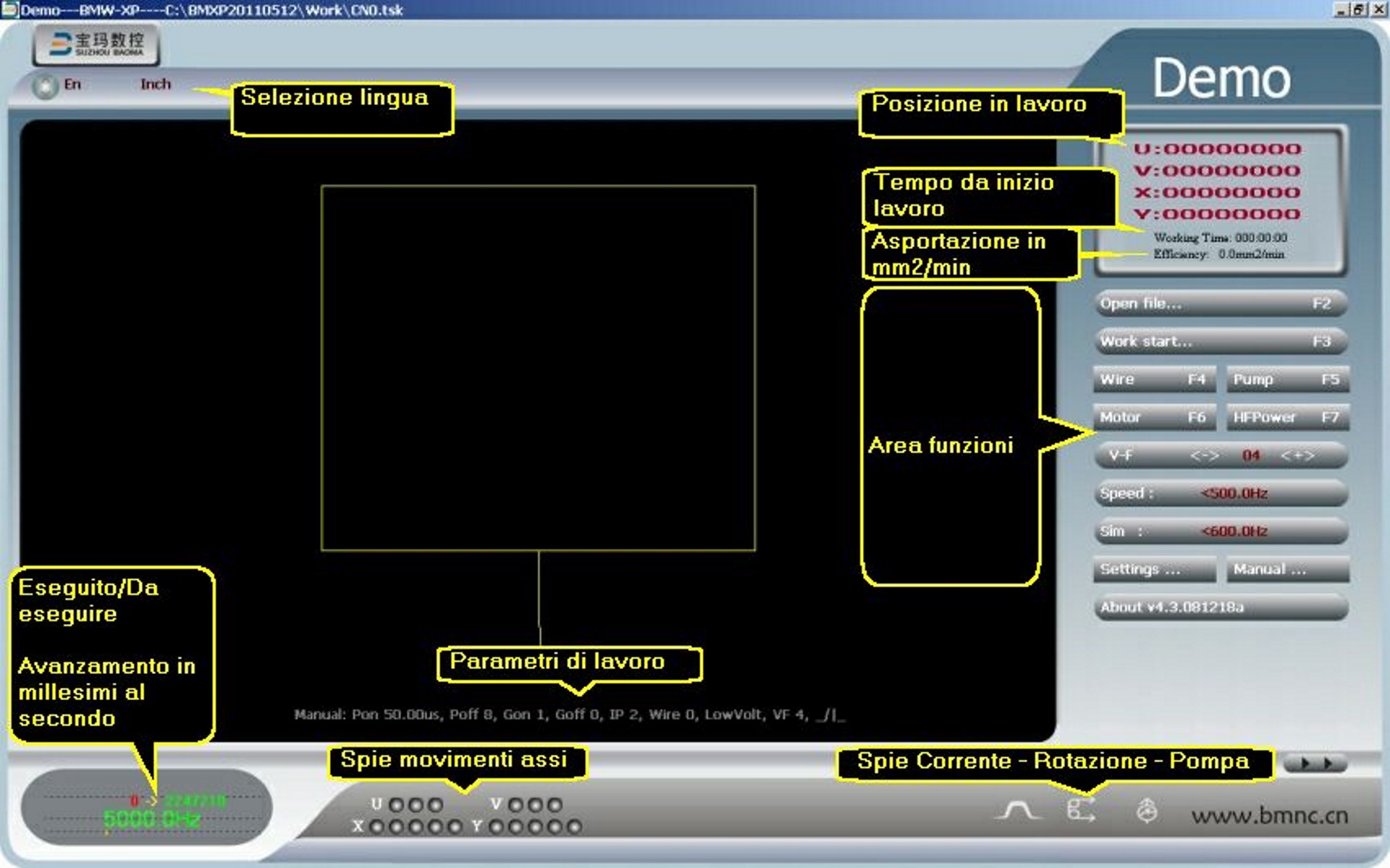
Numerical control (industrial PC with Windows 10 operating system) equipped with a program for managing the graphics, with the possibility of importing from standard DXF files.
It is possible to install a proprietary CAD system (Autocad…).
Control signals directly from PC, reducing by more than 70% the causes of malfunctions.
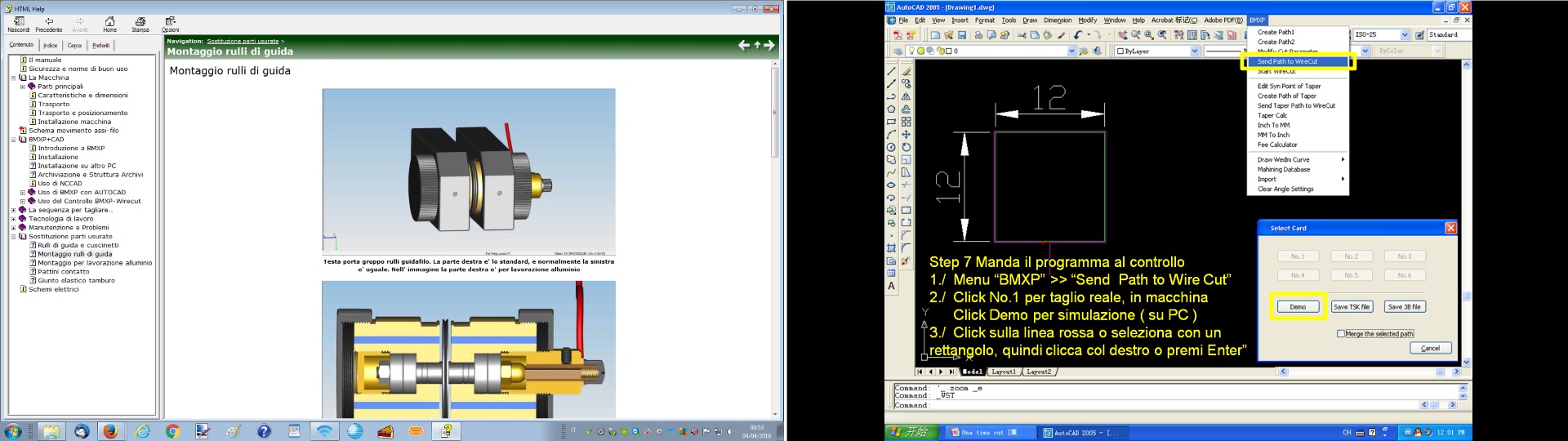
Manuals in Window Help and PDF format on board the machine for easy reference even while the machine is working. Wide use of images, diagrams and exploded views to make the consultation easy.
Sequences in Power Point format to illustrate the use of the various functions.
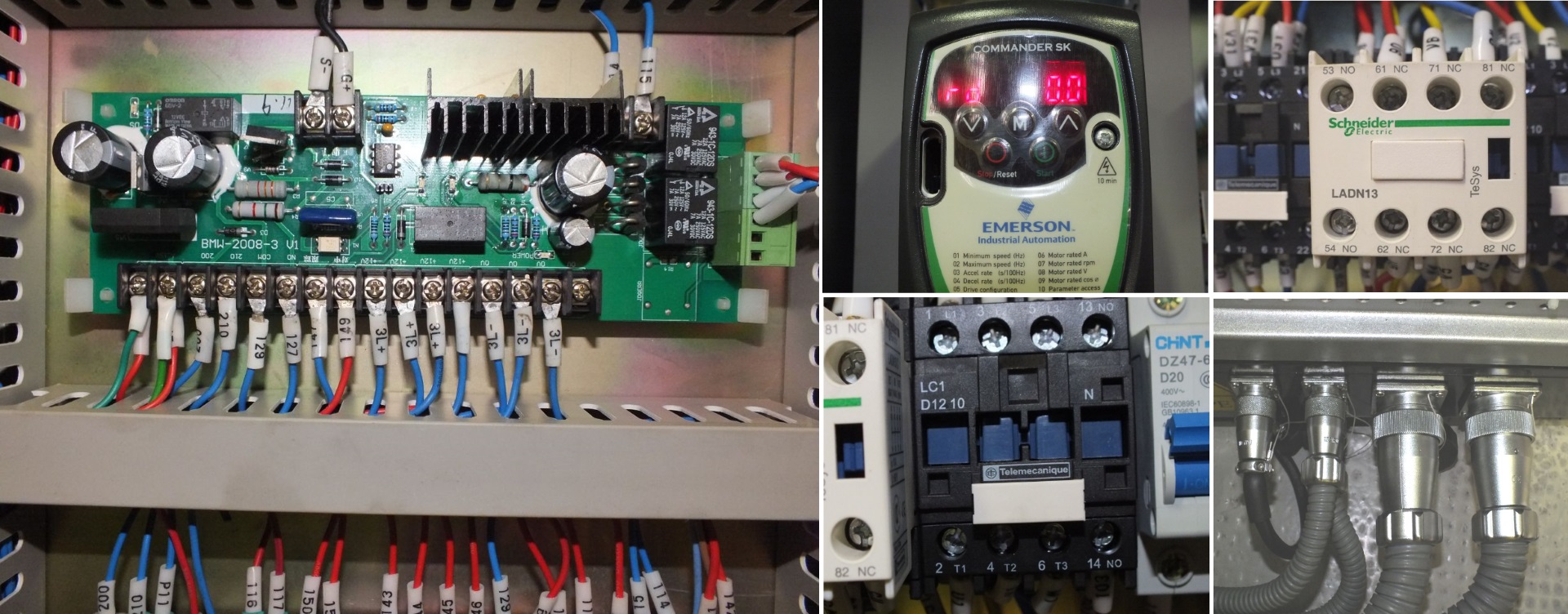
All electrical connections are screwed in (not welded!) for quick and easy replacement.
Components from primary industries worldwide, Inverter Emerson (USA), Schneider components (France), Electronic parts easy to find in the Italian market.
What it does
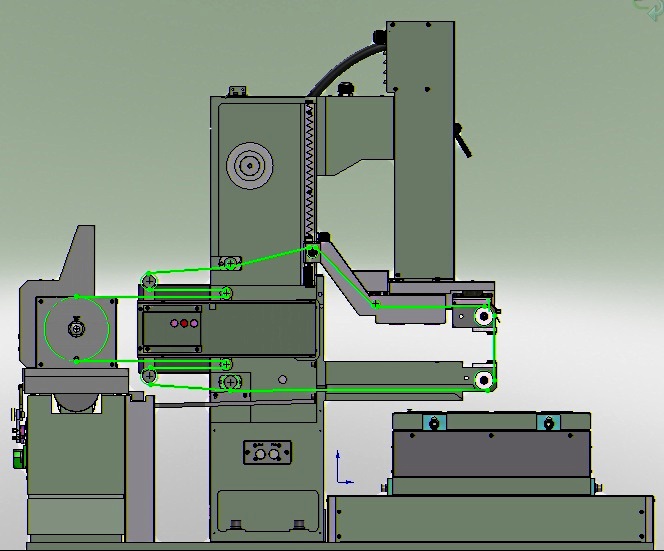
Ecut’s technology is that of wire EDM from which it differs for the higher speed of wire flow.
Instead of running at 8 meters per minute, with Ecut the wire runs almost 100 times faster, 720 meters per minute.
The influence of the liquid to control the temperature of the wire and evacuate the electrode particles becomes irrelevant.
The liquid is falling down, there is no immersion tank, and parts of pieces with dimensions exceeding the working table can be processed.
This is possible because the Ecut technology provides for the reuse of the wire that rewinds on a roller.
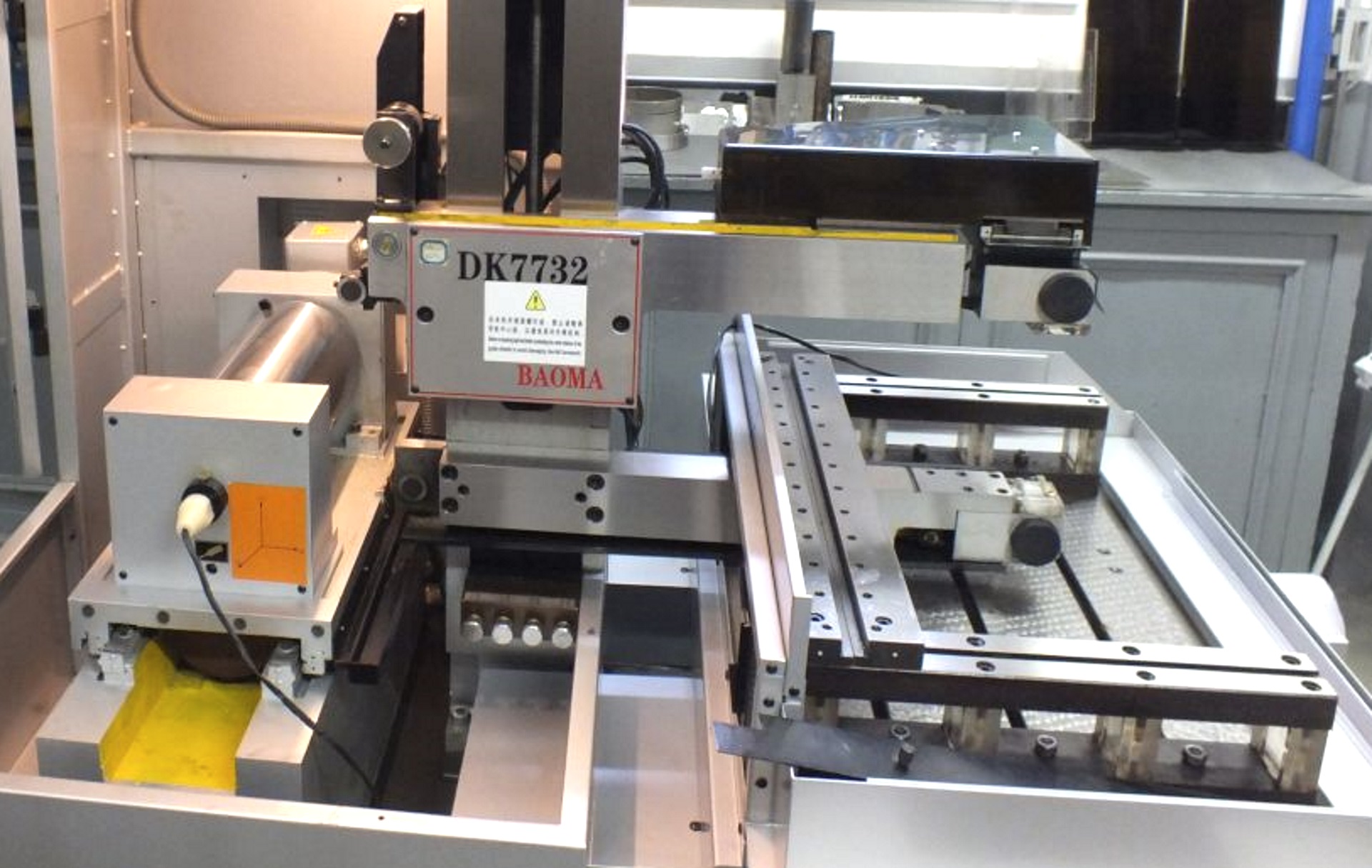
Due to the high running speed, some process conditions are substantially changed.
At 720 m/min the wire “escapes”, simplifying and making sophisticated and expensive technologies aimed at preventing breakage useless.
The wire does not have time to wear out, it lasts a long time before it wears out and only breaks due to incorrect manoeuvres.
Instead of disposable brass wire, a much stronger molybdenum alloy wire is used, the higher cost of which disappears due to its very long life.
How it works
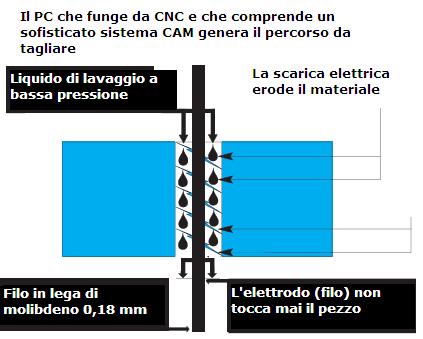
A 0.18 mm steel wire with a high molybdenum content accurately cuts metals of any hardness up to 1000 mm thickness.
The principle is exactly that, well known for over 50 years, of wire EDM, known as WEDM, Wire Electro Discharging Machine.
The fundamental difference is that the wire is continuously rewound and reused.
The simple intuition of winding and unwinding a wire spiral on an axially translational drum has practically revolutionized the original principle.
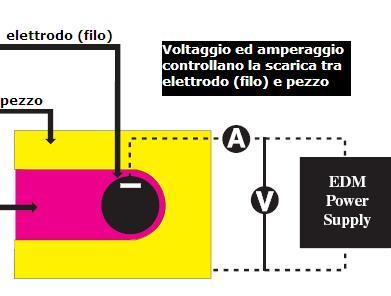
Some consequences of wire reuse have led to this revolution:
1) Not having to throw it away, you use a much stronger thread, although more expensive, having the benefit of being able to stretch it much more
2) The wire can be run much faster, (up to 700 mt/minute, against 7/8 meters per minute of the conventional method). As a result, the contact time between wire and workpiece is infinitely shorter, making washing and cooling much less important.
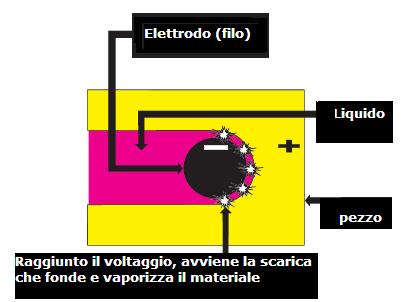
3) The high speed of the wire’s flow causes the wire to “clean” itself. Even at high thicknesses the whole cutting height has the same environment for the explosion of current discharges, then disappears the annoying barrel effect due to the presence in the central cutting area of material removed that alters the size of the discharge area.
4) The above conditions considerably limit surface microhardness and the onset of microcracks
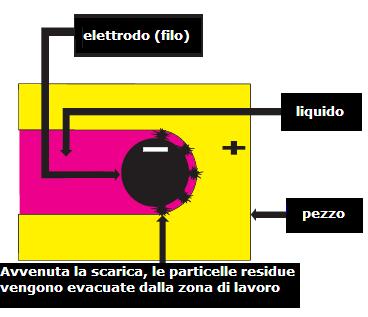
5) The use of a vegetable component that, emulsified with simple natural water, lowers the electrical conductivity of the same, eliminates the use of distilled water and ion exchange resins, almost completely canceling the cost of the washing liquid.
6) The washing pressure is “falling”, so it does not need the immersion tank. Machining can also be carried out on very large pieces compared to the dimensions of the machine tables.
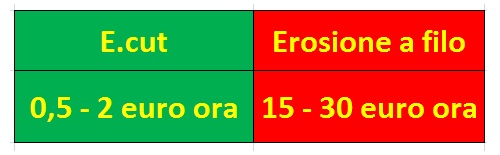
The hourly operating cost of standard models does not exceed 0.5 €/hour, and for C Type models 2 €/hour. It is very low, 10 to 20 times lower than similar processes, and makes it one of the most economical systems for cutting metals.
When to use it
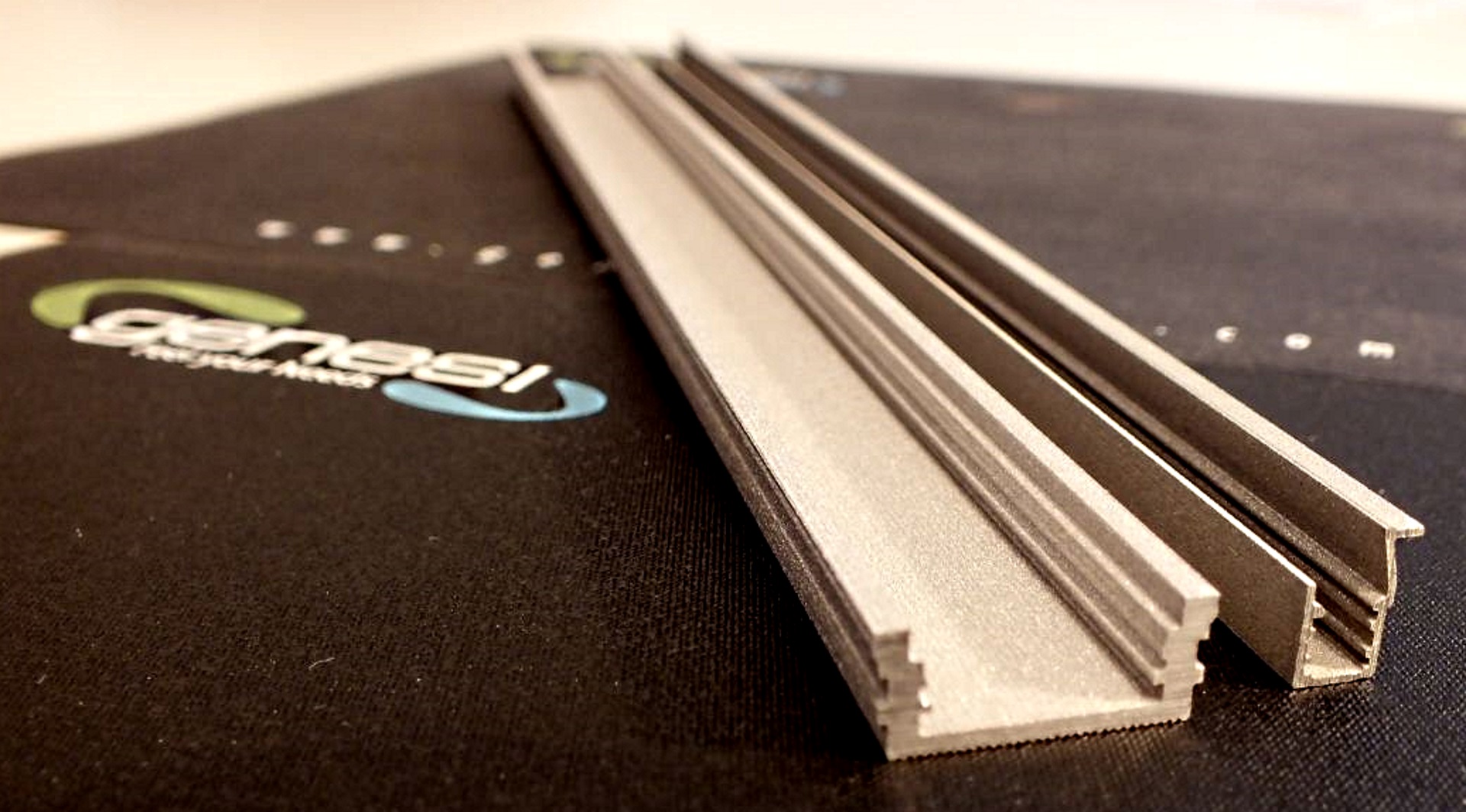
Even without reaching pieces like the one in the figure (prototype of the profile, the height exceeds 500 mm), many similar processes could not be carried out except at very high costs.
The development of wire erosion has upset many processes and, more importantly, allowed the execution of parts that were previously almost impossible, albeit at a very high cost.
At its birth, the high costs led to the search for maximum precision and the best surface finish, necessary for the machining of high-tech parts, for which the cost could still be justified.
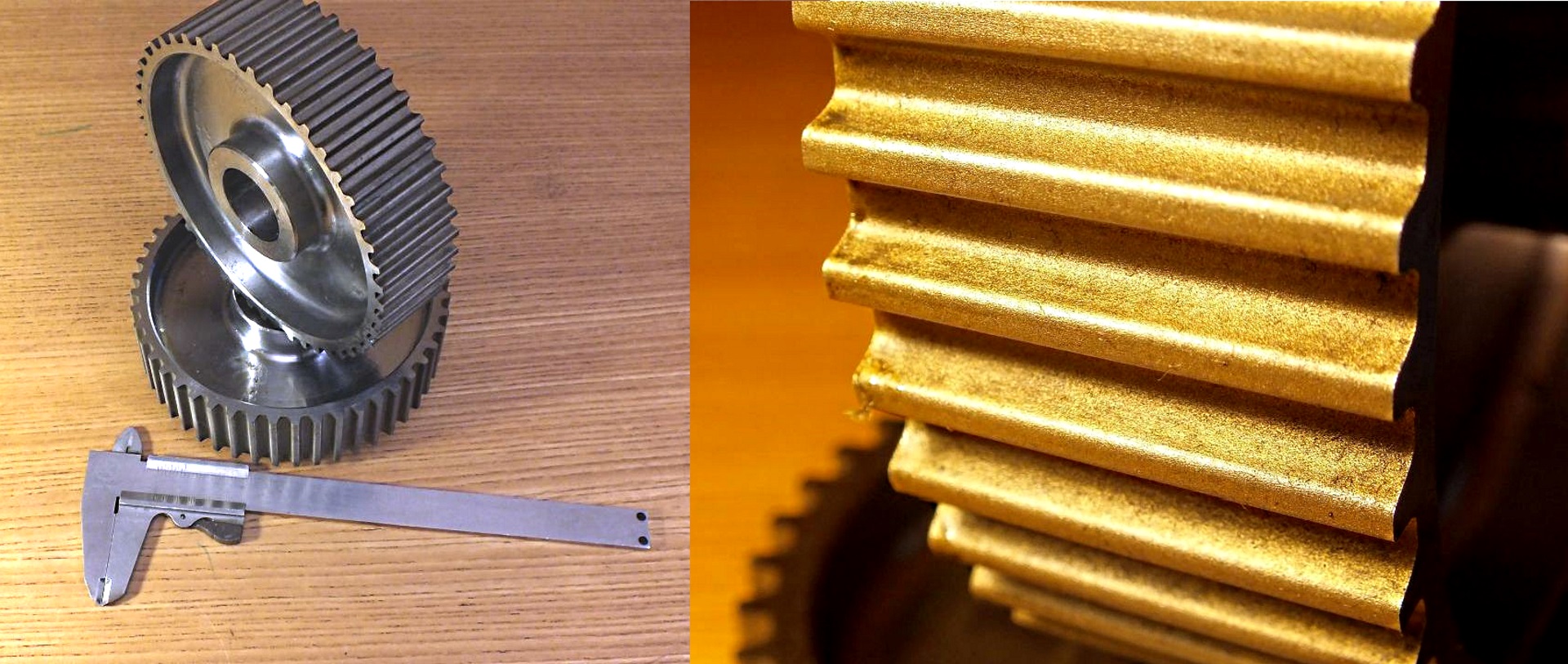
Ecut technology represents a further step, but acquires meaning only by changing some assumptions.
The ingenious idea of the roller that allows you to reuse the wire, leads to the substantial advantage of incredibly reducing operating costs.
In fact, if we consider that a large part of the mechanical workings fall within the tolerance of a few hundredths of a millimetre, that often a roughness of 3 Ra is more than acceptable, and taking into account this, the piece is redesigned, choosing and sizing the various parts accordingly, the result becomes very interesting.
Ecut and wire erosion are not really comparable at this point. They are actually complementary.
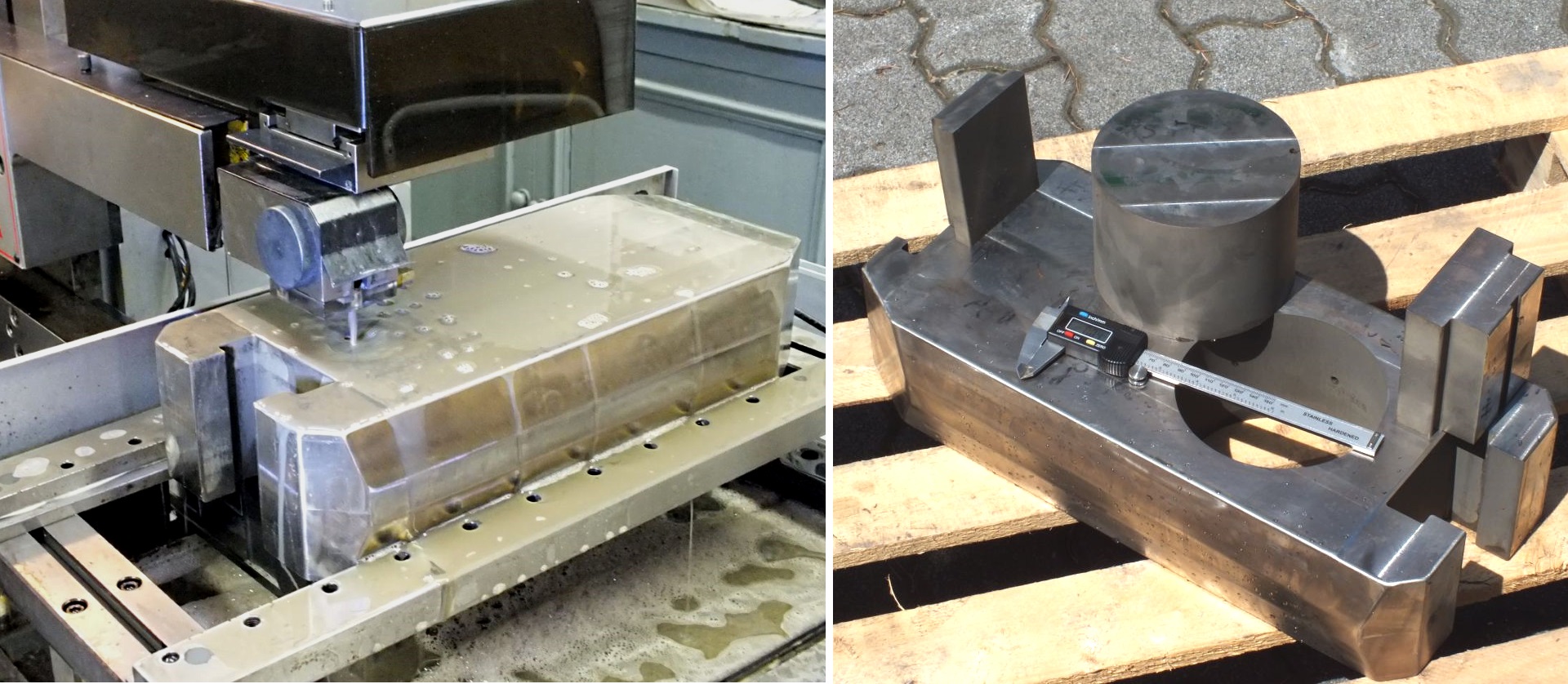
A lot of machining operations carried out with wire erosion can be carried out much more economically with Ecut.
Working cycles can be completely revised in the light of Ecut’s hourly operating cost (less than 0.5 €/hour compared to more than 10 €/hour for wire erosion).
Based on a steel removal speed of around 100 mm2 per minute, it will be easy to calculate how much a machining operation costs.
Cutting a 10 mm square by 10 mm (100 mm2) costs just a few cents, whatever the hardness.
In fact, the harder the material, the smoother and more velvety the surface will be.
Remember that the Ecut cut is finished! Burr-free, with sharp edges, and on pieces of any hardness and thickness.
Cold working does not deform or cause tempering!