Taglio settori di lame di presse piegatrici
Per esempio le lame delle presse piegatrici, oppure le lame delle pialle per il legno.
Il taglio a misura di spezzoni di pezzi gia’ temperati, o anche solo induriti in alcuni punti rappresenta un costo notevole.
Il taglio effettuato con dischi abrasivi non e’ preciso, e rinviene la zona di taglio. E’ necessario quindi lasciare un certo sovrametallo, con il duplce scopo di portare a misura tramite rettifica, e togliere la parte rinvenuta.
Il taglio e’ veloce, la rettifica un po’ meno, ma quasi sempre le due fasi sono attuate effettuate manualmente, e richiedono personale qualificato, nonostante la loro semplicita’.
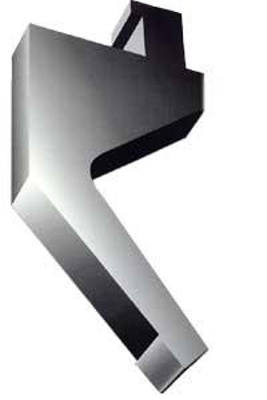
Spesso si utilizza l’erosione a filo, la quale ha il vantaggio di non fare rinvenire il materiale, ed ottenere un taglio preciso e geometricamente accurato. Il costo orario di esercizio, ( filo, acqua demineralizzata, resine scambiatrici di ioni, filtri,etc.), ne limitano grandemente l’impiego. Solo nel caso in cui la macchina sia senza lavoro, chiudendo gli occhi sui costi, la si utilizza per questo scopo.
E.cut rappresenta una soluzione rivoluzionaria! Oltre alle caratteristiche di una macchina ad erosione a filo, presenta alcuni notevoli vantaggi.
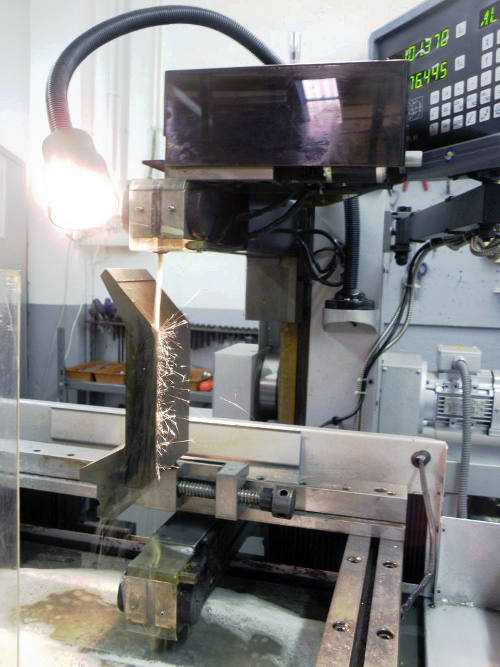
-Non si lavora ad immersione, quindi i pezzi possono fuoriuscire dal bancale.
-Lo spessore massimo di taglio e’ di 300mm gia’ dai modelli piu’ piccoli, permettendo di sovrapporre piu’ lame.
-Il costo orario di esercizio non supera i 0,4 €/ora, contro i 4 €/ora delle piu’ economiche erosioni a filo convenzionali.
-La gestione e la manutenzione sono estremamente semplici, e non necessitano di competenze specifiche.
-Il costo di acquisto di una Ecut e’ da 4 a 8 volte inferiore ad una erosione a filo convenzionale.
Sono realizzabili macchine che possono tagliare fino ad 800 mm di altezza.
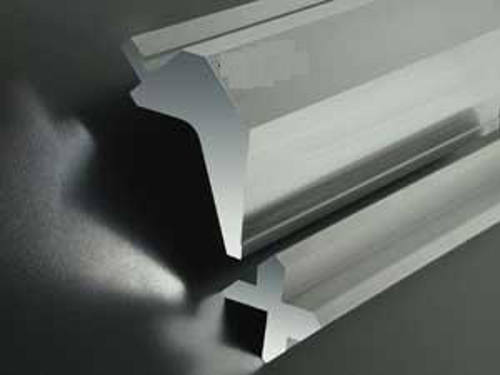