Con Ecut, si!
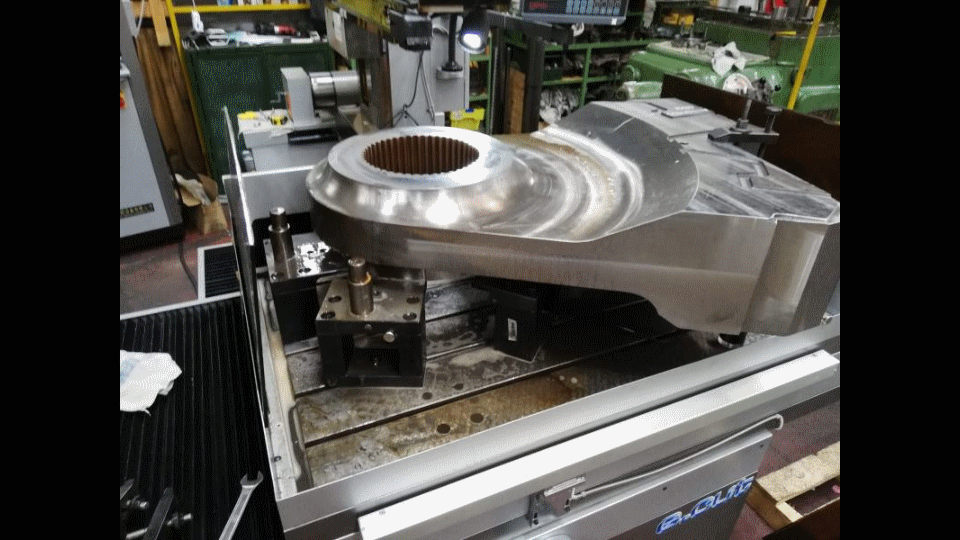
Grandi dimensioni
Su questo particolare di grandi dimensioni, ( oltre 2500 Kg. ) ed una parte a sbalzo di oltre 1000 mm, deve essere eseguita la dentatura interna. L’ esecuzione da parte di terzi, oltre al notevole costo richiesto da chi possiede una dentatrice adeguata, si scontrava con i tempi di consegna. L’ alternativa poteva essere l’ esecuzione con una erosione a filo, ma anche cosi’ i costi orari di una macchina simile sono proibitivi, per non parlare dei tempi di consegna.
La lavorazione eseguita con una Ecut 63D e’ costata incredibilmente meno rispetto all’ erosione a filo, ed anche meno rispetto alla dentatrice.
La mancanza della vasca ad immersione permette di posizionare pezzi di dimensioni anche molto eccedenti la tavola. La luce tra le teste di 500 mm, ( opzionali fino a 800 mm), consente di piazzare e tagliare pezzi di alto spessore.
La precisione ottenibile, entro 0,015 mm , ( +/- o,oo75 mm ), con rugosita’ anche inferiori a 1 Ra; la perfetta geometria delle parti lavorate, senza alcun effetto botte anche ad alti spessori e con alta velocita’ di asportazione, rende Ecut sempre piu’ diffusa nelle aziende produttrici di ingranaggi.
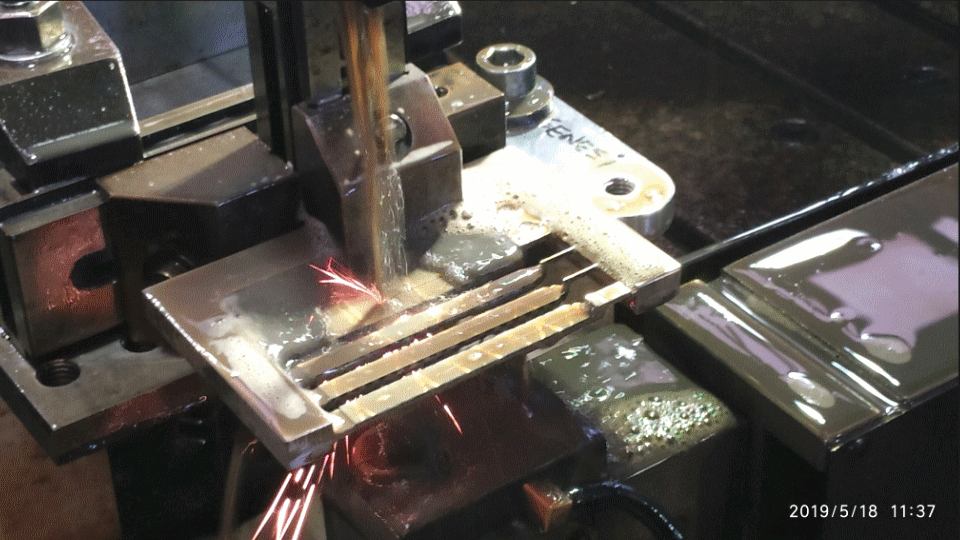
.
Aeronautica – Gas&Oil – Medicale – Automotive racing
L’ utilizzo di materiali metallici sempre piu’ sofisticati e’ sempre piu’ diffuso nei settori ad alta tecnologia. Forme sempre piu’ complesse per pezzi leggeri e resistentissimi vengono progettati considerando le grandi possibilita’ di macchine utensili a piu’ assi.
Si presentano pero’ alcuni problemi:
I materiali sono spesso duri o legati, quindi molto difficili da asportare di utensile.
Le macchine sempre piu’ sofisticate sono costose, e… delicate.
L’ erosione a filo e’ uno dei metodi per asportare piu’ materiale possibile, e lasciare un quantitativo minimo da finire di truciolo.
Ma l’ erosione a filo costa !
E.cut™, ha alcuni grandi vantaggi rispetto all’ erosione convenzionale:
1) Un costo di esercizio da 10 a 20 volte inferiore.
2) La mancanza di una vasca entro cui devono stare pezzi ed attrezzi di staffaggio. Cio’ implica la possibilita’ di lavoro in pendolare, caricando un pezzo mentre l’ altro sta tagliando, oppure l’ adozione di tavole girevoli, o divisori….
3) Grandi spessori di taglio anche per le macchine piu’ piccole, ( e meno costose ), con la possibilita’ di tagliare piu’ pezzi sovrapposti e ridurre i tempi di carico scarico pezzi.
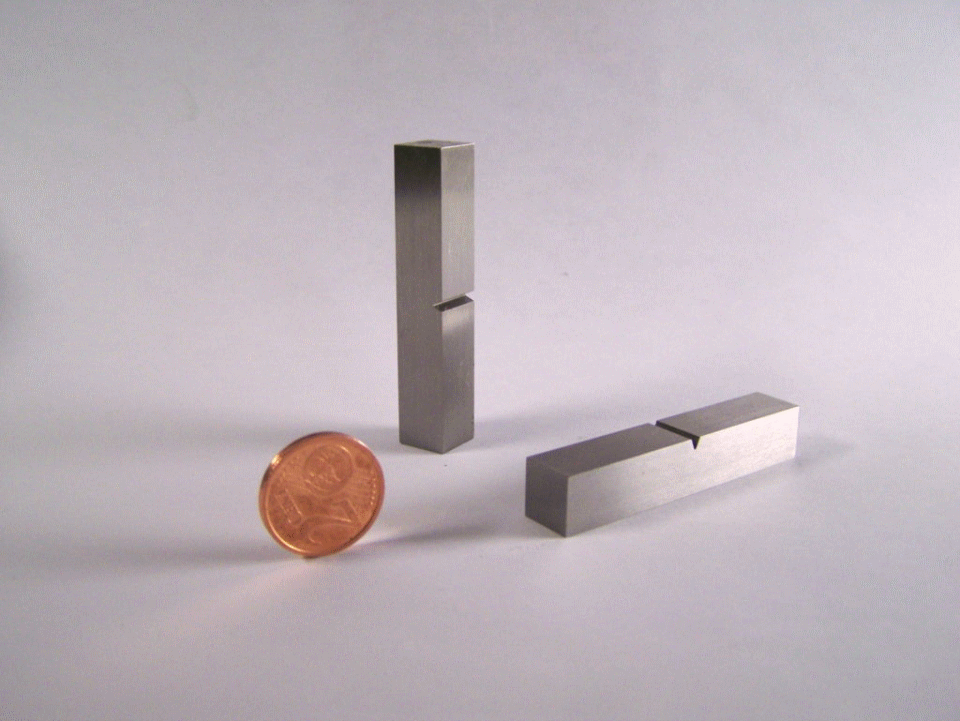
.
Provini di resistenza materiali
Fornire la certificazione dei materiali usati diventa sempre piu’ importante. Per ciascuna fusione, per ciascun forgiato, per ciascun semilavorato da cui si ricavera’ un pezzo, e’ sempre di piu’ necessario fornire l’ esito di prove di trazione, di resilienza, etc.
Ma i provini vanno ricavati !
Segare, tagliare, fresare, tornire… ed alla fine magari il materiale e’ stato “stressato”, ed il test non e’ piu’ probante.
Il costo poi schizza, specialmente se si tratta di materiali ostici, ( titanio, inconel, inox, etc.).
Ecut™ rappresenta la soluzione ideale.
Ad un costo incredibilmente contenuto si ottengono i provini finiti, o semifiniti, con precisione centesimale, senza stressare il materiale; e partendo da qualsiasi spezzone, fusione, piastra, laminato o forgiato.
L’ estrema semplicita’ del sistema di controllo di Ecut™ e la possibilita’ di archiviare un numero infinito di programmi per ogni dimensione o materiale danno la possibilita’ di adibire personale scarsamente qualificato.
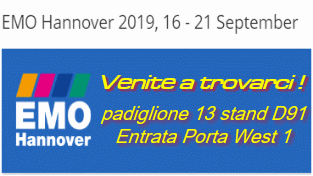